Legendary Lotus race car engineer Colin Chapman developed a philosophy that propelled his Formula 1 machines to multiple championships: “Simplify and add lightness.”
Electric vehicle manufacturers face a similar challenge: adding lightness and simplifying the process of building complex vehicles that rely on a combination of dissimilar materials.
The mechanical fastener industry is playing a critical role with innovative products that are lighter, yet have higher strength and simplify manufacturing through faster automated and manual installation. While some fasteners may be interchangeable between battery- and gas-powered vehicles, the former often present unique challenges to engineers.
Legacy and start-up automakers are asking fastener suppliers to innovate in materials science and engineering to eke out incremental weight savings for each component, while bearing greater loads and stresses. At the same time, EV fasteners must protect components against the elements.
“The EV market continues to provide great opportunities for us to introduce innovative fastening technologies,” says Gene Simpson, president of Semblex Corp. “This is in response to this market’s application challenges and their willingness to consider better joining [methods].
“The exciting thing about the EV space is the fact that it has a lot of extremely talented and experienced people who are looking to do things differently,” notes Simpson. “This creates a great opportunity for fastener companies committed to raising the bar through better products and approaches.”
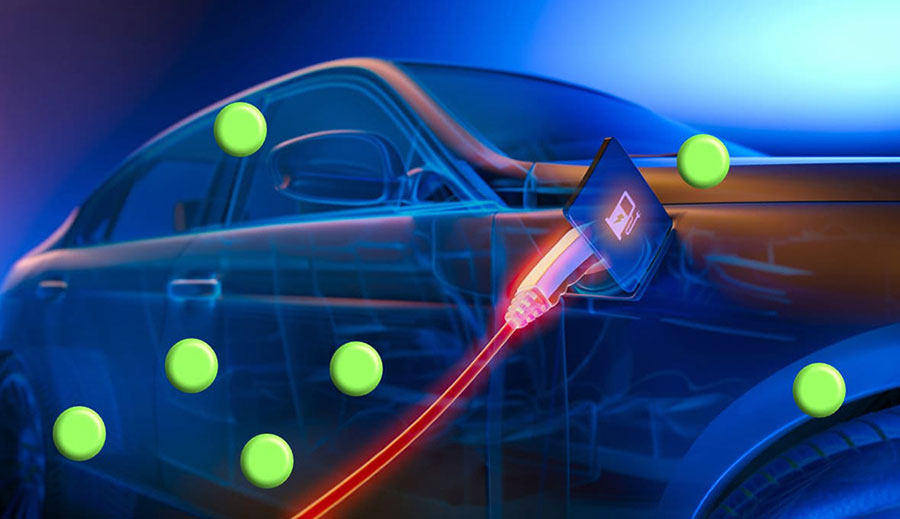
Fasteners are used to assemble battery packs, traction motors, thermal management systems and other EV components. Illustration courtesy Semblex Corp.
Maturing Market
Unlike other assembly processes, such as adhesive bonding, riveting or welding, fastening is ideal for electric vehicles, because it enables engineers to join a variety of lightweight, dissimilar materials. Mechanical fasteners also address recycling and sustainability issues, since they allow battery packs, traction motors, thermal management systems and other components to be easily disassembled.
Many first-generation EVs were designed as skateboards with separate drivetrains and battery platforms serving as the chassis, and the body was bolted on top. For low-volume premium vehicles built by start-ups, that made economic sense.
However, as designs evolve and automakers wade deeper into the EV market, batteries and associated systems are becoming more integrated with the vehicle. Today, automakers want to mass-produce EVs using more conventional assembly line practices.
“In the latest designs, many of those parts are interchangeable with traditional vehicles to improve serviceability and simplify manufacturing,” says Greg Babinec, sales application engineer at Optimas Solutions.
The first-generation EVs required fasteners that provided a sealed joint between the battery tray, skateboard and body to keep out moisture, road grime and other environmental hazards, and protect against galvanic corrosion from salt spray. In the early days of EVs, those joints between the body and aluminum battery tray may have been covered with sealants or other stop-gap measures.
As designs mature, automakers expect fasteners to seal against environmental hazards without extra manufacturing steps or expense.
Lighter, Stronger, Better
The most apparent difference in fasteners designed for EV applications is an obsession with lightweight components. The less a vehicle weighs, the more range can be coaxed from the battery. While individual fasteners may not weigh much, the cumulative mass of hundreds of screws, nuts and bolts can add up.
Optimas Solutions recently worked with one manufacturer to reduce the weight of a particular fastener by 43 percent. According to Babinec, the entire piece was reimagined from the material to the type of drive head while maintaining the strength requirements.
“It’s forced us to think outside the box and get creative,” explains Babinec.
In some cases, Optimas has applied lessons it’s learned in serving the heavy-duty truck market. Cabling and wiring harnesses must run along the frame rails in a truck, and those applications also fit EVs with large wiring requirements. Parts like brackets, plastic hose wiring and wire retention clips along the frames have larger hole sizes for more robust fasteners to account for the additional loading from heavy-duty wiring.“We have some unique [products] that provide some cost savings to our customers, because we’ve already been through that,” says Babinec.
