The large-scale adoption of electric vehicles (EVs) is causing growing pains, particularly for battery manufacturers. Batteries can account for more than 50 percent of an EV’s cost. Manufacturers are striving to produce safer batteries while lowering costs and increasing throughput.
Machine vision and artificial intelligence (AI) are vital in automating complex inspections and reducing bottlenecks. The difficulty level in deploying AI has historically been a significant implementation roadblock for those with limited data science experience. However, new methodologies are making the technology more user-friendly for automakers and battery manufacturers.
The Traditional Machine Vision Approach
The automotive industry is one of the largest adopters of machine vision. The technology is used to automate numerous guidance, inspection, alignment and measurement applications. Developing traditional, rule-based vision applications requires skilled engineers to evaluate each vision task, apply rules to solve the problem, and program accordingly.
Rule-based machine vision is suitable when defects are visually consistent and clearly detectable, but it struggles when flaws vary in appearance or location, or when there are subtle differences between acceptable and flawed components. For example, in EV battery cell surface inspection, flaws such as scratches and craters come in different shapes and sizes. EV battery cell surfaces are reflective and have complex textures and nonuniform surfaces, complicating defect detection. Separating these flaws from similar, but acceptable, cosmetic blemishes is too difficult for rule-based vision systems. The technology cannot account for every defect iteration.
Moreover, maintaining rule-based solutions is an ongoing challenge. Whenever there are changeovers, technological advancements, new processes, or changes to the environment, the algorithms need to be adjusted.
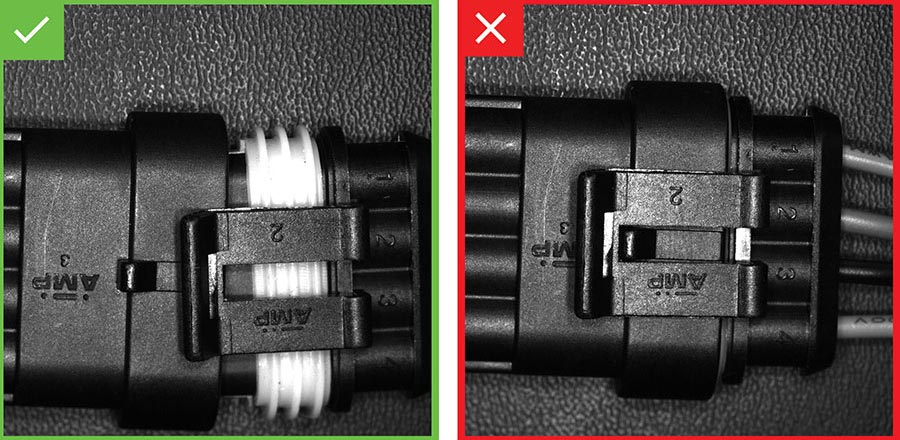
By leveraging edge learning technology, vision systems can validate the correct insertion of connectors in wiring harnesses using only five to 10 training images per class. Source: Cognex Corp.
The Evolution of AI in Machine Vision
Deep learning is AI technology that is proven to be effective in machine vision applications. This technology automates defect detection by analyzing large data sets comprised of thousands of images through a graphics processing unit (GPU). The technology was designed for applications that require decisions and applications with high complexity or extreme variability.
Minute defects, complex textures, reflective surfaces and high-speed operations are the norm in EV battery manufacturing. Electrode coating, one of the first steps of the EV battery manufacturing process, entails pouring a mixture of carbon, graphite, binding materials and other elements onto anodes and cathodes so they can retain electrical conductivity. Defects such as holes, bubbles or contaminants in the mixture degrade battery performance and, at worst, can cause an electrical shortage or fire.
Deep learning is a powerful technology that automates the most complex inspection tasks, such as electrode coating inspection. The technology recognizes small defects and accounts for new types and shapes of flaws, even in low-contrast environments like the black, glossy electrode coating mixture. Combined with high-resolution machine vision systems, this AI-based technology accounts for variable defects in different areas, even against complex textures in poor contrast environments.
