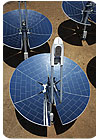
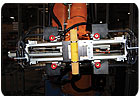
Based in Kennewick, WA, Infinia makes a unique solar energy system called the Power Dish. The system consists of a 3.2-kilowatt, free-piston Stirling engine; a parabolic mirror approximately 5 meters in diameter; and a dual-axis motion control system to keep the mirror pointed at the sun. The mirror focuses the sun’s rays onto one end of the cylindrical engine, creating a temperature differential-heat from concentrated sunlight at one end and cool ambient air at the other end.
The temperature differential causes helium inside the engine to expand and contract. That, in turn, makes a piston move back and forth inside the cylinder, and the piston drives an alternator to generate clean, grid-ready AC power. One PowerDish produces enough electricity to power a typical home.
The engine is a hermetically sealed system that does not require lubrication and has no touching parts. Once the engine is sealed, it can run for 25 years without any maintenance.
To produce the PowerDish economically, Infinia needed to automate assembly of the parabolic mirror. The company turned to Xigent Automation Systems Inc. for help. Based in Lewis Center, OH, Xigent has designed automated assembly systems for auto parts, medical devices, ink cartridges, disposable dairy valves, and military applications.
Infinia’s parabolic mirror consists of pie-shaped, molded panels approximately 2 meters wide and 2 meters long. Each panel is one-sixth of the full dish.
Attached to each panel are 23 mirrored glass tiles in various rectangular and trapezoidal shapes. The tiles are less than 2 millimeters thick and backed with a pressure-sensitive adhesive. The tiles are flexible enough to bend in two axes to conform to the parabolic shape of the panels.
The workhorses of Xigent’s system are two, vision-guided KR60 six-axis robots from KUKA Robotics Corp. Running in parallel, the robots pick up the glass tiles and affix them to the substrate panels. Assembly takes place on a large, five-position rotary indexing dial with custom fixtures to clamp and register the panels to mechanical datums.
Each tile shape is presented to a robot in stacks carried on two rotary indexers. Each indexer is associated with one of the two robots.
The most unique element of the system was the robot end-effector, says Jeff Stover, sales manager for Xigent. The tooling had to acquire each tile; remove the cover film from the adhesive; register the tile with the vision system; bend and place the tile onto the panel; and then burnish the tile to avoid trapping any air beneath it.
Four vacuum cups, each on a separate motor-driven positioner, are used to acquire, bend and place the mirrors. Each vacuum cup is driven to the most distal position possible for a particular part number to provide the maximum mechanical advantage for bending the glass. The glass is drawn up around a barrel-shaped roller using special low-friction air cylinders, since the forces are very low.
Once the robot acquires a tile, it moves the tile over a peeling knife to lift an edge of the cover film. A fixed gripper then grabs the lifted edge and the robot moves the tile away from the peeler to remove the film.
Next, the tile is held in front of a camera, which registers the corner angles and confirms the expected geometry of the tile. Xigent application software uses the vision data to enable the robot to place the part with an accuracy of ±0.5 millimeter. After the tile is placed, the vacuum cups release the tile, and the robot applies approximately 200 pounds of force on the roller as it moves back and forth over the tile.
For more information on automated assembly systems, call Xigent at 740-548-3700 or visithttp://xasinc.com. For more information on solar energy systems, call Infinia at 509-735-4700 or visitwww.infinia.com.
Editor’s note: Whether you’re a systems integrator or the in-house automation team of an OEM, if you’ve designed a system that you’re particularly proud of, tell us about it. Send an e-mail to John Sprovieri, editor of ASSEMBLY, at sprovierij@bnpmedia.com, or call 847-405-4068.