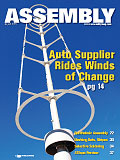
Not that long ago, MasTech Manufacturing in Manistee, MI, was riding high. A supplier of conveyors, material handling equipment and welding cells for the automotive industry, the company had won some major contracts, including lines at Freightliner in Cleveland, NC, and BMW in Spartanburg, SC.
But then the automotive industry hit the skids. MasTech’s workforce went from approximately 50 people in mid-2008 down to just three. If the company were to survive, it would have to diversify. So, when Reno, NV, startup Mariah Power went looking for a manufacturer to build its new wind turbine for residential and light commercial use, MasTech leapt at the opportunity.
It signed a contract with Mariah Power in December 2008, and began converting its 30,000-square-foot facility to make the turbine, a vertical-axis design called the Windspire. All totaled, MasTech spent some $1.5 million on new equipment. “We built robotic [and] manual welding tools,” says John Holcomb, MasTech’s general manager. “We built custom material handling equipment and racking. We bought new machine tools.”
Production began in April. Since then, the company has been assembling 100 turbines per month-a number that could increase to 1,000 per month within a few years. MasTech has shipped Windspires throughout the United States, as well as internationally, including Israel, Denmark, France and the Netherlands.
The company has hired back all the employees who were laid off, and even added a few more. By the end of 2009, the company could have a workforce of 75 to 80 people. “By the end of next year, we hope to employ approximately 120 people,” says Holcomb. “If we start selling more overseas, we could potentially have 500 to 600 jobs in five years.”
The Windspire is 30 feet tall and 4 feet wide. It includes a high-efficiency generator, an inverter, a hinged monopole and a wireless performance monitor. The 1.2-kilowatt machine will produce approximately 2,000 kilowatt-hours per year in winds averaging 12 mph.
From the start, MasTech included local suppliers in the endeavor. The turbine’s aluminum airfoils are produced by Whitehall Industries Inc. in Ludington, MI. Steel parts come from Alro Steel Corp. in Jackson, MI. The inverters are assembled by Amptech Inc. in Free Soil, MI. Boxes and crates are made by Norton Packaging Corp. in Grand Haven, MI. At least three other Michigan companies are also part of the supply chain.
“It’s been our desire since Day 1 to make the largest economic impact in the smallest geographical area,” says Holcomb. “The only components that come from outside the United States are the rare earth magnets, which come from China, but that’s where neodymium is mined.”
Holcomb emphasizes that his company’s turnaround should not be considered unique. “We’ve proven that, given the right tools and the right attitude, American workers can compete in the global market by supplying not only a cost-effective product, but a superior product,” he says. “Anyone can do it. We have the technology. If we reapply it and leverage it in new, innovative directions, we can compete with anybody.”
Editor’s note: With all the news of bailouts, layoffs and plant closings, it’s all too easy to think every manufacturer is stuck in the doldrums. In fact, there’s plenty of good news in manufacturing-if you take the time to look. “Moving Forward” is dedicated to new or expanding assembly plants. If you know a facility that’s opening, growing, investing in new equipment, or simply going great guns while everyone else is treading water, we’d like to hear about it. Send an e-mail to John Sprovieri, editor of ASSEMBLY, at sprovierij@bnpmedia.com, or call 630-694-4012.