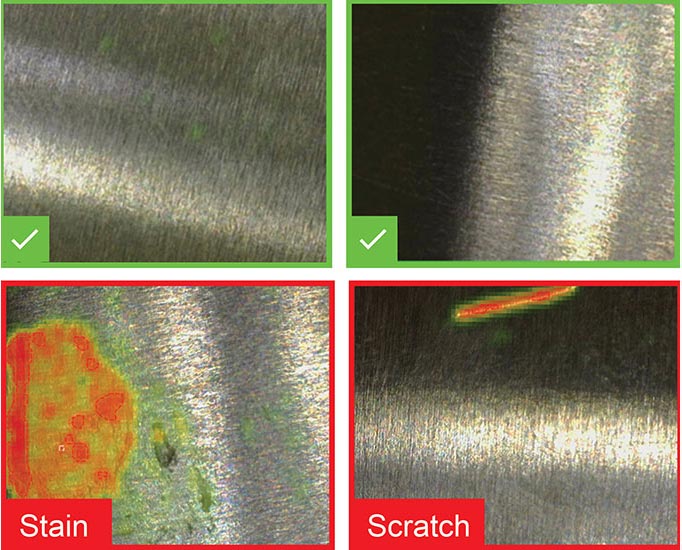
Edge learning technology and machine vision can identify and categorize defects while distinguishing between flaws and tolerable anomalies. Source: Cognex Corp.
Enter Edge Learning
There’s a wide range of automotive and EV inspection challenges, and the level of complexity can help determine the best technology for the job.
Rule-based systems are inadequate for complex challenges. However, not everything necessitates the power of deep learning. For example, if you’re looking for simple patterns or trying to find a flaw along the edge of a part, those applications are consistent enough for a rule-based system. Cognex developed edge learning to balance the usability of rules-based machine vision and the dynamic power of AI.
Edge learning is a subset of AI in which processing takes place on-device, or “at the edge” of where the data originates, using a pretrained set of algorithms. The technology is simple to set up, requiring less time and as few as five images for training, compared to hundreds or thousands needed for deep learning.
Detecting defects with edge learning consists of pretraining and use-case training. The edge learning supplier conducts the first step using a large data set optimized for general industrial automation. The second step involves the customer adding several images specific to their application.
Edge learning also requires less hardware, eliminating the need for a GPU. Vision systems embedded with edge learning offer faster and simpler setup and acquisition for many applications. These smart camera platforms integrate sensors, optics, processors and illumination, reducing the complexity and cost of the system.
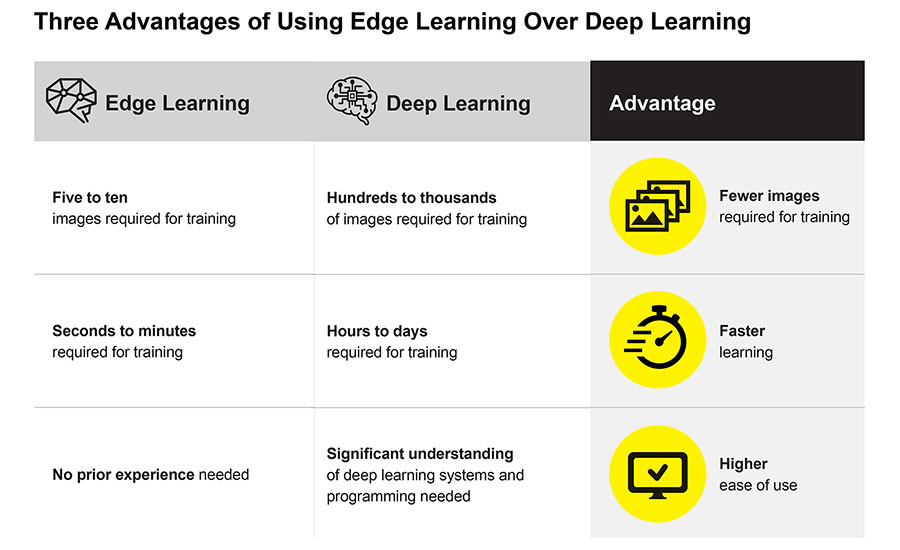
While intricate and exact defect detection tasks are more suitable for traditional deep learning methods, edge learning can handle a substantial range of applications with minimal customization requirements. Source: Cognex Corp.