Because automakers are moving away from using aluminum for battery enclosures and other components, fastener manufacturers have scrambled to adapt.
Profil North America, a division of PennEngineering Co., specializes in mechanically attached fasteners that are affixed during the stamping process rather than attached afterward. The majority of these fasteners are used in the body, and new materials present some challenges, says Rob Edwards, general manager.
“There’s a clear trend in leaving aluminum behind, due to the expense,” claims Edwards. “[More manufacturers are] moving toward very hard steel materials for lower price, but an equal strength. The new designs have [forced] us to develop new products for those very high-performance requirements.”
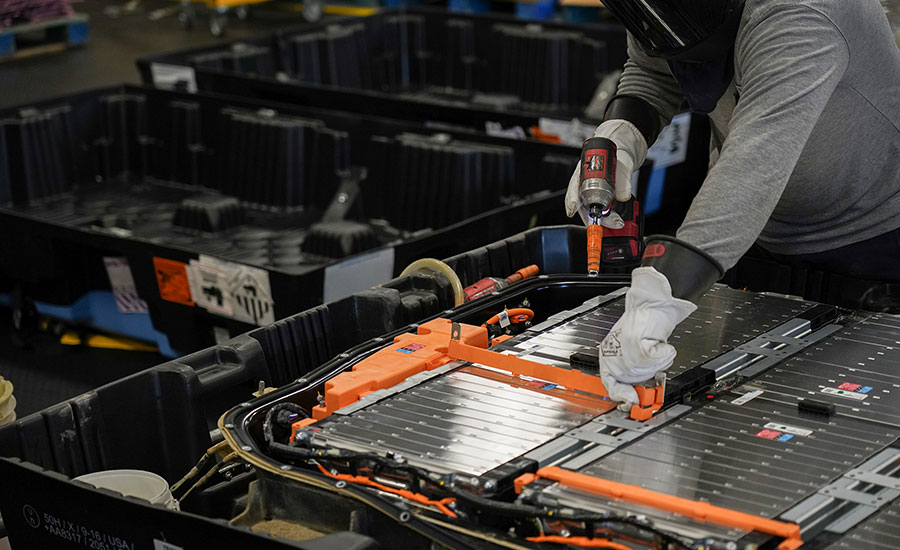
Mechanical fasteners enable battery packs to be easily disassembled. Photo courtesy Toyota Motor Co.
Pushing the Envelope
To meet high strength and low weight demands, some EV manufacturers produce components and panels with press-hardened steel, also known as martensitic steel, which is formed through a fast-cooling process similar to quenching with water.
A typical bracket on a car is made with steel that can withstand 300 megapascals of pressure. A component for an EV formed from press-hardened steel is rated for 1,500 megapascals.
“It’s five times the strength, so you can make the part much lighter and still get the performance you need,” Edwards points out.
However, those components are so hard, it’s challenging to weld fasteners to them or use mechanically attached fasteners. Plus, they have coatings that make welding nearly impossible.
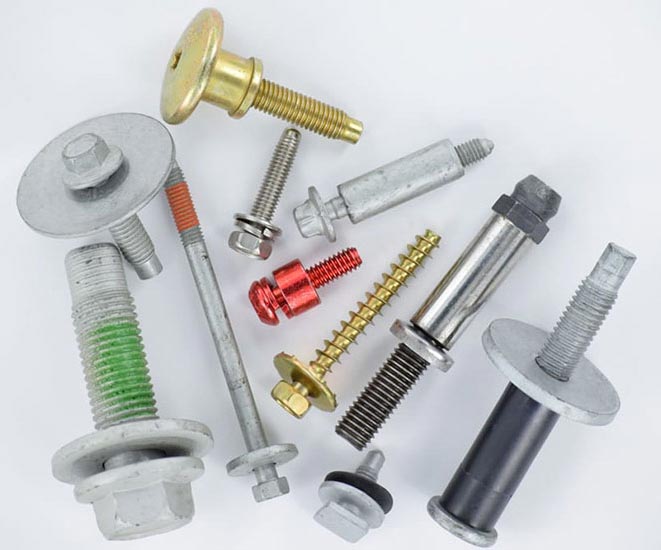
Fastener suppliers are adapting existing products to meet the unique high-voltage requirements of electric vehicles. Photo courtesy Semblex Corp.
Profil worked with one European OEM for nearly a year to develop a fastener with a metal-to-metal watertight seal that joined the battery tray to body panels formed with press-hardened steel. No sealants or adhesives were allowed.
With ordinary steel, the fastener’s torque bars or spokes would bite into the metal, holding the piece in place.
“Making the metal-to-metal joint in high-strength steel required an outrageous amount of torque, so we worked on developing new fastening techniques and materials,” says Edwards.
The solution was to stamp a hexagonal opening instead of the usual circular opening, to give the fastener more grip, and redesign the fastener to match up with the new site.
