Modern assemblers owe a debt of gratitude to a Yankee craftsman born in 1781.
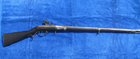
Producing interchangeable parts lies at the heart of modern manufacturing. Without the ability to join mass-produced parts, fed randomly from bulk supplies, most product assembly as we know it today would not exist.
Predictably, the driving force behind the quest for interchangeable parts came from the need to repair military firearms in the field. Before the 18th century, firearms were made one at a time by skilled craftsmen, and each one was unique with components that fit only that firearm. If a component failed, the entire gun was sent back for repair or scrapped.
In the late 18th century, French gunsmith Honoré le Blanc fabricated musket parts to what were then termed “allowable tolerances.” He demonstrated their interchangeability by assembling muskets from parts picked at random from bins. However, the French government-fearing it would lose control over the old crafts-buried the idea.
Eli Whitney picked up on le Blanc’s idea and gave a similar demonstration in America, which brought him a government contract for muskets. But Whitney was faking it-those demonstration parts were handcrafted by skilled workmen. The musket parts delivered under the contract weren’t interchangeable; Whitney never designed a process capable of producing interchangeable parts.
The man actually responsible for turning the principle of interchangeable parts into everyday practice was John H. Hall. Born in Maine in 1781, Hall had an interest in firearms and-ever the Yankee craftsman-had long sought to improve the muzzle-loading firearms of the day. Taking a novel approach, Hall designed a breechloading rifle that was significantly faster to reload than any muzzle-loader. He set up a business to make them, and although he received a government contract for his Hall Breechloaders, he was obliged to turn it down. The delivery date was impossible to achieve because at that point, Hall and his workmen were still handcrafting parts.
Hall observed that this handcrafting was the major impediment to increasing production speed, says Alexander Rose in his recent book American Rifle: A Biography. Hall then deduced that the solution was to eliminate the inevitable variations among handcrafted parts. This would allow rifles to be rapidly assembled from heaps of identical and interchangeable parts.
Because variations resulted from the human factor, the obvious solution was to replace people with machines. That such machines didn’t exist wasn’t a deterrent; Hall set out to design them. The real deterrent was money; he was nearly bankrupt. Hall boldly proposed to the government that he would manufacture rifles with interchangeable parts if he were awarded a sufficiently large contract.
By a fortuitous coincidence, the U.S. Army launched a major reorganization of its arms production facilities following the War of 1812, and Hall was appointed to establish the Rifle Works at the armory in Harpers Ferry, WV. Now Hall could make good on his proposal. It didn’t happen overnight, but he ultimately delivered thousands of breechloaders.
In his paper The Hall Breechloader: An Early Example of Concurrent Product and Process Design, David J. Williams shows that Hall not only addressed the problem of manufacturing interchangeable parts, he simultaneously addressed the challenges of designing the machines and production process for making the parts, and designing the rifle itself for easy manufacture. We can thus conclude that Hall was likely the first practitioner of these manufacturing practices that we take for granted today.
We owe much to this Yankee craftsman. Mechanics and managers who worked at the Rifle Works carried the principles of interchangeability and design for manufacture far and wide, establishing America as the manufacturing leader it is today.