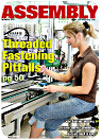
Screwdriving is one of the most popular, and most commonly abused, joining techniques. Engineers must understand common threaded joint design shortcomings and how to avoid them.
No matter the type of fastening application, production improvements are always high on a manufacturer's priority list. If you were asked to reduce labor hours in your product with only minor nonfunctional design changes, you would probably start by examining those activities that constitute the highest proportion of that labor.
With most products, the largest single contributor to labor content is joining and fastening, particularly the use of threaded fasteners. In most assembly operations, this consumes roughly half of all direct labor. According to the 2005 ASSEMBLY magazine capital equipment spending survey, fastening is the most commonly used production process.
Indeed, 57 percent of respondents perform screwdriving at their facilities. That's not surprising, especially considering that fasteners often account for 40 percent to 50 percent of the total part count on a bill of material.
Driving Under the Influence
One of the more lively topics of discussion among engineers on any plant floor is which drive style to use. Many options are available, including hex, Phillips, slotted and Torx screws. Each has unique pros and cons that typically depend on the specific application.
In an attempt to shed light on this debate, Archetype Joint recently conducted an independent comparison test of the drive styles commonly available in machine screws. These small fasteners were selected because they have the widest variety of drive styles available, and because they are by far the most plentiful. A leading tool manufacturer states that more than 80 percent of screws used in industrial production are smaller than or equal to M6 in diameter.
The comparison test was performed on #10-32 x 1/2 screws with eight different drive-head styles driven vertically with an in-line pneumatic clutch screwdriver supported by a spring balancer. Two runs of 13 screws each were installed by two different operators, with fresh screws used for each run.
In the first test, the screws were hand-started a couple of turns before driving. The test was repeated on four drive-head styles with the screws bit-started using a magnetic bit.
The comparison tests revealed some interesting results. For instance:
- The low installation time for the hand-started socket head cap screws was achieved by very fast hand-start times. This was a function of the cylindrical head, which was much easier to control than the other head styles.
- Start times for the hand-start portion of Test 1 averaged just less than 60 percent of the total time, with the driving portion making up the remaining 40 percent.
- Torx or equivalent six-lobe internal drives make it easier to engage the bit than the internal hex of the hex sockets, due to their slightly larger entry radius and a greater capacity for off-axis driving.
- The 60-degree symmetry of the six-lobe and hex drives makes these fasteners noticeably faster to engage than the 90-degree symmetry of the Phillips or other cross drives.
Another aspect of drive styles that affects productivity is the ability to drive the fastener when full access to the drive feature is not available, causing the bit to engage the drive off-axis. To test this capability, we hand-started the same eight types of fasteners used in Test 1 into a nylon prevailing torque nut with the same in-line air driver.
The tool was fixtured in a manner that allowed it to be angled to the screw by a controlled amount. We then experimented with drive angles until we determined the greatest angle each drive-head style could handle before the bit cammed out of or spun on the fastener.
The variation between the two variants of internal hex and Torx screws is due to the shallower depth of the drive feature in the button head compared to the pan or socket head, permitting a greater entry angle. The 17-degree angle of the hex cap screw can't be maintained through the entire drive, because the socket contacts the fastened component's face.
Fastening Tool Comparison
Another area of spirited debate among manufacturing engineers is which type of nutrunner technology is the most productive: clutch, DC electric or pulse. One factor that has raised the volume on this discussion are the new variants of electric tools coming to market. Some of these new tools are nearly as accurate and flexible as traditional transducerized DC electric tools, but are less expensive. Others offer the freedom of cordless operation.
So far, DC electric tools have a significant share of the midsize torque-controlled nutrunner market, which encompasses M6 to M12 fasteners. We compared the three most common tools for this market-the pneumatic clutch tool, the hydraulic-pneumatic pulse tool and the transducerized DC electric tool-for relative productivity and repeatability. All three tools had torque capacities of around 26 ft-lb (35 newton-meters). The clutch and DC electric tools were both right angle models, while the pulse tool had a pistol grip.
The productivity test was similar to the one previously described for machine screws, except the fastener was held constant and the tool varied. The fastener was a 5/16-18 hex flange head screw with 0.75 inch of free rundown before contacting the clamp member. The joint was hard, with the fastener rotating about 30 to 40 degrees after reaching snugness.
Four tests were conducted: hand-started with a horizontal and vertical insertion, and socket-started in the same horizontal and vertical setup. For each test, three sets of six rundowns each were performed. The rundown strategy used for each tool was the same "standard" strategy used for the repeatability test.
The test results revealed that the pulse tool permits quicker rundowns, which is one of the key selling points of the technology. However, the main source of that advantage is not the very high free speed-about four times that of the DC electric tool and seven times the clutch-but the ergonomic advantages of a single-handed operation with the pistol-grip tool over the two-handed manipulation required with the right-angle tools.
The reason these high spindle speeds don't generally result in significant cycle time improvements for many joints is that rundown is a small portion of the total cycle. Also, most of that advantage is lost in longer "pulsing out" at torque set in comparison to clutch activation or motor shut off-about 1 second vs. 0.1 second.
