Founded in 1937, oil-burner manufacturer R.W. Beckett (Elyria, OH) recently began implementing a lean approach to manufacturing to improve efficiency and profitability.
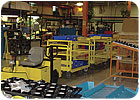
By using carts to transport work in progress, heating systems manufacturer R.W. Beckett has made its production space safer and more efficient.
Among other issues, Beckett managers found the company was not making optimal use of the space in its 165,000-square-foot plant. The factory floor was cluttered with wire containers filled with parts. Storage had become a challenge. Logistically, there were problems getting parts from the receiving area to the assembly line. Managers felt production could be streamlined and increased.
To remedy the situation, the company shifted from a traditional straight assembly line to a cellular model, with approximately five workers all facing the center of the cell. Unfortunately, there were problems with this setup, because whenever parts were delivered, workers had to turn around to unload them. The company’s lean managers quickly realized this could cause ergonomic problems as a result of all the reaching, turning and bending involved. Also, there were too many handoffs, causing worker downtime.
With these problems in mind, Beckett upgraded to a series of U-shaped work cells, setting up material “supermarkets” in the cells’ receiving areas, thereby changing the way materials were delivered to the floor.
As part of the new arrangement, Beckett implemented a number of delivery carts from K-Tec Inc. (Wickliffe, OH), which ultimately proved integral to the company’s improved workflow system. The carts can be pulled in a train by a tugger, skirting the perimeter of the work cells. An operator loads each cart in the parts supermarket, tugs three or more carts loaded with bins organized by cell number, drops the bins in designated chutes on a mobile cart and moves to the next cell. Shelves are clearly marked with the cell number. Carts allow for easy changeovers.
Working in the new U-shaped continuous flow cells and facing out, workers can now perform a task or series of tasks and then slide the product to a coworker until the product is finished. The improved flow within the cells has made it possible to reduce the number of workers in each cell from five to four.
Additional benefits include a 10 percent overall space savings; an 85 percent inventory reduction; a decrease in line-side inventory from 2 days to 2 hours; improved ergonomics, with parts all within 18 inches of workers; and a reduction in forklift traffic.
Partly as a result of the new system, the company has not had an OSHA-recordable injury for over a year.
For more on small parts delivery and material flow, call 440-943-4111 or visitwww.ktecinc.com.