That innovation was only the first step. The fastener had to be redesigned so that it wouldn’t slow down the automated installation process. When the fastener entered a round slot, it didn’t matter which way it was oriented. The new design reshaped the fastener with flat sides to orient it to the hexagonal opening.
“They’re being installed at the rate of one part every 1.25 seconds, so there’s no time to orient it by hand,” explains Edwards.
The bolts are torqued so much that they stretch slightly to ensure the metal-to-metal seal between the battery tray and the car’s floor pan. The hex arrangement provides the torque resistance necessary to achieve a watertight grip.
Edwards and his colleagues are working with manufacturers and suppliers to place the fasteners in the stamping die while a panel is pressed. The red-hot panel comes out of a furnace and into the die, where it is shaped into a door frame or other body component. The trick is that the press-hardened steel cools and turns solid in 6 seconds after it’s stamped.
“You get one shot to put the part in the die and form it,” says Edwards. “After that, you can’t touch it again.”
Safety First
With so much electrical energy onboard electric vehicles, automakers are looking for ways to safely handle current and the heat generated from it. To address the challenges, suppliers are adapting existing fasteners to meet the unique high-voltage requirements of EVs. Bus bars, brackets and other components must withstand the heat generated from battery packs, so highly thermal-resistant products are critical.
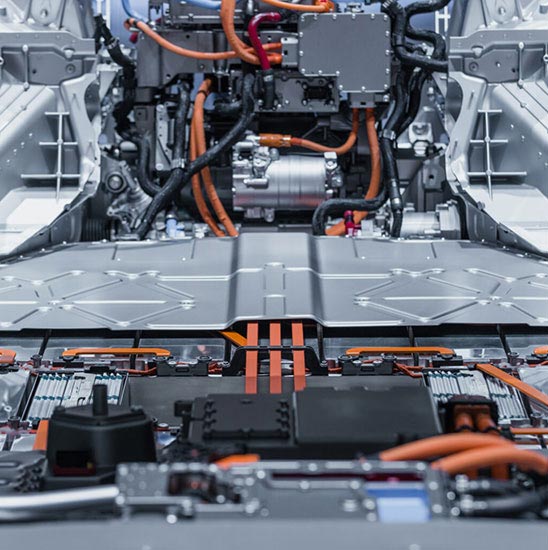
Fasteners are used for a variety of battery enclosure assembly applications. Photo courtesy Profil North America, a PennEngineering Co.
“We have altered some cold-formed mechanical parts for battery cells,” says Stefan Schneider, global product manager for electrification products at Stanley Engineered Fastening. “We adapt our fasteners to remain stable for a longer period, especially in battery venting, which is a safety-critical application,” Schneider says.
Fasteners for many electrical components are designed to be connected and disconnected on a regular basis, while also carrying current up to 400 amps safely.
“We’re looking at not only the mechanical side of the joint, but also things like materials and thermal expansion between different materials,” explains Mark Chadwick, e-mobility segment director at PennEngineering. “That’s meant a lot of investment for new test equipment and engineering capabilities to meet customer requirements we have not seen in the past.”
Because EVs are so quiet, any place where two components are joined has the potential for squeaks and rattles. Fastener suppliers have developed clips with noise-absorbing materials and features to ensure EV buyers aren’t disturbed by NVH issues.
The rise of megacastings in the EV drivetrain has also presented new challenges. Megacastings use much harder material than traditional sheet metal components, so punching a hole or welding on fasteners is difficult.
Stanley Engineered Fastening developed a no-hole stud welding system for fully automated installation. Fasteners used on battery boxes can be removed to allow servicing for the battery components. The no-hole system also supports helium tightness requirement for battery packs.
“It’s a brilliant solution,” Schneider points out. “When there’s no hole, you have no leakage.”
However, one problem with pushing the envelope on some new applications is complying with ISO standards for fasteners. “There are some fundamental limits to what we can do and still meet the standards,” says Profil’s Edwards.
Advanced Assembly
Uptime is critical for automotive assembly lines. The goal is to supply the best fastener for the application, considering force requirements and ergonomics for operators to keep up with the pace of the line.
“We work to the feed line quicker, get the takt times down and improve efficiency, while maintaining quality and the design constraints for the application,” says Optimas Solutions’ Babinec. “We look at not just the fastener’s design, but the overall installed cost.”
For example, a fastener supplier can provide bolts with washers already fitted to save time on the assembly line. Suppliers can also help EV automakers consolidate fasteners to reduce costs and complexity. One recent analysis reduced a manufacturer’s bill of materials by 49 percent, resulting in significant cost savings and a reduction from 167 to 86 items.
Fasteners have played a critical role in automotive industry since Karl Benz rolled out his three-wheeled contraption in 1886. The transformation from ICE to EV won’t change that, and fastener innovations will continue to drive performance improvements.
“Fasteners will always be required in the industry,” claims Babinec. “We’re taking all our technology developed to this point and applying it a little more aggressively to the EV industry.”