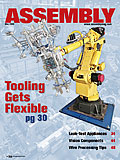

Frame-based EOAT has long been used for machine tending. Photo courtesy ABB
In the beginning, end-of-arm tooling was the exclusive purview of robot manufacturers themselves. However, the industry has since evolved to where a number of companies now specialize in robotic tooling, in the process providing engineers with increased functionality, greater ease of use and lower prices.
Among other products, EOAT equipment manufacturers offer a host of different modular systems and components, including brackets, clamps and connectors used to hold together a framework of slotted or tubular aluminum sections. Carbon-fiber sections are also available for especially weight-sensitive applications. This framework is then used to secure the suction cups, magnets, pumps, grippers, slides, guides and even sensors that serve to grasp, manipulate and ultimately release the actual workpiece.
Specific examples of this kind of tooling include the BodyBuilder, CPI and SpiderGrip lines from workholding and automation company DE-STA-CO (Auburn Hills, MI); the Vacuum Spider line from Schmalz Inc. (Raleigh, NC); a comprehensive line of modular tooling, including profiles, grippers and clamps from SAS Automation LLD (Xenia, OH); the press automation equipment line from robot-maker ABB (Auburn Hills, MI); and the Modular Automation Tooling line from vacuum equipment manufacturer PIAB USA (Hingham, MA).
In spite of their occasionally ungainly appearance, frame-based end effectors offer an appealing combination of light weight, rigidity and adaptability. On the one hand, end users can often fine-tune their own EOAT equipment in-house, using tools as basic as a simple hex wrench. On the other, by mixing and matching standardized components, assemblers, systems integrators and robotics companies can easily create an infinite number of different EOAT, using expensive customized components only as a last resort.
“Most all industries have used some sort of modular EOAT for quite some time now, but just within the last 10 years have the aluminum tools become a major competitor due to price and weight,” says Tom Herndon, regional sales manager for Schmalz Inc.
“Modular and flexible end-of-armtools, grippers and end effectors help the robot to do more,” agrees Trent Fisher, PE, president of SAS Automation. “Modular systems give the integrator the flexibility to…meet their ultimate goal of reducing production costs while increasing speed to market.”
In particular, modular, framed based tooling enables manufacturers to set up their own EOAT that much more quickly and then perform on-the-fly changes once the tooling is in production. “Both help reduce downtime,” says PIAB applications engineer Andy Lovell.
Jesse Hayes, automation production manager for gripper manufacturer Schunk Inc. (Morrisville, NC), notes that his company has even built EOAT that self adjusts depending on the part being manipulated. “We installed a vacuum gripper on the end of a slide to automatically configure to another part,” he says of the system.

Today’s modular systems make it easy to both build and adjust a robot’s EOAT. Photo courtesy Schmalz Inc.
Molding and Manipulation
Given the planar nature of an extruded aluminum framework, it should come as no surprise that frame-based EOAT systems have long been used for packaging and machine tending in the stamping and injection molding industries. Whether it’s feeding galvanized sheets to a press, or removing and manipulating molded cell phone housings, multiple suction cups or mechanical grippers are a natural. The same thing goes for packaging, whether the product being handled is the bumper for a pickup truck or a couple of dozen boxes of breakfast cereal.What is not so obvious is the fact that these seemingly routine tasks are often surprisingly difficult to execute. In many cases, it’s important the robot not mar the finish of the product being processed. In others, actually removing the part, or parts, from the mold can be problematic, especially if the mold wasn’t built with automation in mind. In fact, reach and extraction issues are one of the reasons human operators continue to tend machines in countless factories across the world.
Then there are those applications in which a single robot is required to perform more than one task: for example, transferring a molded or stamped part to another automated workstation for some kind of processing; or manipulating a component so that it can be effectively and safely packaged.
As an example of this kind of application, SAS engineering manager John Westbeld cites the case of a manufacturer that was using a robot to transfer molded electrical panels directly from the mold to a divided container. In addition to the challenge of having to accommodate the parts’ porosity, SAS engineers had to overcome the fact that the distance between the mold cavities was greater than that of the packaging.
