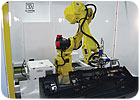
The Chevrolet Volt is one of the most anticipated vehicles in ages. When the car is produced later this year, robotic ultrasonic welding will play a key role behind the scenes. Interior trim components will be assembled with the technology, which is becoming increasingly popular in the auto industry.
“Vehicle volume is much smaller today, with many more niche products,” says Kirk Brunssen, vice president of sales and engineering at T.A. Systems Inc. The company recently integrated 12 FANUC robots for use in the Chevy Volt program. “As a result, automotive suppliers need more flexible production equipment.
“Robotic sonic welding is not the most common method of welding, but it continues to grow in popularity with each passing year,” claims Brunssen. “The most typical applications are plastic welding on projects that have a slightly longer cycle time than more conventional methods. The most common application is the attachment of noise, vibration and harshness (NVH) or sound-reduction materials to interior trim components, along with actual spot and stake welding of materials.”
“There’s no doubt that this is a growing technique,” adds Jeff Frantz, director of applications and ultrasonic tooling at Branson Ultrasonics Corp. “Even though [robotic ultrasonic welding] is still a small percentage of the overall market, it has more than tripled in the last decade. We have seen everything from the welding of automotive bumper brackets to the cutting of instrument panels.”
Other automotive parts assembled with robotic ultrasonic welding include door panels, headlamps, hard trim, quarter trim, exterior cowls, fascias, defroster ducts and engine covers. The technology is used on such vehicles as the Cadillac Escalade, Dodge Caliber, Lincoln MKT, Toyota Corolla and Peterbilt trucks. While most applications are confined to the auto industry, appliance and electronics manufacturers have also integrated robots with ultrasonic welding.
Robotic ultrasonic welding is also used to join large metal car parts. For instance, Ford Motor Co. has been at the forefront of using the technology to assemble aluminum body structures, trunk lids and door panels.
“Challenges include the weight and size of the ultrasonic system and the need for a robot arm to accept these fairly large and heavy systems,” notes Janet Devine, president of Sonobond Ultrasonics, who has worked with Ford engineers on the project.
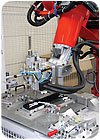
Numerous Benefits
Flexibility is the No. 1 reason why manufacturers want to equip six-axis robots with ultrasonic welding heads. Many different parts can pass through a robotic workcell by simply changing tooling and reprogramming the robot. For example, a manufacturer could assemble exterior cladding on first shift and interior door trim on second shift.“The largest advantage is the flexibility in product design it allows for, the greater utilization of capital equipment by OEMs, and the reduction in the overall tooling cost on current and future products,” Brunssen points out. For instance, adjustments to weld parameters and weld quality can be made much faster and without the use of tools.
“Adjustments are now made on a touch panel instead of with a wrench in a fraction of the time it took before,” explains Brunssen. In addition, the process feedback provided by the system gives more information during setup, which allows for tighter process tolerances and results in more consistent part quality.
“In a normal bench-type environment, the ultrasonic actuator needs to be mounted to a stand or base assembly,” adds Frantz. “[With robotics] the stand and base are not required, because the actuator mounts directly to the robot. In some instances, the actuator can be eliminated as the robot is used to deliver the ultrasonic tooling to the part. The palm buttons that initiate the cycle can also be eliminated as the automated cell initiates the cycle.”
“Flexibility is certainly the largest advantage, but precision plays into the equation as well,” notes Vasko Naumovski, product manager at Herrmann Ultrasonics Inc. “Lower production volumes sometimes necessitate multiple machines, so a single robot may take up less floor space and cost less than multiple individual welders.” Of course, robotic cells for some applications can be even larger than dedicated machines.
With a robot, one ultrasonic head is often used instead of multiple heads. “A robot provides greater flexibility to retool the device when compared to standard multiheaded ultrasonic machines,” says Bill Aurand, national sales manager at Rinco Ultrasonics USA Inc.
Typically, six-axis articulated robots work the best for ultrasonic welding. “The geometry of the part always determines things such as reach issues,” explains Joe Campbell, vice president of sales and marketing at ABB Robotics North America. “It depends on the application and the size of the part.”
According to Brian Gourley, technical services manager at Sonics & Materials Inc., six-axis robots are ideal because they make it easier to reach contoured surfaces. “No matter what type of robot is used, it must be able to move into position quickly and align the ultrasonic horn,” he points out.
“Most SCARA or parallel-type robots can only handle smaller loads and their work envelopes make them well-suited for picking and moving parts from a conveyor and then into an ultrasonic welder pedestal,” adds Michael Sharpe, material joining segment manager at FANUC Robotics America Inc.
“But, larger robots, which are typically articulated in design, offer higher payloads and six degrees of freedom so they can articulate a part for continuous seam or actually handle the welder on the end of the robot’s arm,” Sharpe points out. “Large robots have the ability to more readily integrate the controls and servo actuation through the robot’s motion.”
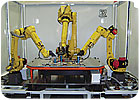
Pros and Cons
Several challenges confront engineers when using robots for ultrasonic welding applications. One concern is cycle time. If an application requires many weld points, the cycle time can become long.
“On traditional sonic welding equipment with dedicated welders for each point, the cycle time can be very fast,” explains Brunssen. “However, on parts that have many welds required, the cycle time has to be considered to make sure it meets the desired production requirements. We can get around this by using multiple robots or multiple weld heads or part indexing, but each application and customer requirement is unique.”
Another significant factor can be the potential added cost of robotic equipment. “The upfront cost can sometimes be greater than dedicated machines,” Brunssen points out. “But, robotic sonic welding is not necessarily more expensive. There are a lot of factors that determine the cost compared to traditional types of assembly equipment. [It’s important] to develop a system that can meet budget requirements without sacrificing future flexibility.”
In recent years, the price of robots has decreased, while the variety of products and features has increased. “The benefit comes from the end user’s ability to reuse the robot for a new application,” says Gourley. The advantage of a robotic cell is that it can be easily retooled for future applications. Manufacturers can run several programs in a cell vs. several dedicated cells.
“If robotic ultrasonic welding were used for a dedicated product, then it could be more expensive,” adds Naumovski. “The reason to justify it would be cycle time. If the assembly process were tied to a molding machine operation of say 45 seconds, and there were six welds to be accomplished, if the robot could accomplish the task in that time frame, then it’s justifiable. If the welds take longer to accomplish, then a different process should be considered.”
Payload capacity is another important consideration. A 20-kilohertz welding stack can be quite heavy. As the weight of end-of-arm tooling goes up, the cost of a robot typically increases.
“End-of-arm quick-change tooling can be used to solve this problem, but this adds cost and complexity to the machine,” warns Michael Johnston, vice president of sales and marketing at Dukane Corp. “Ideally, the end-of-arm tool should include a small-stroke air cylinder. This provides for significant improvement of weld performance and machine setup.
“In an effort to reduce end-of-arm tooling weight, a special nodal-mount, high-gain horn [allows engineers to eliminate] a booster,” adds Johnston. “This can reduce end-of-arm tool weight by as much as 30 percent.”
Other factors that engineers should consider are programming, controls and fixturing. They must ensure correct alignment of the weld points, perpendicularity of the weld horn to the part, and consistent application of force by the robot. A
Learn more about robotic ultrasonic welding by clicking these ASSEMBLY articles:
Glossary of Ultrasonic Welding Terms
The Economics of Ultrasonics
The Pros and Cons of Robotic Ultrasonic Welding