When to Use Edge and Deep Learning
Complex automotive and EV applications, such as detecting flaws in electrode coating and battery cell exteriors, require more advanced technologies like deep learning. Differentiating an acceptable cosmetic blemish from a legitimate defect in high-speed environments is daunting.
The most significant difference between edge and deep learning is computational power, which can influence applications. Deep learning processes large, highly detailed image sets made up of thousands of images. The technology is a good fit for highly complex or customized applications such as electrode coating defect detection, inspecting weld seams, and battery cell surface inspections, which involve more training and have significant defect variations. Edge learning requires far fewer images and a minimal learning curve than deep learning, saving time by enabling effective assessment and inspection. The technology is particularly effective for presence and absence validation, when there are known good and bad samples or identifying a specific type of flaw. However, deep learning would be more suitable if the goal is to pinpoint precise details, such as specific lines or problems, to improve processes.
For some applications, it’s worth testing both edge and deep learning. Traditional optical character reading (OCR) algorithms struggle with reading vehicle identification numbers (VINs) and direct part marks (DPMs). Depending on the method of direct part marking, the lighting conditions, the material being inspected, and other variables, edge learning can address OCR and DPM reading with a handful of images. However, deep learning would be more effective if there are complex textures and backgrounds, inconsistent illumination, and nonuniform, poorly marked components.
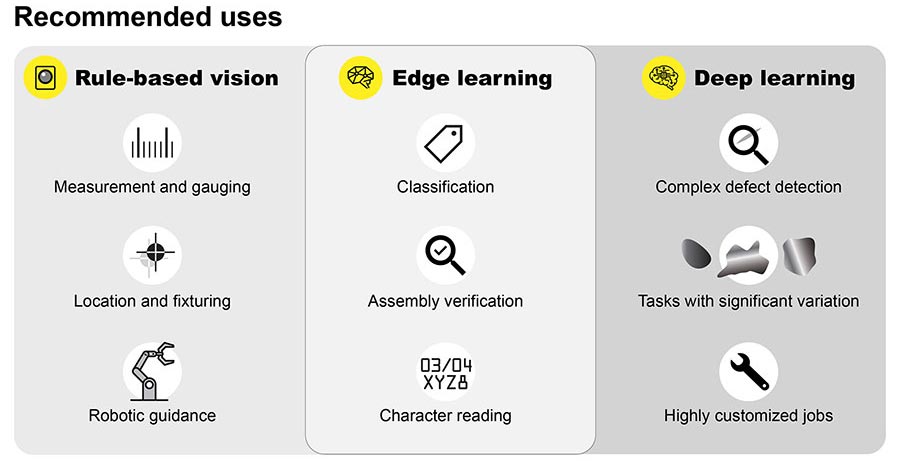
Edge learning sits between traditional rule-based machine vision and comprehensive deep learning technology, effectively catering to the requirements of applications that fall in between. Source: Cognex Corp.
Conclusion
Edge learning is a powerful and efficient machine vision technology that can tackle more complex problems than rule-based tools without the time and money required for deep learning systems. The technology offers several advantages for automotive and EV battery manufacturers, including:
- Reduced inspection time, especially compared to subjective manual inspections involving difficult choices such as identifying specific features within intricate or highly variable images.
- Lower scrap rates by separating acceptable cosmetic blemishes from functional flaws.
- Simple deployment and easy training, reducing the burden when parts or processes change and delivering ROI more quickly.
- Reduced costs by automating complex inspections.
For more information, visit www.cognex.com.
ASSEMBLY ONLINE
For more information on vision systems, read these articles:
Integrating a Vision System
Vision System is Right Inspection Tool for Leatherman
Do You Need a Color Vision System?