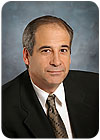
Less than half of all engineered products undergo any specific joint testing before introduction. While there are exceptions to every rule, I would argue that this is a big mistake.
The vast majority of companies that forgo planned joint testing haven’t come to that position by first trying it and then deciding there wasn’t any benefit. It simply wasn’t on their radar screen to begin with.
Why isn’t joint testing more common? I usually hear the following types of excuses:
“We’ve never done it, and never really thought about it.”
“We don’t need to test joints. Our suppliers recommend the right fastener and verify they meet spec.”
“We do test joints-whenever we have a production problem with them.”
Most companies subscribe to one of three different philosophies:
Certain production problems are inevitable. Organizations with this view limit their problems to an “acceptable” level and don’t have the time or resources to implement planned test programs. Death, taxes and loose screws are all part of life for engineers.
Fasteners are mature, pre-engineered solutions that don’t require additional engineering. While the vast majority of joining and fastening techniques are mature, a carry-over fastener in a new joint is a new joint. This is an important distinction.
When joint problems occur, focus on the fastener. In reality, this is rarely the root cause of the problem. When a change of fastener solves the problem, it is almost never because the initial fastener didn’t meet spec, but rather the replacement was a better application for that joint. Still, the takeaway in most companies is that the problem was a bad fastener, rather than a bad joint.
If you have decided to implement or enhance your joint-testing capability, how should you go about it? The answer depends on your company’s specific goals; your industry; and the joining and fastening techniques involved. But, to be successful, you’ll have to overcome two common problems: Getting valid test results early enough in the program and ensuring that test conditions are consistent with production realities.
When testing is dictated by a certain development gate, there is often difficulty in securing the required components in the required quantity. This leads to requests to use parts of a similar, but not intended configuration; to reuse certain parts to achieve the required number of tests; or to reduce the number of test runs.
These challenges occur in all facets of development. However, in my experience, it is generally not a case that the components are not available. Rather, the issue is usually that it is inconvenient, expensive or embarrassing to get the required components at the required time. So, be realistic in developing requirements for your test plan. And, be steadfast in requiring that all testing conforms to that plan.
Test conditions must also be consistent with what’s happening on the plant floor. For instance, if you’re testing adhesives, bond strength should be dependent on material surface conditions.
All testing should be controlled. But, when left up to the test lab, those controls tend to be around “ideal” conditions. The natural tendency is the desire to get “good” results. Instead, you should survey and quantify the range of production application and surface conditions. Then, replicate a point on the distribution of those conditions during testing.
Similarly, seemingly insignificant subtleties in the size, type and settings of screwdrivers and nutrunners can have a significant influence on bolted joints. For a number of economic and logistic reasons, production conditions often don’t match test conditions-even when this was the initial intent. As with part acquisition for testing, these disconnects can usually be eliminated by better communication, planning, and alignment of rewards and penalties between departments.
While the specific conditions facing your organization should determine what role joint testing plays, the quality of the decision-making process depends on the quality of information available and good insight into how that information is best used. Good luck formulating your plans.