Two typical appliances using draft inducer blowers to improve gas combustion performance and appliance efficiency are the gas furnace and gas water heater. The market for these appliances has been growing rapidly. Like the gas furnace before it, new and proposed legislation mandating reduced gas byproducts and improved efficiency is now pushing the gas water heater to greater use of the power venter blower, a subset of the draft-inducer blower category.
Once you have determined the need for the draft-inducer blower, you must now decide what type of technology to use for the motor. Two motor technologies are in widespread use. These are the PSC and the Shaded Pole motors. A variation of the Shaded Pole motor covered in this article, the full-round type, is the C-Frame motor. The C-Frame motor is also a Shaded Pole motor with lower efficiency, reduced operating life, and a greater tendency for noise. As a subset of the Shaded Pole category, the C-Frame is a lower cost option with exaggerated weaknesses.
The motor
A Permanent Split Capacitor (PSC) motor is an induction motor (meaning it has no brushes) that uses two sets of copper coils in a multi-tooth stator arrangement. These coils, along with the capacitor, act to create a near two-phase motor. Typical PSC designs result in a motor where the optimum performance occurs at one point on the speed-torque curve. The operating range around this speed point is where the design approaches two-phase performance.The Shaded Pole motor is also an induction machine. It is considered a salient pole machine because a single set of coils is wound around a single tooth which makes up each 1/2 pole. In addition to the wound coil a second band of copper, called a shading band, is inserted onto part of each tooth face. The combination of the main wound coil and the shading band give a sense of two-phase operation. Unlike the PSC motor a Shaded Pole motor never approaches two-phase operation.
Two-phase operation
Two-phase operation for the PSC motor is somewhat analogous to the operation of a three-phase motor. The design speed efficiency is high, torque pulsations are low and the windings carry equivalent values of torque. Since the motor is actually operated from a single-phase source the near two-phase characteristics do not hold under the starting condition. Since the performance is balanced for the running condition the starting performance is reduced as compared to a true two-phase machine.The blower
Two general types of draft-inducer blowers are used to improve the performance of a furnace or water heater. Both blower types use a multi-blade wheel to deliver the air volume within a specified pressure range. The primary difference in the two types of blowers is in the housing material. Higher temperature applications, generically called 80+ designs, require metal housings to handle the heat while providing a low cost product. The 80+ furnace is so named because it operates in an 80 percent energy efficiency range. Lower temperature applications, generically called 90+ designs, operate at much lower temperatures, allowing the use of engineered plastic blower housings and impellers. The 90+ furnace operates in a 90 percent energy efficiency range and are called condensing furnaces. The acidic condensate requires a change to plastic housings and wheels where compatibility is easier to achieve.Considerations
In order to properly select a motor for the blower, one must evaluate the needs of the application such as:• Performance capability at the design points.
• Performance capability across the range of application conditions.
• Sound qualities during steady-state operation.
• Sound qualities during starting (will the blower take too long to start emphasizing the noise at start-up).
• Energy efficiency.
• Operating cost.
• Operational lifetime.
• Motor weight.
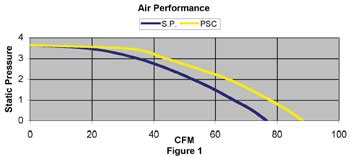
Performance
As seen in Fig. 1, the PSC motor delivers a higher maximum CFM for each static pressure point. This additional air delivery results in a system that is capable of supplying the needed air even when the installation is less than ideal. Allowing the furnace installation technician to safely and efficiently install the furnace with longer vent-pipe restrictions or with 2-in. versus 3-in. OD pipe could be the difference between a successful installation and a problematic installation.The additional air performance is inherent in the PSC motor. First is the capability of the PSC motor to develop higher operating speeds. This may mean a peak operating speed of 3,400 RPMs versus 3,250 for the Shaded Pole. The PSC motor also develops greater torque throughout the operating range which accounts for higher maximum flow. In Fig. 2 one can see the difference in motor performance between the two types.
The maximum torque developed in each type of motor is referred to as breakdown torque. The PSC motor design has significantly higher breakdown torque and, therefore, a higher flow-pressure capability.
It is also important to note that the Shaded Pole motor has a significant dip in the torque curve below breakdown, highlighted area. This is the induction cusp, sometimes called the harmonic cusp. In under-voltage installations the presence of the cusp near the load line of the blower system can result in a failure to accelerate to full speed. The blower could perform at half its rated flow. This condition must be avoided by careful attention to testing details, including under-voltage testing, and by manipulating design parameters. Design parameter adjustments will result in an increase in losses for the Shaded Pole motor.
