Compared with the automotive industry, medical device manufacturers are in the early stages of applying lean manufacturing principles. Manufacturers of advanced imaging equipment and surgical devices tend to be further ahead of companies that produce high-volume, low-cost devices.
“Generally speaking, the medical device industry has just begun its lean journey,” claims Don Penkala, president of Granite Bay Global, a lean manufacturing consulting firm. “Of course, there are exceptions. [Some] medical device plants [rank among] the leanest I've seen.”
Automotive companies have used some form of lean for several decades with varying degrees of success. Consumer products manufacturers embarked on their lean journey in the mid-1990s.
“The adoption of lean initiatives in the medical device industry accelerated with the economic downturn, as manufacturers had to find new methods for reducing costs and sustaining quality in increasingly regulatory and price-sensitive markets,” says Penkala.
“The reluctance of some [medical device players] to adopt lean is a result of the intense regulatory environment in which they operate,” Penkala points out. “It is not as easy to experiment with cell creation, team modifications, test runs [and other initiatives] with the level of documentation and reporting requirements inherent in medical device manufacturing.”
Medical device manufacturers have used many of the same excuses, delaying the widescale adoption of lean manufacturing. “Besides the typical justification that ‘lean is for automotive manufacturers’ or ‘lean only works for Toyota,’ the most common excuse against using lean concepts is [the misnomer that it can’t] work in a highly regulated environment,” says Sammy Obara, president of Honsha Associates, an alumni association of former Toyota Motor Corp. engineers and managers.
“One company I ended up teaching lean to for several years gave me an early push back claiming that continuous improvement would make them ‘too bureaucratic,’” recalls Obara, who spent three years studying lean manufacturing principles in Toyota City, Japan, and another 10 years applying it at Toyota plants in North and South America. “They explained that for every tiny change in their process they would have to create lots of documents to obtain FDA approval and that could take a long time.”
“Aside from the typical challenges with lean implementation, such as gaining commitment and understanding and applying the principles to a specific environment, the medical device industry faces rapid technological change,” adds Penkala. “[Manufacturers typically] need to incorporate automation where precision in required. [There’s] a reluctance to adopt change because of regulations; component and product traceability; and increased reporting and documentation requirements.”
Medical Device Manufacturers Slowly Go Lean
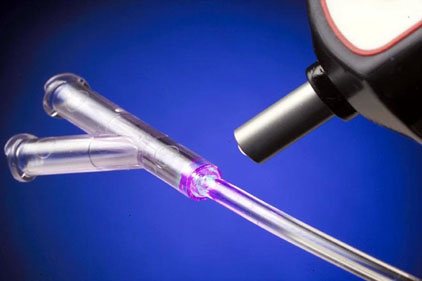