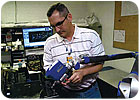
E-ONE uses the ScanArm coordinate measuring machine for part
compliance and validation and reverse engineering. Photo courtesy FARO
Technologies
Each fire rescue vehicle E-ONE manufactures contains a large amount of parts that must be measured and inspected prior to assembly. The parts include processed aluminum plates; machined aluminum extrusions; vacuum-formed plastic parts; purchased or manufactured steel parts; purchased assemblies; and steel or anodized piping. They range in size from a few cubic inches to several cubic feet.
For many years, E-ONE assemblers had used various hand tools to measure these parts: micrometers, digital and dial calipers, dial indicators, precision rules, straightedges and tape measures. Unfortunately, such tools often limited the assemblers’ ability to make sure each part met the company’s design tolerances.
For example, such tools couldn’t measure within the company’s print specification (±0.031 inch) on curved surfaces, complex extruded raw materials and vacuum-formed plastic parts. Also, the tools were unable to measure multiple parts quickly for sampling data. Finally, the hand tools lacked the ability to reverse engineer tubing and piping for routing purposes.
E-ONE considered two options to better meet their measurement needs. One was to use dedicated inspection fixtures. However, research showed that the company couldn’t properly store or maintain the fixtures.
The second, and better, option was to install a portable coordinate measuring machine (CMM) in the form of an articulating measurement arm. This led E-ONE to purchase and install the laser ScanArm from FARO Technologies in late 2009.
The ScanArm combines the contact measurement ability of the FaroArm Fusion with the noncontact scanning ability of the Laser Line Probe attachment. ScanArm also features measurement and reverse engineering software that allows E-ONE to complete inspections and create reports in one step.
“The ScanArm allows incoming inspection sampling and immediate response to part or fit up issues,” says James Musick, quality administrator at E-ONE. “This gives us the ability to immediately identify and correct root cause problems.”
Currently, E-ONE uses the portable CMM for part compliance and validation, reverse engineering, and to verify materials and fabricated part dimensions. E-ONE also uses the ScanArm to document custom-fitted plumbing applications and reverse engineer pump panel cutouts.
Musick says the ScanArm’s reporting feature is invaluable for continued process improvements. For example, E-ONE uses the reports to more accurately qualify their suppliers by holding them accountable to the specification limits they committed to.
Musick also says the ScanArm enables E-ONE to reverse engineer several parts outside its core competencies, resulting in a savings of more than 500 hours of labor annually.
For more information on coordinate measuring machines, call 800-736-0234 or visit www.faro.com.