Available in many shapes, sizes and materials, plastic snap-in fasteners secure panels, hoses and wire harnesses.
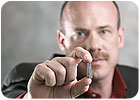
During the past few years, assemblers have invested considerable sums in high-tech fastening tools. Nutrunners and screwdrivers measure the torque and angle applied to threaded fasteners with great precision. Riveters monitor how much force was used to set a blind rivet, how many rivets were installed, and how many mandrels were collected.
That’s all well and good if you’re assembling, say, the brake system for a car. But, if you’re installing plastic trim in the car’s interior, you hardly need that level of technology. In fact, you may not need a metal screw or rivet at all. In some cases, assemblers can simply push in a few plastic fasteners by hand and be done with it. Assembly doesn’t get much easier than that.
“Christmas trees,” clips, snap rivets and other push-in plastic fasteners are a fast and inexpensive method for joining sheets or panels made from metal, plastic, composite, rubber, wood, foam or fiber. Available in myriad shapes, sizes, designs and materials, these fasteners resist vibration and abrasion. Because they’re plastic, they neither corrode nor conduct electricity, making them ideal for installation in painted sheet metal, circuit boards and electrical enclosures. Plastic fasteners also weigh less than metal ones.
The main advantages of plastic fasteners are “speed and ease of assembly,” says Bruce Sanders, domestic sales manager for Micro Plastics Inc. (Flippin, AR). “You simply push them in. With screws, you may need threaded inserts or nuts. With plastic fasteners, you just need a hole.”
Plastic fasteners are used in the automotive, appliance, aerospace, electronic and furniture industries. In electronics, plastic fasteners mount heat sinks to circuit boards and finger guards to cooling fans. Other snap-in fasteners have clips that route wires and cords around the assembly.
Plastic fasteners can be found in countless locations in vehicles. In the interior, they anchor upholstery, door panels and consoles. In the engine compartment, they attach the fire blanket under the hood. Snap-in clips route harnesses, cables, hoses and fluid lines throughout a vehicle. Christmas tree fasteners attach the radiator shroud to the condenser in the Chevrolet Corvette, and they help secure plastic flaring on the fenders of the Toyota Land Cruiser.
“Our fasteners are used in everything from bird feeders to the space shuttle,” says Sanders.
Plastic push-in fasteners are typically installed by hand or with a rubber mallet. For high-volume applications, pneumatic and spring-loaded tools are available. For example, the Grinch from Fremont Machine and Tool (Fremont, NE) is a handheld air gun specifically for installing Christmas tree fasteners. The fasteners are emptied into a hopper, which files them through a tube into the gun. Pulling a trigger shoots a fastener into the hole. Weighing only a few pounds, the tool comes in different models according to fastener size and can be custom-made to suit any size fastener.
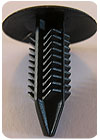
Oh Tannenbaum...
The Christmas tree fastener, or fin clip, gets its name from flexible fins on its shaft. When the fastener is stood on its head, its pointed tip and sloping fins give it a shape reminiscent of a pine tree. As the fastener is pushed into place, the fins deflect and then spring back after they pass through the hole. Because the fins tilt toward the head, the fastener is easier to push in than pull out.The fasteners are typically molded from various grades of nylon 6 or nylon 6-6, depending on the requirements for flexibility, vibration-dampening, impact resistance and heat resistance. The fasteners can also be made from polyethylene, polypropylene, thermoplastic elastomer (TPE), thermoplastic polyamide or acetal copolymer. They can be molded in many colors, including black, white, beige and green.
Christmas tree fasteners do not have to extend beyond the panel and will hold securely in blind holes if the panel material is softer than the fastener material. They can have round, binder, crowned or flat heads ranging from 0.177 to 1.26 inches in diameter. The point of the fastener can be conical, blunt, round or triangular. The fasteners are available in lengths ranging from 0.22 to 2.03 inches.
The force required to push out a Christmas tree fastener varies depending on the temperature, the diameter of the hole, the thickness of the panel, the design of the fins, and the materials that the panels and fastener are made from. For example, it requires approximately 31 pounds of force to push out a fastener inserted into a 0.197-inch diameter hole in high-density polyethylene (HDPE) panels ranging from 0.08 to 0.402 inch thick. At the same time, it requires approximately 175 pounds of force to push out a larger fastener from a 0.281-inch diameter hole in particle boards ranging from 0.05 to 0.9 inch thick.
