When we asked riveting suppliers to tell us their most challenging applications, we received dozens of reports on everything from surgical instruments to wood-burning stoves.
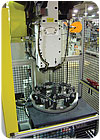
Rivets of one form or another are used in a wide range of applications, from truck trailers and air bags to staplers and circuit board assemblies. As the following reports show, manufacturers are using rivets to solve diverse assembly challenges.
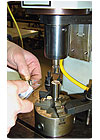
An orbital forming machine rivets a small steel disc to a clear, plastic lens. Because of its gentle action, orbital forming was the perfect riveting method for this application. Photo courtesy Orbitform
A Riveting Method "Unmasked"
Carpenters and orthopedic surgeons share a disturbingly similar toolkit: power saws, power drills, and hammers. And just as safety-conscious carpenters wear protective glasses, so too do prudent orthopedic surgeons wear face masks or shields to protect themselves from flying bits of blood and bone.Recently, a medical device manufacturer designed a hood that protects the surgeon’s entire head. The hood features a wide plastic lens that can be easily removed and replaced, without fussing with snaps or zippers. Steel targets fastened to the lens correspond with magnets sewn into the body of the hood. The magnets provide enough attraction to hold the lens securely in place, but not so much that the lens cannot be stripped off and replaced quickly.
The challenge of this application was how to attach the steel targets to the lens. Some methods would smash the plastic. Others did not provide a rivet with the right configuration or appearance for the job.
An orbital forming machine from Orbitform (Jackson, MI) provided the solution. Orbital forming is a cold-forming process in which an orbiting tool held at a fixed angle progressively moves malleable material into a predetermined shape. Orbital forming machines can form heads on rivets, studs, pins, shafts or tubes. These can be round, square, oval, rectangular or D-shaped. The process can be used on most malleable materials, including ferrous and nonferrous metals, stainless steel, die-cast zinc and aluminum, and even some thermoplastics.
“Orbital riveting is very gentle,” says Pat Beach, inside salesperson at Orbitform. “To upset a rivet with an impact riveter, you need to put a lot of tonnage over the rivet, and the body of the rivet will compress with one big ‘bang.’ You can’t really control that. With orbital forming, you can control the depth and diameter of the head form. Plus, it doesn’t apply a lot of force to the target. The forming is done in increments.”
To secure the steel targets to the lens, Orbitform’s application lab designed a special semitubular steel rivet that is 0.25 inch long and 0.625 inch in diameter.
"What was remarkable about this application was the short time frame," says Beach. "Within a few weeks, we helped the customer define the rivet and produced some samples."
For more information, contact Orbitform at 517-878-9447 or visit www.orbitform.com.
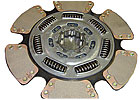
Riveter Makes Impact on Clutch Assembly
Impact riveters have been assembling automotive components for decades. So, when an automotive supplier came to Orbitform looking for an impact riveter to assemble clutch plates, there was nothing particularly challenging about the application. But, when the supplier wanted the machine to assemble multiple models of clutch plates and assist operators with loading and unloading, now that was a challenge.A clutch plate is a thin, steel disc. Its center is connected to the transmission input shaft by a grooved hub. The disc is covered with a material similar to brake linings. This material allows the clutch to slip smoothly and quietly. Arrayed around the circumference of the plate are three to six ears, or paddles. Each ear is attached to the plate with four semitubular steel rivets.
Initially, the supplier used a single semiautomatic impact riveter to attach ears to the plates. However, after loading the parts into the machine, the operator had to pick up and move the assembly to a new fastening location each time a rivet was installed. Thus, for a six-paddle clutch plate, the operator would lift the part 25 times-24 for each rivet and once more to unload the finished assembly. A dual-head riveter that could install two rivets at a time improved productivity somewhat, but it was still less than ideal.
Orbitform’s engineers came up with a better way. The heart of the new system is an Adtech QRHV 5000 impact riveter that installs all four rivets in an ear simultaneously. To further increase productivity, the fixture for the clutch plate is mounted on a servo-controlled rotary indexing table. Now, the indexer turns the clutch plate to the next riveting position, not the operator. When the assembly is finished, a pneumatic cylinder below the indexer lifts the finished assembly out of the fixture. The operator still has to load and unload the machine, but it’s now a much more ergonomic operation.
“Loading and unloading the parts put a lot of stress on the forearm. The pneumatic cylinder helps the operator pick up the parts,” explains Beach.
Because the indexer is servo-driven, the machine can be programmed to assemble clutch plates with either four or six ears. The operator just has to swap out fixtures and press a button for the new program. “With a cam-driven indexer, the number of stops would have been fixed,” says Beach. “With the servo-driven indexer, you can change the number of stops automatically.
“The new system took a job that was a pain and made it kind of fun.”
