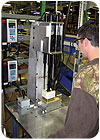
At its assembly plant in Athens, PA, Ingersoll Rand Co. (Annandale, NJ) produces more than a dozen different product families, including pneumatic impact wrenches, ratchets, grinders, precision fastening tools, nitrogen generators and oil caddies. The plant is a build-to-order facility with 22 assembly lines that assemble these different product lines in some 3,000 different configurations.
Recently the company embarked on a lean manufacturing initiative with the goal of increasing plant productivity by 5 percent, in the process performing a number of quality improvement initiatives to all of its 22 assembly lines. As part of this analysis, quality managers discovered a significant delay where operators were fastening hammercases on the company’s pneumatic impact-tool line.
Specifically, the hammercase installation station required workers to operate an impact wrench at the same time they were aligning each hammercase. To further complicate the process, the screws had to be installed in a particular sequence to avoid damaging the assembly.
“It’s the way the hammer case is fastened to the tool,” says Ingersoll Rand associate electrical engineer John Pazzaglia. “It’s critical because [the case] has to be evenly aligned on the housing to hold the motor together. If it’s screwed on in a tilted manner or off-center, it tends to lock up the rotor, and can even break the hammercase.”
To make matters worse, the work was physically demanding because of the torques involved and the fact that operators had to reach a fair distance to install all of the fasteners. At one point, Ingersoll Rand installed a tool balancer to help out. But, the operation was still hard on the company’s operators.
“The balancer was helpful as far as vertical motion, but...operators were always working with their arms outstretched and trying to move the tool left to right, which was still an ergonomic issue for us.” Pazzaglia says. He adds that the balancers proved to be clumsy to work with as operators struggled to align the tool. It was also difficult to verify hammercase torque values, which meant the company had to rely on end-of-line testing, where mistakes cost time and production efficiency.
To correct the ergonomic issues and speed up production, the company created a semi-automated fastening station employing an IC1D series controller and a battery of QM5 series DC electric fastening tools.
The new system eliminates repetitive strain injuries by enabling operators to simply place each assembly in a fixture, which is then lifted up into the fastening spindles, which tighten all four screws simultaneously, ensuring even torque across the hammercase.
The IC1D controller displays a green icon once the system has reached the correct torque values. It also stores all measurement data for later analysis, if necessary.
Ultimately, the new system has reduced the time required to install each hammercase by about 18 percent. The new table also frees up operators to take on additional functions and enables the Athens plant to produce an extra impact wrench every 2 hours.
For more information on fastening tools and customized fastening systems, call 800-376-TOOL or visitwww.irtools.com.