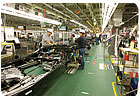
It’s just a piece of paper. But, it’s one of the most effective lean tools available to manufacturing engineers. An A3 report is a generic name applied to a document written on a large sheet of paper. It refers to the international standard for 11-by-17-inch paper.
The A3 process is a Toyota-pioneered practice of getting a problem, an analysis, a corrective action, and an action plan written down on a single sheet of large paper, often with the use of simple graphics. The automaker uses it as a powerful lean management tool.
A3 thinking is the process by which Toyota identifies, frames, and then acts on problems and challenges at all levels. According to John Shook, a Toyota veteran and president of TWI Network Inc., a consortium of lean manufacturing consultants, A3 reports form the heart of lean management. “The A3 process standardizes a methodology for innovating, planning, problem-solving, and building foundational structures,” he points out. “[The goal is] a broader and deeper form of thinking that produces organizational learning that is deeply rooted in the work itself.
“Toyota creates engaged and analytical employees through the process of solving problems,” says Shook, who recently wrote a book on the subject entitledManaging to Learn(Lean Enterprise Institute). Shook calls this approach, which is captured in the simple structure of an A3 report, “the key to Toyota’s entire system of developing talent and continually deepening its knowledge and capabilities.”
Toyota uses A3 reports for problem-solving activities, status reports and proposals. “The tool captures part of the Toyota thinking pattern that the company tries to teach to employees early in their careers,” says Art Smalley, president of the Art of Lean Inc. “In other words, problem-solve clearly and communicate effectively. Don’t waste other people’s time.”
According to Smalley, a former Toyota engineer, the automaker urges employees to use A3 reports to structure thinking and tell a concise PDCA (Plan-Do-Check-Act) story, generate discussion with supervisors or other departments for feedback, and mentor employees in problem-solving skills.

A Basic Communication Tool
Smalley says A3 reports are effective because they’re so basic in today’s high-tech world of e-mail, texting and social media. “As communication has gotten easier the past couple of decades, we have become really lazy with regards to effective communication,” he explains. “Too many hours are spent on e-mail or in poorly organized meetings on items that don’t add value or don’t foster communication effectively.“A3s take time to write, but they provide useful information in a very succinct manner,” adds Smalley, who recently coauthored a book on the topic calledUnderstanding A3 Thinking(Productivity Press). “They are not for every communication, but for things that will have some impact or shelf life.
“You can tell in two to three minutes if an A3 is well thought out and if it should be granted discussion time by senior managers or leaders,” claims Smalley. “If not, then you send the author back to get the facts and details better organized.”
While A3 reports are not new, they have recently become popular with manufacturers. “There’s a growing frustration in many companies with the inability to really solve problems,” explains Durward Sobek, an associate professor of mechanical and industrial engineering at Montana State University and coauthor ofUnderstanding A3 Thinking. “The A3 process cuts through the fog of data and information that overwhelms people today.
“Somehow, we have substituted quantity of information in place of quality of communication in recent years,” laments Sobek. “The A3 process is also popular because it doesn’t require expensive training sessions or software programs.”
“An A3 report provides a good template for organizing information,” adds Matt Zayko, an associate at the Lean Transformations Group. “It forces you to capture and disseminate lots of facts and data on just one page vs. a 40-page PowerPoint presentation.”
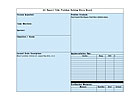
Every A3 Report Is Unique
Unfortunately, the sudden popularity of A3 reporting has led to numerous mistakes in the engineering community. “Anything foreign and mysterious is prone to misunderstanding,” explains Smalley. “In reality, an A3 report is just good problem solving and application of the scientific method with effective communication techniques, such as quantitative charts, rather than words.
“The reports can take a while to learn how to write, so they are often not so effective for some people in the beginning,” Smalley points out. “Also, there are endless flavors or possibilities concerning the types of A3s that can be written. Sometimes, people see one type and latch onto it as the only way to write the report. It winds up being the hammer and the nail problem.”
“Many people are missing the point of A3 report writing,” adds Drew Locher, managing director of Change Management Associates. “They see it as strictly a communication device and not as a problem solving, process improvement and management tool.
“The true benefit to crafting A3s is not in the single-page document that typically results, but in the process of creating it,” notes Locher. “A3 writing is about storytelling. The story can be about a problem that is being addressed, a project that is underway or even a business strategy to address some performance issue.”
Contrary to popular belief, most A3 reports don’t follow the same outline and look alike. “You’d struggle to ever find two that looked alike,” says Sobek. “Other than the fact they fit on one sheet of paper and have common sections, they are usually quite different when you read the content.”
While A3 reports should follow a basic template, the exact format and wording are flexible. Most organizations tweak the basic design to meet their unique requirements.
According to Sobek, the exact structure depends upon the type of A3 and the needs of the situation. A typical report contains seven main elements that follow one another in a natural and logical sequence: Background; current situation and problem; goals and targets; root cause analysis; action items and proposed implementation plan; verification measures; and followup. An A3 report should always address both current condition and target condition. In addition, all information should flow and be relatively simple.
The type of information contained in an A3 depends upon the purpose of the report and the audience. “The information in an internal problem-solving A3, for example, should contain the basic information required to explain the background, current condition, main problem definition, root cause analysis, countermeasures, action items, confirmation method, and any important follow-up topics,” says Smalley.
“We used to talk about the T-shaped manager at Toyota,” adds Smalley. “[That’s someone who is] broad at the top, yet able to dive into details as needed. A good A3 is like that, as well. It covers the content broadly, but is able to communicate the few real important details about the problem, the root cause, confirmation of effect or key follow-up items. It should not contain 100 pages and force the reader to search for the necessary information-that is inefficient and inconsiderate.”
Most experts recommend creating A3 reports in pencil, because it’s easy to erase things and start over. “There’s never been an A3 report I’ve written that was right the first time,” notes Kirk Paluska, a consultant with the Lean Transformations Group. “A pencil is good, because you can easily make changes and move things around.”
“I did my first A3 at least a dozen times before I got an acceptable format,” adds David Verble, a former manager at Toyota’s Georgetown, KY, assembly plant and a current faculty member at the Lean Enterprise Institute. “It takes a while to learn the story board format. Questioning is key. You have to ask yourself ‘What do I really know and how do I know it?’”
To be effective, the A3 process requires a different pattern of thinking than people may be used to. “It requires you to be like a crime scene investigator,” claims Sobek. “You’d be surprised how much you can communicate on a single page once you put your mind to it and eliminate the unnecessary information.”
One of the easiest traps that novices fall into is treating an A3 report as a fill-in-the-blankws tool. “Don’t be deceived by the simplicity,” warns Verble. “It’s not about filling in boxes. It takes a lot of work; you have to be patient.” A
To learn more about A3 reports, click www.assemblymag.com and search for these articles:
- A3 Mistakes to Avoid.
- Glossary of Lean Manufacturing Terms.
- How to Write an A3 Report.