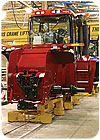
At its manufacturing facility in Fargo, ND, Case New Holland (Amsterdam, Netherlands) performs final assembly of its heavy-duty, articulated agricultural tractors. Weighing 60,000 pounds, the machines have long presented a material handling challenge as well as a challenge for safe, efficient assembly.
To streamline the process, Case New Holland recently implemented a series of four interconnected LO-TOW towline conveyors systems from SI Production and Assembly Systems (Easton, PA). The result has been a dramatic reduction in the number of man-hours required to assemble each tractor. In fact, the company’s return on investment for the system has been such that the conveyors were able to pay for themselves in less than a year.
In terms of actual operation, the different conveyor sections serve not only to allow easy access to parts throughout the assembly process, they also help Case New Holland perform joining operations of major subsections.
Each LO-TOW conveyor consists of a powered chain running through a recessed floor track that pulls a “cart,” which supports the assembly being processed. Each cart functions as a kind of a mobile workstation and provides access to all sides of an assembly, including the bottom. Carriers can be equipped with raise and lower features to accommodate a production line’s ergonomic requirements.
At the beginning of the assembly process, operators position a pair of towline carts back-to-back on a mainline indexing conveyor. The first cart carries the front axle of the tractor unit, while the second cart supports the rear axle. The conveyor then indexes through a number of workstations at a rate of 20 fpm as workers install transmissions and other components on the front and rear axle assemblies.
With this series of procedures complete, the conveyor turns 180 degrees, and the cart carrying the rear axle assembly diverts to a separate “side finger” indexing conveyor. Meanwhile, the cart carrying the front half of the tractor remains on the main conveyor where the front-half assembly is equipped with a cab and other components.
Once the additional components have been added, the rear-half cart returns to the main conveyor where it is joined to the front-half cart again. Operators at Case New Holland do this by simply connecting each in-process tractor’s drive shaft and other connecter parts, like the main pivot assembly.
With the two halves together, a short auxiliary conveyor positions the tractor assembly at the start of the system’s fourth and final conveyor section, which carries it through the line’s remaining assembly stations.
This final conveyor section advances the carts at speeds of 0.25 to 0.75 fpm. The conveyor’s total gross load capacity totals 448,000 pounds. Because the two halves of the tractor are now permanently attached, only one cart is needed to tow the assembly through this section.
When the tractors are complete, operators remove the carts and return them to a staging area where they are re-engaged with the first mainline indexing conveyor. The cart is then ready to begin carrying another tractor.
For additional information on heavy-duty material handling, call 800-523-9464 or visitwww.sipasystems.com.