The solution consisted of a frame-based gripper equipped with a slide assembly that brings the panels closer together after they are removed from the mold. The EOAT was also equipped with a photoelectric sensor to confirm part presence and ensure quality.
In response to applications like these, EOAT equipment manufacturers have created a dazzling array of interchangeable components, including larger and smaller extrusion sections, adjustable clamps, junction boxes and relay boards. In addition, EOAT builders are increasingly creating “hybrid” systems employing a combination of magnetic, vacuum and finger grippers to meet the needs of especially demanding applications. The resulting systems can perform tasks that might otherwise only be possible for a human being. They may also be able to perform multiple tasks using a single gripper.
“An example of this in packaging is a multifunction gripper with one area of the robotic gripper [using] vacuum cups to secure products such as totes or boxes and another area of the gripper utilized for the moving of pallets with gripper fingers,” Fisher says. “This type of a multifunctional gripper pushes the efficiency envelop while reducing costs as only one robot and one gripper handles both loading the product and the placing of a new pallet to begin the next palletizing cycle.”
Along these same lines, Schunk’s Hayes cites the EOAT his company helped build in which mechanical grippers were used to do the actual lifting while vacuum cups kept the part stable. In another application, Hayes says a single tooling system employed vacuum to pick up one kind of component and a finger gripper to pick up another. The two parts were then simultaneously placed in a workstation for processing.
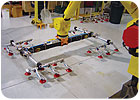
This EOAT incorporates both aluminum and carbon fiber components to make it as light as possible. Photo courtesy DE-STA-CO
EOAT Considerations
No matter what the specific application, when designing and fabricating frame-based EOAT, assemblers need to keep in mind many of those same concerns that apply when integrating any other type of robotic tooling.For example, as is the case in any robotic application, it is important to anticipate the loads that will be generated by the workpieceandthe tooling when the robot is doing its job. When working with larger frame-based EOAT, in particular, it is critical that builders figure out torque and moment values in advance to avoid problems with quality and repeatability down the road.
“The gripper mounting location [relative] to the robot must be selected to minimize excessive torque or moments for the least amount of stress and strain. It is best to use components that allow flexibility [so that] the designer can easily select the best mounting location, typically either center or end-boom,” Fisher says.
Along these same lines, it pays to go with the lightest gripper and framing components possible and not “overkill” the application with heavy, fixture-type tooling. In addition to reducing robot wear and tear, lighter components will also enable faster cycle times.
“Keep it simple. Talk to the people who will be using this tooling every day for practical feedback,” says DE-STA-CO vice president of engineering Robert Pitera. “Always be aware of the weight expectation of the robot.
Whether an in-house design team is capable of making these kinds of decisions depends on the complexity of the application, says Schmalz Inc.’s Herndon. However, he notes it is often worth the effort, if for no other reason than that it provides the manufacturer with an added degree of control. “Some [EOAT systems] are built on-site by end users who have a good inventory of the modular parts,” Herndon says. “This enables them to change tooling on the fly as major part changes are made.”
Of course, manufacturers also need to be careful not to overreach themselves, especially when working with trickier parts or assemblies. According to PIAB’s Lovell, these include packaging applications in which there is no standard case size, or automotive applications in which there is substantial variability in the parts being handled.
“It is important to have experience in designing tools with an understanding of the robot payload and part manipulation needed,” agrees Fisher. “Anyone designing tools needs to understand the automation required, in order to design the tool appropriately and cost effectively.”
“Many of our products are off the shelf and easy to use,” agrees DE-STA-CO’s Pitera. “However, we have shown tremendous payback by building the tools ourselves and then shipping them to integrators for install.”
No matter what the specific tooling and application, engineers need to remember that even the most flexible system in the world will have its limitations. Not only that, asking too much of a specific piece of tooling can quickly backfire due to breakdowns or compromised product quality.
Nonetheless, Herndon says in the future, framed-based EOAT, like so much in modern manufacturing, is only going to get better and easier to work with. “I think the future will hold lighter and more adjustable tools at an extremely reasonable price,” he says. “There will also be tools that can be adjusted automatically to handle any product, no matter if it’s a box, a bumper or a cell phone face plate.”