As the appliance industry becomes increasingly competitive, refrigerator and freezer original equipment manufacturers (OEMs) are challenged with changing energy standards, as well as the need to maximize quality and efficiency in their manufacturing facilities. In particular, they need to reduce the cycle times for the production of refrigerator and freezer cabinets in order to maximize the capacity utilization of their plants.
The development of polyurethane insulating foam that allows the foamed refrigerator cabinet to be demolded faster can help address this challenge. In the past, optimized additive and catalyst packages and improved foam processing technologies have led to significant advances in reducing demold times, but novel chemical approaches are now required to further reduce this process.
The industry is developing new chemistries that allow for the development of customized polyurethane foam systems that meet the demands of OEMs for faster demolding systems. This innovative, fast-demolding technology allows OEMs to produce cabinets with improved production efficiency while supporting energy efficiency and other important quality parameters of the refrigerator itself.
An Industry Facing New Challenges
The desire for increased energy efficiency is one of the major driving forces in the appliance industry. In household refrigerators, the performance of polyurethane foam insulation contributes greatly to the appliance’s overall energy efficiency. The chemistry’s constituents increase the thickness and the overall insulating ability of the foam. However, with increased thickness comes increased post demold swelling. If the foam is overly thick and the foam is demolded too soon, the heat and internal pressure generated during the foaming process can lead to splits forming in the center of the foam. This can hurt a refrigerator’s performance and ultimately decrease its energy efficiency.
Refrigerators must also meet specific size specifications. Many homes have standard spaces into which the refrigerator must fit. If the refrigerator’s actual width exceeds its stated dimensions because of foam swelling, it may not fit into these spaces. On the inside of a refrigerator, excessive swelling of the side walls could result in shelves or other components not fitting properly.
Of course, one way to reduce the amount of post demold swelling is to increase the demold time. However, this can result in loss of productivity, or the need to purchase additional foaming equipment. Thus, a shorter demold time is critical to both production rates and efficiency to the manufacturer.
At the same time, consumer trends in cabinet design require even more improvements in the insulation performance of the foam. To accommodate customer desires for improvements in design, cabinet walls are becoming thinner to increase the usable space within the refrigerator. Furthermore, within the walls, lights, wiring, control panels and other electronics are embedded to support additional features of the refrigerator. These objects added within the walls can potentially obstruct foam flow and degrade the foam performance.
OEM Foaming Operation
Insulating household refrigeration cabinets and doors with polyurethane foam is a unique process at the OEM. It is the step between the pre-foam assembly operation, which creates the metal shell, wiring, lights and liner, and the final product assembly operations, where the doors, compressors, evaporators, and other components are added. In the insulation step, the OEM combines liquid polyurethane raw materials to make the finished polyurethane foam.
The pre-foamed cabinet or door is placed within a fixture to limit the expansion of the polyurethane foam. During the foaming process, the interior of each cabinet and door is where the chemicals react and the polyurethane foam is produced. The raw material suppliers will generally establish process conditions for the OEMs to allow manufacturing of the correct finished product with the required properties.
The total residence time in the foaming operation may be relatively brief, but many things happen during the process. Before the raw materials are pumped into the cabinet or door, the part is brought into the fixture, the fixture closes and then the mixhead is aligned. The raw materials are then metered, mixed and automatically poured. The pour generally takes less than five seconds. The reaction begins with mixing and the foam flows and fills the space between the inner and outer shells in less than 30 seconds. The thickness of the cavity and what the cabinet designer has placed within the cavity and the cavity configuration largely influence what happens in those few seconds between pour and fill.
There are many processes occurring simultaneously when a cabinet is filling with polyurethane foam. Polymerization of the raw materials is occurring, carbon dioxide is being generated by the reaction of chemicals and water, heat is released from the reactions, and the physical blowing agent is being vaporized. This causes bubbles to form within the liquid. The gases within the bubbles expand due to heat. The air in the cavity is displaced as the foam expands, and the viscosity of the foam increases as the reactions proceed toward completion and the liquid raw materials react and turn into a solid foam.
After the foaming process, the cabinet and door stays within the fixture for a specified amount of time (typically two to seven minutes) before it is demolded. The time between the initial shot of liquid raw materials until the fixture is opened so the part can exit is the demold time for the part. After demolding the part, the fixture is opened, the part removed, and the process repeats with the next part. The total residence time may be five to 20 minutes, with the demold time comprising a portion of the total residence time.