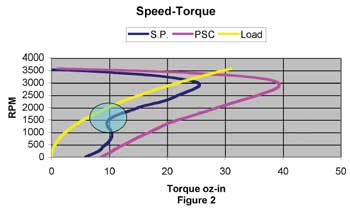
Sound
The characteristics that make a PSC motor well-suited from a performance standpoint also lend themselves to reduced sound levels. During steady state operation the near two-phase design results in low to very-low levels of pulsating torque. Pulsating torque can excite the blower wheel or housing so maintaining low levels is very important. The use of the shading bands in the Shaded Pole motor results in torque harmonics. Torque harmonics are more likely to excite the blower wheel or housing leading to audible noise generation. Using isolation mounts on the wheel or housing can dissipate some of the unwanted energy, though not without adding complications and cost.Referring back to the speed-torque curve, it is apparent that, during starting, the blower using the Shaded Pole motor will take longer to start. Any noise present during starting will likely be more noticeable due to this longer starting time. The cusp once again comes into play as a noise consideration. As the blower accelerates through the cusp region the rate of acceleration will fall then rise again increasing the potential for a noticeable noise.
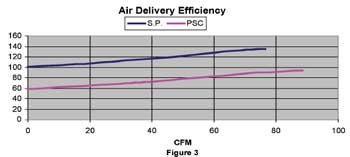
Efficiency and operating costs
In terms of pure efficiency, the PSC motor again prevails. Where a PSC motor can achieve a peak efficiency of about 65 percent, the Shaded Pole motor will peak at around 35 percent for a full-round lamination design. The C-Frame peaks in efficiency at 30 percent for an equivalent output. In Fig. 3, one can see that the Shaded Pole motor is consistently about 40 watts higher than the PSC for the same air delivery. It might be interesting to note that in the hunt for power reductions in the 1/2HP and larger furnace distribution blowers it is not uncommon to look for 10-watt to 20- watt reductions for improved energy ratings. This watt reduction is driven by cooling efficiency calculations. At present the losses in the draft inducer may not be a primary consideration, though they are significant when compared to changes required in the distribution blower. However, proposals to add the draft inducer energy component to the overall system efficiency calculation will probably change this in the not too distant future.If the draft inducer operates at a typical 1,200 hours per year, the annual energy difference between these two motor types is about (40 watts * 1200 hours) = 48 kWatt-hours. The PSC motor can significantly lower energy costs over the life of the appliance.
Operational life and motor weight
Complicating the analysis is the issue of operational life. The extra watts consumed by the Shaded Pole motor are all losses. These extra losses result in a significant increase in winding temperatures leading to increased bearing temperatures. In all cases the effect on the design is to increase the length of the stator to more readily dissipate the heat. The added length also adds significant weight. In some cases another compromise is made with the addition of an internal cooling fan in the motor. This may be more cost effective than adding only stator length, but will certainly add to the noise component.Conclusion
The best motor for the job is obviously the motor that can meet all of the application requirements for the least cost. For applications where the prime driver is unit cost, the Shaded Pole motor can be a suitable compromise.It is very evident that, considering energy use, the PSC is an energy-saving choice. The PSC-driven blower will cover a larger range of appliance installations and deliver air-power with reduced sound levels while providing increased reliability. When the total cost is considered it may be that the PSC motor results in fewer call-backs to service troublesome venting applications.
With the push by many customers and government agencies mandating higher efficiency the PSC motor is the one with obvious payback potential.
The future
Draft inducers with the capability to operate over wide flow ranges with high operating efficiencies are ready for furnace and water heaters of the future. As AFUE standards required more efficient gas combustion ten years ago, electrical operating efficiency requirements are on the horizon. The PSC motor will play a major part for appliances that currently use Shaded Pole motors.Advanced performance for multi-stage and continuously variable furnaces can be accomplished using a variable speed motor with Electronic Performance Control. Patented algorithms allow an electronic control to modulate the draft inducer or power venter to automatically provide the correct flow as variables change with the installation and over time. Long vent runs, partial obstructions, and under-sized vent pipes are no match for the wide performance capability of these blowers. It is also possible to minimize the blower envelope by using these electronic performance controls.
For reprints of this article, contact Jill DeVries @ 248-244-1726 or devriesJ@bnpmedia.com.
If you have read this article, enter 104. For more information, enter 103.