During the 1950s, there was a boom in new assembly plant construction in the United States. Today, many of those plants are still going strong. In fact, several of them were finalists for the 2007 Assembly Plant of the Year award.
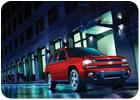
The 1950s was a unique era in the United States that was marked by economic prosperity, aerospace-inspired automobiles and a new form of music called rock ’n’ roll. A wave of optimism swept over the manufacturing landscape and there was a boom in new plant construction. ASSEMBLY magazine debuted in the midst of it all.
Several years before the first issue of ASSEMBLY rolled off the printing press, General Motors Corp. (Detroit) opened a plant in Moraine, OH, to assemble Frigidaire appliances. A few years later, IBM Corp. (Armonk, NY) built a large manufacturing plant in Rochester, MN, to build punch card-operated mainframe computers.
Today, those plants are still going strong, but the products they assemble have changed dramatically. Both facilities were finalists in the 2007 Assembly Plant of the Year competition sponsored by ASSEMBLY.
There was a strong field of candidates for the fourth annual award. That made it difficult for the team of judges, which included ASSEMBLY’s editorial staff, to narrow down the list to four finalists.
All of the assembly plants were worthy of consideration, but at the end of the evaluation process one stood out from the others: the Schneider Electric/Square D plant in Lexington, KY. The facility was selected as Assembly Plant of the Year because of the way it has used continuous improvement initiatives to stay competitive in today’s global economy, especially as some of its competitors have moved assembly to offshore locations.
However, the other finalists are also quite impressive, because they all specialize in flexible, high-mix assembly. Here’s a brief look at what makes each of these world-class plants stand out.
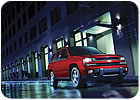
The Chevy TrailBlazer is one of five different midsize SUVs that are assembled at GM's Moraine, OH, plant.
GM Moraine
In recent years, midsize sport utility vehicles (SUVs) have been one of the most popular market segments in the auto industry. According to J.D. Power and Associates (Westlake Village, CA), demand for midsize SUVs grew more than 50 percent over the last 10 years.General Motors’ Moraine, OH, assembly plant builds several different vehicles in this category, including the Buick Rainier, Chevrolet TrailBlazer, GMC Envoy, Isuzu Ascender and Saab 9-7X. Last year, the facility assembled 229,242 SUVs.
The 4.4 million square foot plant uses a process called global error proofing (GEP) to monitor the entire assembly process. As a vehicle travels through production, it controls the sequential build sequence to ensure that operators adhere to various model options.
“Producing five unique models with more than 5,000 parts each, it is essential that we have multiple applications of error proofing to ensure that all requirements on each job are complete,” says Mike Glinski, plant manager. “The error-proofing systems we use include process tools that give feedback to the system that all required events have occurred, [in addition to] part pick, bar code scanning and vision systems.” Operators also use a world-class torque monitoring system that features DC electric fastening tools.
Material sequencing costs have been reduced by the delivery of parts and components directly to the line. The plant has used the logic in GEP to implement an electronic pull system that orders small lots of material for each workstation automatically. The system counts each vehicle that has been built and then electronically explodes the bill of material.
The Moraine plant has more than 2,000 employees who are heavily involved in continuous improvement efforts. By using lean methods, such as value-stream mapping, joint cross-functional teams have generated numerous cost-reduction ideas.
Operators are involved in approving all changes to their jobs that include new assembly strategies. They provide suggestions and feedback on what works, what doesn’t work or what should be considered.
“These efforts have helped eliminate production bottlenecks and reduce overtime, in addition to reducing scrap and indirect material purchases,” says Glinski. “Operators are empowered to implement new strategies with agreement from their shift counterpart. Team leaders assist in writing and changing documented, standardized work.”
Operators participate in continuous improvement workshops that help identify waste, experiment with new methods of doing work, and rebalance jobs to improve productivity. The adopted ideas from the workshops are implemented in less than one week.
Team leaders perform regular layered audits of their teams to identify opportunities for improvement and suggest new assembly strategies. They also participate in engineering trials and recommend improvements to ensure that proposed changes are efficient and executable at the line level.
The Moraine plant has a “Voice of the Customer Wall” that focuses on items that customers have designated as priorities. “Listening to our customers and focusing on their comments boosts our competitive advantage,” says Glinski. “Employees call customers who have recently purchased a new Moraine-built vehicle to thank them for their purchase and help answer any questions they may have about their new SUV.”
Operators also conduct regular equipment reviews to ensure readiness and alert maintenance to problems that require attention. They use the Five Why’s of troubleshooting on every breakdown to improve technology, thus preventing repetitive failures.
Cross-functional throughput improvement teams exist throughout the plant to leverage lessons learned and troubleshoot technologies. “Through the ongoing use of predictive technologies, we have learned to further predict and prevent failures,” explains Glinski.
The predictive technologies team uses vibration analysis, chain wear analysis, airborne ultrasound, thermal imaging, motor signature analysis and laser alignment to improve equipment uptime and life cycle.

The IBM Rochester plant assembles a wide variety of products, including System i servers, which are used for online business applications.
IBM Rochester
Although computer chips are not edible, the closest thing to an IT smorgasbord exists on the plains of southern Minnesota. IBM Rochester manufactures an extremely diverse product portfolio under one roof, while utilizing consistent management, engineering and procurement tools across all operations.Products assembled in Rochester include computer servers, supercomputers, point-of-sale systems, self-serve kiosks, medical devices, handheld scanners, rugged laptop computers for military applications, and an assortment of other high-tech wonders. The plant is one of IBM’s best-kept competitive secrets.