“You don’t want a hole that’s too small or too large,” says Sanders. “A 1-inch hole is too extreme for a part like this. A hole size anywhere from 1/8 to 3/4 inch is good. If you get much smaller or larger than that, you’re going to run into difficulties. If it’s too small, it won’t function well. If it’s too large, you defeat the purpose of using a part like this. The most common hole sizes are 1/4 to 3/8 inch in diameter.”
Christmas tree fasteners can be reused, but only for a limited number of times. “You can pull them out and reuse them two or three times,” says Sanders. “After that, the fins get boogered up, and they don’t retain as well.”
There are many variations on the basic Christmas tree design. Double-ended Christmas tree fasteners enable two panels to be connected from the center. The fastener head will not be visible, but the body of the fastener can separate the two panels by various distances. Double-headed Christmas tree fasteners also secure multiple panels. The upper head of the fastener snaps or twists into one panel, while the shank secures one or more additional panels.
A variation on the Christmas tree fastener is the knurled-head spin clip from Micro Plastics. This fastener combines the advantages of a push-in fastener and a screw. For fast assembly, the part can be pushed into a 1/4-20 threaded hole, then screwed in for a tighter fit, or screwed out for disassembly. The fastener also functions as a standard Christmas tree fastener for use in an unthreaded hole approximately 0.203 inch in diameter. It’s available in lengths from 0.375 to 1 inch.
One more variation on the theme is the Spinweld Christmas tree fastener from ITW Fastex (Des Plaines, IL). This two-piece fastener-a Christmas tree and a receptacle-was designed to accommodate misalignment problems when joining plastic panels for products such as office chairs. The head of the Christmas tree is spun against the frame with pressure, causing the two plastic surfaces to melt and molecularly bond. The receptacle is snapped or spin-welded onto the mating panel or frame. The two parts can then be snapped together without the need for threaded fasteners.
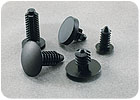
The force required to push out a Christmas tree fastener varies depending on the temperature, the diameter of the hole, the thickness of the panel, the design of the fins, and the materials that the panels and fastener are made from. Photo courtesy Micro Plastics Inc.
Clips and Rivets
Christmas trees aren’t the only type of plastic push-in fastener. Indeed, there are almost as many plastic fasteners as there are Christmas tree ornaments.Arrow clips are reusable nylon fasteners. This fastener has an ovate body that compresses as it’s forced through a hole and springs back to its original shape to lock the parts securely. The clips can be pulled out and reused multiple times. The head diameter ranges from 0.1 to 0.866 inch, while the clip diameter ranges from 0.068 to 0.375 inch. They come in lengths from 0.125 to 1.135 inches. They can be inserted in holes ranging from 0.062 to 0.34 inch in diameter, and they can join panel thicknesses of 0.01 to 0.35 inch.
As with Christmas tree fasteners, there are many variations on this theme. One example is the Stalok fastener from ITW Fastex. Instead of an ovate rivet body, flat shoulders, or prongs, extend from the body of this rivet. This rivet is tamperproof from the front. It can only be removed by compressing the prongs from the back side of the assembly.
Ratchet rivets are two-piece fasteners. To assemble a set of panels, one half of the fastener is inserted into the hole from one side of the assembly, while the other half is inserted from the opposite side. The two halves are then pressed together. Each fastener has serrated teeth that lock together, permanently joining the assembly and adjusting to a variety of widths. Molded from nylon 6-6, they are available in white or black. They can also be dyed or painted. The smallest model can sandwich a thickness of 0.235 to 0.297 inch. The largest can accommodate a thickness of 0.78 to 1.38 inches.
A similar concept is the two-piece snap rivet. Instead of interlocking ratchets, the two halves lock together with an annular snap-fit. Like ratchet rivets, snap rivets are molded from nylon 6-6. The smallest model has a grip capacity of 0.17 to 0.19 inch. The largest has a grip capacity of 0.32 to 0.34 inch.
Another option is the drive-pin rivet. This two-piece plastic fastener consists of a rivet body and a drive pin. The body is hollow along most of it’s length. The bottom of the body is solid, and its sides are slotted. After the rivet is inserted into a hole, a hammer is used to drive in the pin flush with the rivet head. This breaks the bottom and expands the sides outward, producing a tight grip on the back side of the panel.