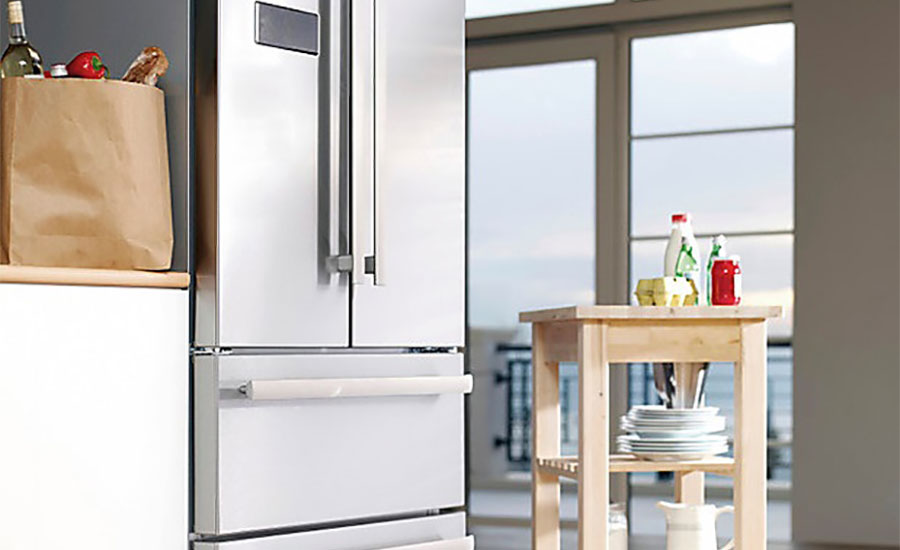
In household refrigerators, the performance of polyurethane foam insulation contributes greatly to the appliance’s overall energy efficiency.
New Chemistry Changing the Demolding Process
The production of rigid polyurethane foam in a cabinet requires two main liquid components: a polyol, which is an alcohol with more than two reactive hydroxyl groups per molecule, and a polyisocyanate, along with a suitable blowing agent. The blowing agent is typically added to the polyol along with additional additives like surfactants (a foam stabilizer) and catalysts (to control the reaction rate). The reaction that takes place when the polyol and polyisocyanate are mixed together results in macromolecules with urethane structures—polyurethanes. During the reaction, a considerable amount of heat is released, which is used in part to evaporate the blowing agent. As a result, the reaction of the liquid mix is expanded to form foam.
Besides the catalyst, the composition of both the polyol and the isocyanate can have a dramatic effect on the post demold expansion. With a given set of base polyether polyols or isocyanates, an optimized formulation can be developed that provides a balance of productivity, cure rate, and flowability in order to produce a material tailored to the specific processing technologies. The industry is expanding the optimization to include new polyethers as well as new isocyanates that result in reductions in the demold swelling of the foam, which can yield about 20 to 40 percent reductions in actual demold time in cabinets.
The polyurethane backbone can be modified to create structures that reduce post demold swelling and give more optimal flowability, viscosity growth, strength and thermal insulation in the polyurethane foam. The polyurethane backbone is controlled by changing the functionalities, molecular weights and viscosities of both the polyethers and isocyanate structures to produce the optimal results.
In addition to the demold performance, research has shown that the newly developed polyurethane formulation matches or exceeds the performance of the current systems in key properties like density, compressive strength and thermal conductivity.
Keeping Pace with An Evolving Industry Through Innovation
Post demold expansion is a fundamental characteristic of rigid polyurethane foam that affects both production processing and performance. To meet the OEM’s need to increase productivity without compromising quality features like energy efficiency or cabinet geometry, novel chemical polyol and isocyanate structures have been developed, tested and applied for fast-demold foam systems.
The innovative polyurethane system has been found to result in best-in-class post-expansion values, allowing for enhanced process productivity. Excellent flowability leads to homogenous density distribution and supports the economical production of energy-efficient refrigerators.
A more detailed report of these findings will be presented at several international polyurethane conferences this year, including CPI’s 2018 Polyurethanes Technical Conference, which will be held October 1-3 in Atlanta. In addition to presenting new innovations in the field of appliance insulating foam, the CPI Conference offers critical insight and education on innovations across the wide range of polyurethane application areas.