“[Our] diverse product portfolio runs the gamut of complexity ranging from highly configurable, build-to-order high-end servers, to relatively low-complexity self-service kiosks,” says Dan Thomas, plant manager. “Each product type has attributes which call for different production strategies.”
Common production practices, tools and operators allow the facility to leverage the skills required for assembling and testing diverse, complex product lines. The plant uses modeling tools to project workload. This allows for resource balancing before and during shifts, and it allows the management team to move resources to where the work is.
According to Thomas, each manufacturing team designs its own work processes. “This common sense approach significantly empowers team members to develop well thought-out process steps and reinforces the ownership in the process and product for the manufacturing technician,” he points out.
Over the last 50 years, IBM Rochester has continuously reinvented itself to sustain an extremely competitive and technically viable operation. Today, the plant has 1,000 employees. “By managing a diverse product portfolio with a simple philosophy and an approach to keep the decision making and process development close to the process itself, the site has effectively lowered its center of gravity for reactiveness,” says Thomas.
“[Our] key asset, an experienced workforce, has [made] a significant and effective impact on day-to-day, as well as long-term, operations,” adds Thomas. “The manufacturing team has leveraged what it has learned over time. This has allowed the plant to continuously improve and use best-in-class processes developed by manufacturing a wide variety of products.”
The plant continues to embrace change. “In so doing, it has fostered a bold attitude to take on any challenge, and then quietly deliver beyond expectations,” explains Thomas. “This ‘get it done quietly,’ low-key, modest and unassuming approach is the reason [we are] one of IBM’s best-kept secrets.”
IBM Rochester’s underlying philosophy is simplicity. Assembly technicians-the people who are closest to the product-are responsible for setting up and improving their own processes. This keeps simplicity and practicality at the forefront of all processes.
For the past 15 years, the plant has embraced globalization by shifting some work to other IBM manufacturing sites around the world based on cost optimization and market dynamics. While focusing efforts to make the extended IBM manufacturing network successful as a whole, IBM Rochester has been able to successfully anticipate market needs and position itself with the skills and product expertise called on by the market.
Quarter after quarter, the plant has delivered a very diverse product line servicing a similarly diverse customer set. A Customer Showcase initiative encourages team members to consider the manufacturing floor as a showroom.
“Many IBM customers want to see where and how their systems are assembled, configured, integrated and tested,” says Thomas. “This idea of showcasing the facility and people resonates very well when manufacturing technicians can meet customers and demonstrate with pride their skill in assembly and passion for quality.”

Vantage Manufacturing & Assembly isn't afraid to tackle any type or size of project.
Vantage Manufacturing & Assembly
According to an old adage, variety is the spice of life. It also forms the backbone of Vantage Manufacturing & Assembly LLC (Poughkeepsie, NY). The company is a contract manufacturer that assembles a wide variety of automotive, aerospace, medical and consumer products, in addition to military devices and heating, ventilating and air conditioning (HVAC) controls.For instance, Vantage is the sole assembler of the Heat Computer, a device that monitors heat and air conditioning systems in large buildings in many cities. The product helps reduce harmful emissions and saves fuel by keeping HVAC units from running constantly. Optimum Applied Systems Inc. (Dobbs Ferry, NY) turned to Vantage to mass-produce the energy management system.
“We will build anything our customers ask of us, from making a tiny nylon screw to assembling large industrial convection ovens,” says Nancy Drugan, human resource and quality assurance manager. “If it’s something we’ve never done before, we figure it out. If it involves tooling or machinery we don’t have, we get it. We have no fear of conquering the unknown.”
Earlier this year, Vantage made national headlines when it revealed that it was building a new environmentally friendly taxicab for use in New York City. The MetroKing, which is marketed by Alternative Fuels Technologies Corp. (Jamaica, NY), is the first custom-made taxi for U.S. cities since Checker Motors Corp. (Kalamazoo, MI) stopped assembling its classic vehicle in 1982.
The new fuel-efficient, handicap-accessible MetroKing is based on a Chevrolet Colorado pickup truck. It uses hybrid-electric components, such as large battery packs and an advanced starter-alternator. The vehicle is also available with a compressed natural gas fuel system.
Vantage Manufacturing only has 40 employees, but that small size works to its advantage. It allows the company to leverage employee expertise when tackling big jobs, such as the MetroKing project.
“This company is comprised of employees from many manufacturing plants that are no longer in existence,” explains Drugan. “Manufacturing was once the dominant employer in this region. Because of outsourcing, many have been forced to close their doors.
“[We are] committed to reversing that trend, to becoming the biggest and best manufacturing facility in this region,” Drugan points out. “To that end, we are employing the most highly skilled people, and obtaining the best equipment to ensure our products are built quickly and correctly.”
“The flexibility of personnel due to cross-training [ensures] no disruption to product flow,” notes Edward Winiarski, plant manager. “Corporate planning involving all employees allows for the input of positive ideas toward continual improvement, which are implemented on a regular basis.”
Inside the 34,000-square-foot facility, employees perform a wide variety of turnkey production operations, including printed circuit board assembly, wire harness assembly, sheet metal fabrication and electromechanical assembly.
“By incorporating state-of-the-art technology and software, we are able to offer our customers quick turnaround on their product,” says Jeff Burger, materials control manager. “Strict adherence to ISO standards ensures our customers get quality product and information every time.”
“[State-of-the-art] MRP software has been implemented to show real-time data, allowing our customer service reps to deliver rapid responses to our customers,” adds Burger. “RFID and bar code technology have been introduced to track product from procurement to shipment. By recycling all our raw material, we can guarantee no hazardous waste affects the employees or the environment around them.” A