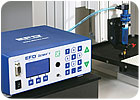
The beauty of a benchtop time-pressure dispensing system is its simplicity. An adhesive or other fluid is packaged in a disposable syringe. An end cap connected to a compressed air line fits over the end of the syringe. An electronic controller applies a measured amount of air pressure, for a measured amount of time, to the back of the syringe, forcing the material out the tip.
Inexpensive, fast, flexible and easy to operate, these systems can be handheld or mounted to a Cartesian robot. Syringes are available in sizes ranging from 3 to 55 cc. When the syringe is empty, it’s thrown away. No cleaning is required.
“By changing the time and pressure, you get different quantities of adhesive,” says Tom Bray, applications design engineer at Hernon Manufacturing Inc. “You can dispense a wide range of materials, from very low-viscosity liquids to very high-viscosity pastes.”
Finding the right combination of time and pressure for a particular material requires some experimentation. “You want to start with shortest time, lowest pressure and smallest tip you can,” says Bray. “From there, you work your way up: more time, more pressure, bigger needle.”
Although time-pressure systems have been around for decades, the technology has not remained static. Indeed, equipment suppliers have recently introduced a number of improvements to the technology.
One of those improvements has been digital control. In the past, when operators wanted to adjust time or pressure, they turned dials. Now, operators enter in the exact numerical settings.
“Instead of a potentiometer or an internal timer, you have digital readouts,” says Vladimir Siroky, director of operations at Fisnar Inc.
Digital control also gives engineers the ability to store and recall time-pressure settings for specific materials. It also permits them to lock settings to prevent operator adjustment, and it enables them to program automatic adjustments to those parameters over time.
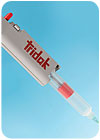
Problems and Solutions
For the most part, time-pressure dispensers are very repeatable, says Bray. Two common sources of variability in shot size are fluctuations in air pressure and material temperature. The former can be addressed with a precision pressure regulator. The latter can be addressed by warming or insulating the material supply.One problem with time-pressure systems is that their performance can decline as the syringe empties. Less time and pressure are needed to dispense a given volume from a syringe with 25 cc of adhesive and 5 cc of air than from a syringe with 5 cc of adhesive and 25 cc of air. As a result, if time and pressure settings remain constant, the shot size can diminish over time.
Assemblers can overcome that problem by dispensing from smaller syringes or starting with syringes that are less than full. “That way, there’s less of a [volume difference] between a full syringe and an empty one,” says Mike Vidal, engineering manager at EFD Inc.
EFD has come up with its own solution to the problem that doesn’t require any sort of adjustments or volume compromises. It’s called the Optimeter. The central component of the Optimeter is a cone-shaped pin. The base of the cone is connected to the piston inside the syringe.
When the syringe is full, the narrow end of the cone passes through the air hole of the end cap, limiting how much air pressure can be applied to the piston, explains Vidal. As the syringe empties, the cone moves down with the piston, gradually retracting from the air hole and allowing more pressure to act on the piston.
“What’s nice about the Optimeter is that it’s passive,” says Vidal. “You don’t have any fancy electronics or feedback loops. It’s like a spigot. As the barrel empties, it opens up the flow more. You get the same pressure pulse with a full barrel as you get with an empty barrel.”
The Optimeter is available for 10 and 30 cc syringe barrels. “The taper on the pin is optimized for each barrel size,” says Vidal.
Another common issue with time-pressure dispensers lies with reactive materials, such as epoxies, that change in viscosity over time. As these materials thicken, more pressure, more time or both are needed to maintain a consistent deposit size. If time and pressure settings remain constant, the shot size will decrease over time.
Here, too, suppliers are rising to the challenge. For example, the Ultimus V digital dispenser from EFD can be programmed to match the viscosity changes of the material, automatically adjusting time and pressure settings at set intervals of time or amounts of deposits.
For instance, say an epoxy becomes markedly thicker 10 minutes after it’s mixed, and thicker still 20 minutes later. An engineer can program the unit to dispense at a certain time and pressure for the first 10 minutes, another time and pressure for the next 20 minutes, and a third time and pressure for the remaining material. Alternatively, the unit could be programmed to dispense at a certain time and pressure for the first 200 shots, another time and pressure for the next 400 shots, and a third time and pressure for the remaining material.
“There is some up-front work that has to be done to understand the viscosity profile of the material,” notes Vidal. “However, once you develop the profile, the material is generally going to behave in the same way.”
