Introduction
Automation of industrial processes has tremendously changed our lives and is the main reason for the modern world’s wealth. It makes mass production possible and decreases the cost of the individual item, thereby offering benefits both for the producer and the consumer. On the producer’s side, we see a permanent race for faster processes, shorter production cycles and thus lower fixed costs in order to be able to offer competitive prices to the customer. Motion Index Drives has a strategic partnership with a prominent European cam indexing manufacturer and distributer, Taktomat, who has significantly contributed to this development with reliable and precise rotary index tables, transfer systems and various other products for over 30 years. Now, we are presenting a new version of our well-established LFA linear transfer system specifically designed to meet the requirements of modern manufacturing. This new design, crafted in collaboration with leading European academic institutes, allows to decrease the indexing time significantly compared to existing solutions, and to scale production to new levels.
Our LFA systems can be thought of as a chain with stiff chain links driven by a motor. Necessarily, there need to be curved parts, usually two U-turns or four 90◦ turns, for the chain to be closed. A sprocket is located in the curved areas, and is connected to a motor to drive the chain. Figure 1 shows a CAD drawing of the LFA HSP conveyor with two U-turns. A motor connected to a worm gear is located on each side to drive the chain. The typical shapes are linear as shown in Figure 1 and rectangular, but we have the design capabilities to manufacture more exotic shapes tailored to specific customer needs. Applications of these modules are vast and range from inkjet printing, packaging, filling, labelling to various applications in battery manufacturing. They can be used in intermittent (start-stop) or continuous motion mode.
High speed physics
From our experience, as well as from a thorough understanding of the physics, we knew that the motion along the straight line does not pose a problem. Indeed, in this part of the chain the only physical force acts between the chain links which is controllable by their mechanical connection. However, the behaviour is entirely different in the curved areas of the transfer system, where an additional force acts in the radial direction. It is well-known that this radial force is proportional to the second power of the velocity and the inverse radius. Now, when a chain link transitions from the straight line onto a proper circle, then there is a discontinuity, or a jump, in the radial force. If the chain was a roller coaster, then a person sitting in a cabin would get an additional hit by the sudden occurrence of the radial force, thereby causing significant discomfort. On the standard LFA chain conveyor designed for medium speeds we would see this discomfort in mechanical disruption and stress that would caused non-negligible wearing on short time scales. Thus, with our traditional approach we could not get over a certain speed threshold, as the mechanical design in the curved part did not cope with the instant change of the radial force.
The ideal turn - playing with physical forces
In order to circumvent these difficulties, our approach was to redesign the geometry and to transition from the straight line into the turn along a tailored mathematical curve that would allow to build up the radial force continuously.
In the case of the standard LFA transfer system, the chain leaves the sprocket, precisely when it gets onto the straight line. We just argued that this is not suitable for high-speed applications. So, we apply this new mathematical curve on the sprocket side in to lift the chain links out of the sprocket far before they get onto the straight line. Indeed, this can be observed in the actual built-up. In the first part of the transition, the ball bearings sit tight in the sprocket and do not roll. As soon as they reach a certain angle, they leave the sprocket and roll properly on the curve.
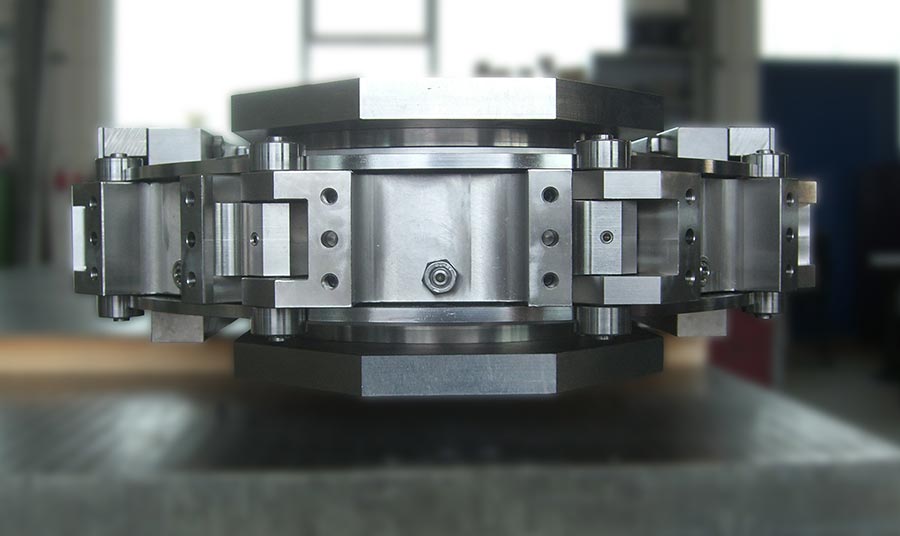
Figure 2
In Figure 2 it is shown how the ball bearings are lifted out of the sprocket as they transition from the curve into the straight line.
The curve is extended compared to a circle in the sense that the straight line does not start right above the centre of the sprocket. In fact, we managed to find a mathematical curve that also satisfies the constraints given by the chain, commonly referred to as polygon effect. Moreover, we chose a symmetric design, which allows to use sprockets and motors on both sides. In this case we can further decrease the indexing time by distributing the power for acceleration onto two motors. Our engineering department has a thorough expertise on coupling the two motors in the most efficient way and without ever compromising the accuracy of the system. Finally, adapted to the total load, we are able to suggest an optimal velocity profile, which makes the entire application more energy efficient. This makes the user of the transfer system save money on the fixed costs with every stroke.
Table 1
feed length [mm] | indexing time [ms] |
---|---|
150 | 203 |
300 | 268 |
450 | 328 |
600 | 382 |
750 | 443 |
900 | 499 |
1050 | 558 |
1200 | 625 |
1350 | 682 |
1500 | 738 |
Measurements and results
We tested our new LFA HSP system with two coupled servo motors and different loads of up to 200 kg distributed equally across all chain links. The tests were performed both for a vertical and a horizontal installation of the transfer system. Specifically, we applied different feed lengths to the system, optimised the acceleration and deceleration ramps to get the minimal indexing time. These are displayed in Table 1. We further saw that the minimal indexing time is essentially limitedly by the acceptable torque of the motor. The coordination of the two motors is crucial in order to achieve these results. In our tests we were able to distribute work on the two motors, so that the first motor is contributing 58% and the second motor 42% of the total acceleration power.
Acknowledgements
MH thanks Sigmund Kumeth for the initial discussion and essential contributions that led to a prototype of LFA HSP. Further, MH thanks the mechanical engineering team at Taktomat for the pleasant cooperation while working on this project.