A 26 ft-lb pistol-grip pulse tool does not create unacceptable levels of torque reaction, because the tightening process is broken into many small pulses by the pulsing unit. As a result, there is no large reaction moment transferred to the operator.
When the other two continuous tools go from applying full target torque to being instantly shut off, that sudden change in energy is absorbed by the operator if the tool is handheld. Soft starts and stops can be programmed into full-featured DC electric tools. However, this increases cycle time.
The hydraulic pulsing unit that provides these advantages also carries some disadvantages. For instance, because soft joints require greater fastener rotation to achieve a given target torque, the number of pulses required to reach that torque will increase proportionally.
This adds incrementally more time to the pulse tool cycle, compared with the clutch tool and the DC electric tool programmed with a standard strategy. For example, in our repeatability tests, the pulse tool took 3 seconds longer to fasten the soft joint than the hard joint. In contrast, the DC electric tool took only 0.5 second longer, while the clutch tool took only 0.1 second more. In addition to slowing the tool, increased pulsing causes more wear and the need for greater maintenance.
For this reason, the best applications of pulse tools fall in a narrower range of joints than the other two technologies. Regarding the relative productivity of the DC electric and clutch tools, if the DC electric tool is programmed to a single-stage rundown at the same speed as the clutch tool, the drive times will be nearly identical. Since the size and weight of the tools are also very similar, it may appear that the productivity will also be the same. This discounts the ability of the manufacturer to differentiate its equipment through detailed design changes.
Clutch Tools vs. DC Electric
On average, the DC electric tool was about 5 percent more productive than the clutch tool. This was possible even though the rundown times averaged about a half second slower, because the start trigger was easier to manipulate than the much larger start lever of the typical air tool. These levers tend to be more awkward than a button and require more effort. The features of each tool should be carefully compared when making purchase decisions, as they can often have greater influence on productivity than basic technology.
The repeatability test that was run was similar, but not identical to ISO 5393, the standard tool performance test. The primary difference is that our test measured the repeatability of bolt tension rather than torque. This is both because tension is a more important indicator of the joint's quality, and because torque measurement of the discontinuous pulse tool is difficult to compare directly to traditional continuous tools.
A 5/16-18 hex cap screw was tightened in a load cell specifically designed for torque-tension fastener testing with a hex nut. The nutrunner was supported in a flex arm to minimize operator variation while still permitting controlled motion. A hardened washer was placed under both the bolt head and the nut. Both hard and soft joints were tested, with a nylon disk providing the characteristics of the soft joint.
The first test used the most likely tightening strategy for each tool, meaning a two-stage rundown for the DC electric tool. As these strategies can affect repeatability, alternative strategies were also tested to the extent of each tool's adjustability. For the DC electric tool, a "slow" strategy was run where the shift-down torque was lowered from 40 percent to 20 percent of target, while the second stage speed was reduced from 20 percent of max to 10 percent.
A "1 Stage" alternative was also run where the speed was set at 50 percent of max all the way to target. Pulse tool speed can be adjusted through flow control. A "slow" alternative strategy of 70 percent max was also tested.
One factor should be kept in mind when considering a tightening strategy with a programmable device like the DC electric tool used in this study. Two-stage tightening is a common strategy, because it can save time. But, in most joints, there will be an increase in torque or tension scatter when the speed a threaded fastener is rotating is suddenly slowed significantly and restarted. The reason is that the joint's friction factor, which has a large influence on the torque-tension relationship, is sensitive to the speed the fastener is rotated.
How much the tool slows during a down-shift is a function of each manufacturer's design, but is perhaps even more dependent on how close the down-shift torque is to the tool's capacity. When these two values are close, the tool can momentarily come close to stalling, increasing the potential for tension scatter.
At least in this one test, a single-stage strategy saved three-fourths of a second per drive while reducing repeatability by 15 percent. While the pulse tool showed somewhat improved repeatability on the soft joint, it came with the 3-second time penalty mentioned earlier.
The wide range of fastener applications makes it dangerous to draw wide-ranging conclusions from this, or any other, single test. Therefore, the relative accuracy of these three screwdriving technologies cannot be universally inferred from this test. In fact, one shouldn't choose between these technologies based primarily on accuracy or repeatability.
For applications where all three technologies are equally applicable, their ability to achieve a given torque or tension target will likely be very similar. However, this doesn't imply that each technology is interchangeable for any application. Each has different characteristics and different economics, so there is a best fit for each.
The greatest potential benefits that arise from a well-planned threaded fastening process are improved quality and throughput. This leverage can be increased to a much greater degree with detailed joint evaluation during product development.
Tooling Tips
Assemblers can choose between three basic types of fastening tools for screwdriving applications. Each has pros and cons that must be carefully evaluated.
- Clutch tools-good for dedicated applications without the need for multiple stage rundowns, particularly where the assembly layout or product may be altered after a period of fixed production.
- DC electric tools-good for assembly lines or workcells that require fully integrated error-proofing and statistics reporting requirements. This is particularly true if joint and fastener characteristics are unusual or vary from station to station. These tools are also good for production environments where a given tool may be used on multiple applications.
- Pulse tools-good for dedicated applications where the tool has been proven to be effective, such as hard joints in high-volume production environments where reduction of repetitive motion injury and labor content are key factors.