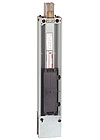
Self-piercing rivets were used to assemble the aluminum housing of this electrical busway. Riveting was faster and more cost-effective than using threaded fasteners. Photo courtesy Henrob Corp.
Self-Piercing Rivets Assemble Busway
An electronics manufacturer designed a new power busway housing. The two halves of the housing were made of prepainted extruded aluminum. The manufacturer had assembled similar products with nuts and bolts. However, punching holes in the aluminum added cost. And, because the holes had to be slightly oversized to provide adequate clearance for the bolts, the housing halves could slip in relation to each other.The manufacturer wanted to automate assembly and lower the in-place cost of fastening. Self-piercing riv-ets from Henrob Corp. (Novi, MI) were the answer. Self-piercing riveting is a cold joining process for fas-tening two or more sheets of material by driving a rivet through the top sheet and upsetting the rivet, under the influence of a die, into the lower sheet without piercing it. The sheets can be metal or plastic, coated or uncoated. An additional layer of material, such as an adhesive or sealant, can be included between the sheets. The process is fast and quiet. The average cycle time is 2 seconds.
To assemble the housing, Henrob provided two preclamping rivet setters mounted in an O-frame, explains Dean Monday, national sales and marketing manager at Henrob. The setters simultaneously insert two 5-millimeter countersunk rivets, which are fed from spools. The setters have long nosepieces to access nar-row troughs at the base of the housing. Preclamping of the parts in the O-frame ensures that the housing halves are completely flush with each other for incremental riveting.
As an added benefit, the self-piercing rivets provided better grounding between sections of the housing. The new assembly passed stringent short-circuit testing according to UL requirements.
For more information, contact Henrob at 248-344-0032 or visit www.henrob.com.
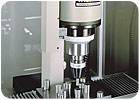
This orbital riveting system forms heads on multiple stainless steel rivets for a laparoscopic surgical instrument. The heads must be formed precisely to enable the assembly to swivel smoothly. Photo courtesy Taumel Assembly Systems
Riveter Ensures Instrument Can Move
A manufacturer of laparoscopic surgical instruments needed to rivet multiple parts together so they could swivel with a smooth, precise motion. The parts were made of plastic and fine-blanked stainless steel. It was a tricky application. If excessive forming pressure is applied, the assembly will be stiff or the plastic parts could crack. Too little, and the assembly will be loose. Every joint had to be perfect. And, because the assembly was a medical device, the company had to scrupulously document the as-sembly process.To accomplish this task, Taumel Assembly Systems (Patterson, NY) supplied an orbital forming machine with the ability to measure the height of the assembly and the forming pressure in real time. A linear scale measures the length of the rivet or post and the overall stack-up height of the parts. A load cell built into the parts fixture measures the actual pressure applied by the tip of the forming tool, rather than just the cyl-inder pressure. Height sensing and force monitoring ensure that manufacturing errors are detected early, reducing reject rates and production costs.
A PLC control with a touch-screen display allows engineers to program stroke time, forming time, forming pressure and stroke length. Process control data can be downloaded to a PC or a mainframe computer.
For advanced production, Taumel also supplies riveters integrated with CNC X-Y-Z positioning systems. This enables a single riveter to head multiple rivets or studs on one or more assemblies in the same work path. The rivets can be different heights and different materials with varying tensile strengths. Thus, the riveter could form two posts on the same assembly, even if one is tall, wide and steel, and the other is short, narrow and brass.
In the surgical instrument application, the forming tool advances onto the stainless steel rivets when the machine is activated. At this point, the tool is not moving. Rather, it’s acting as a touch probe to measure the height of the parts, verifying that the parts are present and that they are the right size. If the preprogrammed parameters for the parts are met, the orbital forming action will start, and the forming tool flares out the rivets. When the process is complete, the tool raises up off the assembly.
Careful control of the rivet height ensures that the assembly has enough play to swivel, but not so much that the parts are loose.
For more information, contact Taumel at 845-878-3100 or visit www.taumel.com.
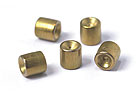
These ClinchRivets attach metal brackets to an automotive filter housing. The housing manufacturer had been spot welding the brackets, but switched to the ClinchRivets because they did not damage the anti-corrosive coating on the parts. Photo courtesy Tox-Pressotechnik
Process ‘Clinches' Bracket Assembly
Tox-Pressotechnik (Warrenville, IL) has long been known for its “rivetless riveting” process for clinching metal sheets together with a punch and die. A simple round punch presses the sheets to be joined into the die cavity. As the pressing force increases, the punch-side material spreads outwards within the die-side material. The finished joint is a round button without burrs or sharp edges. The process leaves a small de-pression on the punch side of the joint and a small bump on the die side. The surface of the metal sheets, including anti-corrosive coatings, remains intact; the protective layer flows with the material.Two years ago, Tox introduced a variation on this process called the ClinchRivet. The process works in much the same way as the company’s “rivetless” method, except that the punch pushes a small, cylindrical rivet into the joint. Each end of the rivet is convex. As the pressing force increases, the rivet deforms along with the sheet materials, changing shape from a cylinder to an hourglass.
