YOUNGSTOWN, OH—Royal DSM and JuggerBot 3D recently announced a trial program that lets companies evaluate engineering-grade materials in an industrial-grade filament printer without the upfront investment in hardware.
“While adoption of additive manufacturing in production environments is increasing rapidly, many companies continue to face challenges as they work to adopt the technology,” says Jill Cohen, global marketing and sales director of additive manufacturing at Royal DSM, a nutrition, health and sustainable living company. “The two issues reported most frequently are the cost of equipment (and/or limited investment budget) and the lack of in-house expertise on various 3D printing technologies.”
“For additive manufacturing to make it into mainstream production, it requires industrial-grade printers that can process engineered materials in a reliable and consistent way,” explains Daniel Fernback, CEO of JuggerBot 3D, an additive manufacturing machine builder specializing in production 3D printing. “JuggerBot 3D has focused the design of their systems to be uniquely capable of processing a wide variety of high-performance, engineered materials, like DSM’s line of thermoplastics for additive manufacturing.”
JuggerBot’s printers are material-agnostic and standalone systems, with a built-in unit to keep filaments dry before processing them in the machine. Its patented Interdependent Drive System, using both push and pull filament extrusion forces makes it easy to streamline production. JuggerBot builds the printers at its facility in Youngstown, OH.
Initial trial customers include 3D printing service bureaus and design companies active in transportation, consumer appliances and medical prosthetic devices and sockets. They will receive hardware and material support throughout the entire trial period and only pay for a deposit and the materials consumed. The program is currently only available in the U.S.
DSM, JuggerBot Launch 3D Printing Program
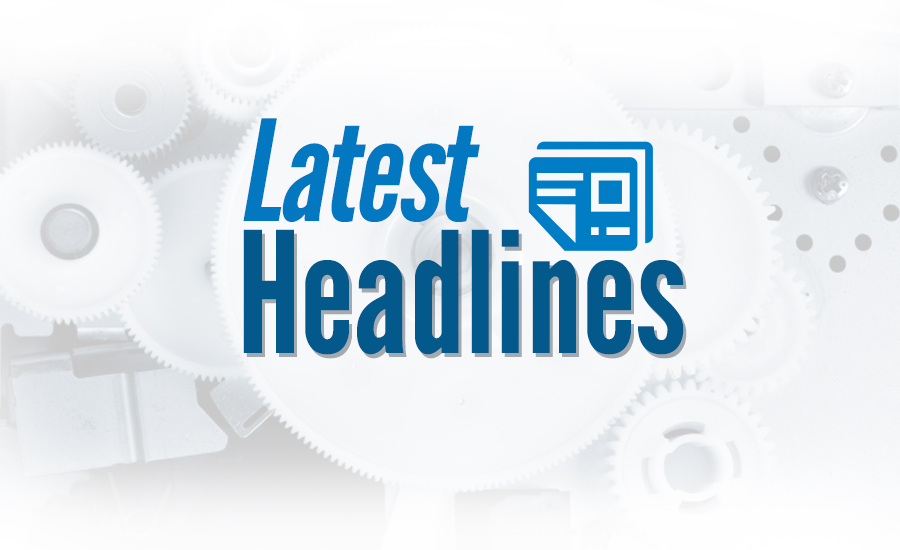