At the DaimlerChrysler (Stuttgart, Germany) plant in Bremen, Germany, it is the Body-In-White (BIW) Rollout and Process Optimization Department that makes sure everything goes together correctly.
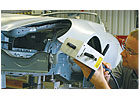
A technician at the DaimlerChrysler plant in Bremen, German, uses a laser tracker to inspect the dimensional accuracy of the left fender on a Mercedes SLK body-in-white.
“Our job is to assure dimensional accuracy of the entire body-in-white,” says operational engineer Henning Siemers. “Of course, every BIW consists of many individual parts, and they must all fit perfectly. Our primary duty is to inspect the entire BIW, both individual parts and the whole vehicle, including the panel gaps, and then analyze the data we get. Based on the analysis we perform, we then go back to the production facilities and make adjustments to the tools and make sure that what comes out is an automobile whose parts fit together flawlessly.”
In the past, the BIW department relied on hand-operated measurement instruments. However, these kinds of tools are no longer adequate for today’s automotive production standards.
“Viewed in retrospect, cars used to be made of almost square-like segments, which used to fit nicely together without much hassle. Nowadays, cars are much more curvaceous, with round areas suddenly changing shapes and meeting other panels at all kinds of angles and lines,” Siemers says.
To solve the problem, the Bremen BIW department purchased an LTD840 portable laser tracker coupled with a T-Probe and T-Scan from Leica Geosystems (Norcross, GA) to do everything from measure panel gaps to examine part curvatures and inspect reference holes. The system is portable, modular and capable of taking measurements at a range of up to 15 meters. This gives technicians a total measurement envelope of 30 meters.
“One of the new applications we have found is in-line calibration,” Siemers says. “The new Mercedes C-class is built modularly on a pallet, and the BIW is taken from station to station…. When you have 150 pallets [to calibrate] and want to measure with high tolerances, you’re quickly reaching the limits with traditional methods.”
According to Siemers, DaimlerChrysler is also looking at using its laser trackers to inspect and fine-tune the movements made by company’s assembly robots.
“By relying on scanning, I am in the possession of much more useful information. The quality of part analysis has improved. We are able to get to the root of a problem much more quickly, therefore coming up with targeted solutions for what needs to be changed,” Siemers says.
He adds that being able to transport the system from station to station means the BIW department can do its job without slowing down production.
“We really appreciate the portability,” Siemers says. “With the Leica Geosystems equipment, I can gather all the information I need in just 2 to 3 hours and perform the analysis later. This way, I am not blocking production for too long, because the system lets us work in parallel. While one operator is taking the measurements, another one can already be working on sorting out the results.”
For more on laser trackers, visitwww.leica-geosystems.com/usor call 800-367-9453.