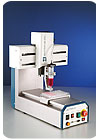
Time-Pressure Alternatives
The time-pressure unit isn’t the only game in town for benchtop dispensing. Suppliers have introduced numerous alternatives over the past few years.One alternative is a pinch-tube system. With this type of dispenser, the material is held in cartridges or pressure vessels rather than a syringe, and it flows to the dispense point through a flexible tube. The container can be pressurized, or the material can flow to the dispense point via gravity.
The dispenser is a handheld pen-like instrument. When the operator depresses a lever, material flows out the tip. This type of system can dispense both low- and high-viscosity materials, including solvents and cyanoacrylates.
For more control, the tube can be run through a pneumatically operated pinch valve instead of a handheld pen. With the valve mounted to a stand on the benchtop, the operator positions the assembly beneath the tip and activates the dispense cycle via a foot-switch.
The chief advantage of this type of system is that the fluid path is disposable, says Shawn Cole, product manager at Tridak LLC. Because the fluid is sealed within the tube, it never contacts the valve’s inner parts. This simplifies changeovers and minimizes maintenance and cleanup.
“It prevents contamination,” says Cole. “There’s no chance that the [current] fluid will contact with whatever fluid the valve dispensed previously.”
Positive-displacement control and suck-back are available with some pinch valve models. Tubing comes in a variety of materials, such as urethane, Teflon, silicone and polyethylene. Inside diameters range from 0.066 to 0.375 inch. A typical flow rate with a tube with an inside diameter of 0.095 inch is 15 milliliters per second.
Another option for low- and medium-viscosity materials is a pneumatically operated, handheld diaphragm valve. Shaped like a wand, the valve body is made from Delrin, and the diaphragm is made from Teflon-coated silicone. When the valve is actuated, pressurized material forces back a piston, which releases the diaphragm off its seat and enables the fluid to pass by to the dispense tip. Because the diaphragm separates the wetted parts from the air supply, the valve is suitable for dispensing cyanoacrylates, reagents, anaerobic material, solvents, glue, electrolytes and alcohols.
“With a diaphragm valve, there are no internal mechanics,” says Cole. “The diaphragm is compatible with most materials.”
For precise applications, another type of benchtop dispenser uses a leadscrew driven by a stepper motor to push the piston, instead of compressed air. Each turn of the motor pushes the piston forward a set amount, explains Nancy Gleason, director of business development at Fishman Corp. Based on the volume of the syringe and the pitch of the screw, the system calculates how far the piston must travel to dispense the desired amount of material. The amount dispensed remains constant, regardless of the viscosity of the material or the volume remaining in the syringe.
An interference fit between the piston and the syringe prevents pressure loss and keeps material from slipping past the piston, says Gleason. In addition, the piston can be programmed to pull back after each dot is dispensed, which keeps material from oozing out of the tip.
With a 3 cc syringe, a leadscrew for large volumes can dispense dots as small as 0.0009 cc with a standard deviation of three sigma. A leadscrew for small volumes can put down dots as small as 0.00023 cc.
Another motor-driven alternative to the time-pressure unit is a peristaltic pump dispenser. As with a pinch-tube system, the adhesive travels from a reservoir to the dispense tip via flexible tubing. Instead of using compressed air to force out the adhesive, a rotor turns a series of rollers that press against the tubing. With each turn of the rotor, the rollers push a set amount of adhesive forward in the tubing.
“It works like your esophagus,” says Siroky. “It’s a positive-displacement technology, and it’s very easy to control.”
Because it’s a closed system, the device is ideal for dispensing volatile or hard-to-work-with materials. Safe for use in clean rooms, the peristaltic pump can operate in manual or timed modes. Reversing the rollers slightly produces a suck-back to prevent drips from the dispense tip. Equipped with a Teflon tube, it can output 0.01 to 6 milliliters per minute. With a silicone tube, it can put out 0.1 to 20 milliliters per minute.
On the opposite end of the spectrum, assemblers can avoid any electromechanical control at all with a device like the Microdot from Tridak. This thumb-actuated device accepts 5- and 10-milliliter syringes. Each click of the thumb-switch pushes the piston down a set amount. Shot size is adjusted using a knurled knob near the top of the unit, and a safety lock prevents accidental actuation.
“The Microdot allows you to move around freely, and you get a very repeatable shot with each click,” says Cole. “We have customers who use it for doing rework in warehouses. They can take all the adhesives they need with them and just use the one dispenser.”
When dispensing a material with a viscosity of 400 centipoise, the device can put down a shot as small as 0.003 milliliter with a 25 gauge taper tip or as large as 0.17 milliliter with a 14 gauge taper tip.