The rivets are available in standard diameters of 3.5 millimeters and 5 millimeters. The thinner fastener is 2 millimeters long and joins stacks with a total thickness of 1.4 to 2 millimeters. The thicker fastener comes in lengths of 5, 6 and 7 millimeters for joining stacks 2 to 3.5 millimeters thick, 2.5 to 4 millimeters thick, and 3.5 to 5 millimeters thick, respectively.
The addition of the rivet increases both the shear strength and tensile strength of the joint. It also fills the depression that would otherwise be left on the punch side of the assembly, leaving a flat surface. The process is similar to self-piercing riveting, except that less force is needed to install the rivet, and the fastener does not cut the metal. Like the company’s standard clinching process, rivet-clinching does not damage anti-corrosive coatings on the sheets, and prepunched holes are not required.
“For most applications, our standard clinching method meets the assembly’s strength requirements without the additional fastener,” says Bruno Maczynski, marketing manager at Tox. “The ClinchRivet offers superior strength when used with thin materials or high-strength alloys.”
Recently, an automotive supplier implemented the process to join two brackets to a filter housing. The company had been using spot welding to attach the brackets, but switched to the ClinchRivet process because it did not damage the anti-corrosive coating on the parts. In addition, the clinching process did not generate sparks or fumes like spot welding.
Two presses are used to install five rivets in the assembly. A process monitoring system ensures that the rivets are installed at the correct depth and force.
For more information, contact Tox at 630-393-0300 or visit www.tox-us.com.
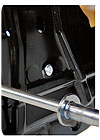
This steel blind rivet attaches the ground wire for an air bag to an automotive seat frame. A unique rib design allows the fastener to be installed in large holes without causing deformation or stress fractures. Photo courtesy Emhart Teknologies
Error-Proof Tool Sets Blind Rivets
Many cars are now equipped with air bags for side-impact protection. These air bags are often located in the front seats. Assembling and installing these air bags must be rigorously controlled-and not just because the devices are “mission-critical” components. A loose fastener could create an annoying rattle or worse, become a projectile if the air bag should deploy.This was the challenge faced recently by a manufacturer of automobile seats. Each seat assembly for a particular vehicle was equipped with an air bag. The ground wire for the air bag was fastened to the frame using a blind rivet that had to be visually inspected after setting. If a defect was found, the seat was taken off-line and reworked. This was costly and inefficient.
The company called on Emhart Teknologies (Shelton, CT) for help. Emhart applications engineers installed SmartSet quality assurance systems at each riveting station. The SmartSet system uses a microstrain sensor to measure the force at which a rivet setting tool-in this case, the Proset 2100-installs a fastener. The system monitors each sequential rivet set and compares the results with learned settings. Any variance is detected immediately and a “go/no-go” instruction is sent to the production line controller via I/O cable. Correctly set rivets signal the controller to release the seat to the next assembly station, while any variance stops the line so the assembly can be inspected and corrected immediately.
The SmartSet system fit well with the company’s assembly line, which assembles seats in various configurations in the exact sequence that they are needed by automotive OEMs. Each seat is identified with a unique bar code. As each seat enters a riveting station, the bar code is read and the SmartSet system automatically knows what rivet application to run.
With a stroke of 17 millimeters and a pulling force of 8.4 kilonewtons, the pneumatic Proset 2100 can set stainless steel rivets up to 4.8 millimeters in diameter. The tool’s front-end components can be serviced in minutes, without tools and without removing the tool from the assembly line. The tool can install at least 250,000 rivets before any major servicing is required. The body of the tool is made from a lightweight polymer. The trigger is wide, with rounded edges, for a comfortable grip.
The ground wire is attached with a POP brand SD53HR high-retention rivet. The rivet has a steel body, a steel mandrel and a domed head. It’s 4 millimeters wide and 10.6 millimeters long, with a head diameter of 8 millimeters and a grip range of 3.2 to 4.8 millimeters. A unique rib design provides greater side expansion of the rivet body, allowing the fastener to be installed in large holes in plastic and thin sheet metal without causing deformation or stress fractures.
Real-time process monitoring has reduced rework at the plant. Common riveting failures, such as head ejections, partial pull-throughs, missing rivets and incorrect rivets, have been eliminated.
For more information, contact Emhart at 203-944-1706 or visit www.emhart.com.