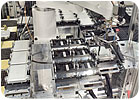
Machine tending is the most common task for robots in test and inspection. Here, a SCARA robot shuttles electronic assemblies in and out of functional testing fixtures. Photo courtesy Delphi Electronics & Safety Div.
Machine tending is the most common task for robots in test and inspection for two reasons. First, test and inspection often takes more time than assembly. To prevent a bottleneck, a robot can be programmed to tend multiple test fixtures or to perform some other operation while a test is performed.
For example, one manufacturer uses a SCARA robot to shuttle valves in and out of a leak testing station. The station has three test fixtures, and the robot’s end-effector handles two valves at a time. At the start of a cycle, two pallets arrive on a conveyor. The first pallet carries 63 valves; the second is empty. The robot picks up the valves one at a time and loads them into the fixtures. By the time the third valve has been loaded and a fourth valve has been picked up, the test on the first valve is finished. At this point, the robot retrieves the first valve, swaps it for the untested valve, and places the tested valve in the empty pallet. It then returns to pick up another untested valve, and the process repeats itself.
The other benefit of using robots to tend test and inspection equipment is error-proofing. If an assembly fails a check, the robot immediately puts it in a reject bin. There’s no chance for a careless operator to accidentally place a faulty assembly among good product.
“I recently met with a customer who wants to use a robot to present an injection-molded part to a vision system for inspection,” says John C. Clark, national sales manager for EPSON Robots (Carson, CA). “The robot would then segregate the parts based on the results of the inspection.”
If it’s impractical for the robot to present parts for test and inspection, the robot can bring the equipment to the parts. For example, a Tier One supplier uses a six-axis robot to inspect frames for pickups and sport utility vehicles. The robot’s wrist is equipped with a vision sensor instead of a gripper. When a frame arrives at the inspection station, the robot positions the sensor at multiple locations on the assembly to ensure that parts have been attached and holes have been punched correctly. Certainly, this application could have been accomplished with multiple cameras in fixed positions. However, mounting the camera to the robot saved integration costs and also enabled the supplier to inspect different models without spending time on changeover.
Sometimes, a robot can perform an inspection while it handles a part, says Milton Guerry, sales and marketing manager for Schunk Inc. (Morrisville, NC). A gripper can be equipped with a sensor that measures the part when it’s picked up. If the part is supposed to be 1 inch wide, but the sensor says it’s 2 inches wide, the robot rejects the part.
More intriguing are test and inspection applications in which the robot takes an active role in the process. For example, a cell phone manufacturer uses a SCARA robot to perform functional testing. A finished phone is placed in a fixture and powered up. The robot then presses various buttons to determine if the buttons and display function correctly. Similarly, an automotive OEM uses a six-axis robot to perform accelerated life testing on interior components, such as shift levers and seat backs. A particularly slick application was developed by a manufacturer of water heaters for aquariums. The company uses a benchtop Cartesian robot to calibrate thermostats. The robot is linked with electrical testing equipment. After positioning a screwdriver onto a calibration screw on the thermostat, the robot then turns the screw until the appropriate electrical output is detected by the test equipment.