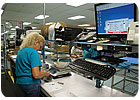
With
the push of a button, the carousel operator can retrieve the hot pick for the
waiting operator and then return to picking the batch of orders. Photo courtesy
KardexRemstar Inc.
Saia Burgess, a manufacturer of motion control components, recently implemented lean-manufacturing initiatives at the warehouse of its Vandalia, OH, manufacturing facility. The company manufactures a wide range of motion control products there, such as solenoids and switches used in ATMs, security monitoring systems, medical devices and military systems.
To keep nine manufacturing departments operating efficiently, Saia Burgess keeps more than 10,000 SKUs on hand. Until recently, the SKUs were stored on shelving. Workers had a one-to-one relationship with an order, and each worker focused on picking one order at a time.
Pick tickets were generated daily, and workers would walk throughout the shelving searching for all the parts they needed to complete the order. When the order was complete, they would deliver it to the correct department and return to the stockroom to pick the next order in the pile of pick tickets. Workers often visited fast-moving part locations several times a day, creating redundant activity.
To “lean” the order completion process, Saia Burgess has replaced the stockroom shelving with four KardexRemstar horizontal carousels that are integrated with pick-to-light technology and FastPic inventory management software. Now, 70 percent of all parts (6,800 SKUs) are stored in the new carousel system, with bulk SKUs remaining on the shelving.
Implementing the carousels has changed the way orders are processed, says Tim O’Brien, materials manager. Eight assembly department group leaders print material packets indicating the parts they require. When the material packets are printed, the order is downloaded from the Material Requirements Planning (MRP) Movex software to the FastPic inventory management software.
In addition, part orders can be entered days before the material is required. The department manager delivers the materials packet and a cart to the stockroom, indicating the order is ready to be picked.
Each order is then assigned a separate position on the batch station. The carousels rotate for the first pick, using pick lights to direct the operator to the exact location of the first pick. The operator picks the quantity indicated by the pick light and turns to the batch station to distribute the parts among the six orders as directed by the put lights.
As the operator is distributing the parts from the first pick, the other carousels are rotating to present the next pick, virtually eliminating operator dwell time. This process repeats until the six orders in the batch are filled. Each order is then placed on the cart provided by the department manager.
Any parts required for an order that are physically stored off the carousel are flagged at the beginning of the batch. Another stockroom picker will retrieve these parts from the shelving and then match them up with the orders on the department carts. All orders are filled and delivered to the correct manufacturing department within 24 hours.
The carousels also let the operator add new parts to the system on the fly. New parts are identified upon receipt, added to the FastPic software and stored in the carousels. “It’s a 30-second process to create the part number and enter in the information and set it up with the location,” says Kelly Greene, distribution business unit manager. “We can also do a mass download periodically to update any new part numbers if we would get a large amount.”
The stockroom processes an average of 220 orders per week, each averaging about eight lines per order. About 10 percent of orders are shipped directly to customers, with no value-added manufacturing required. These orders are processed in the same way; the cart is simply delivered to the shipping department for shipment directly to the customer.
Accuracy rates with the old system were below 94 percent, says Greene. Since the implementation of the carousel, the company’s accuracy is just below 99 percent.
The carousels have saved Saia Burgess 40 percent in labor. Before their implementation, the stockroom required five people to pick orders. Now it requires three people: one to pick from the carousel, one to pick from bulk storage and one to replenish the carousels on second shift.
Saia Burgess also was able to recover floor space and get their parts all back under one roof. Previously, the 7,000-square-foot onsite stockroom was over capacity, forcing slow moving items to be stored off site in a 1,600-square-foot space.
All parts are now stored onsite in a 5,000-square-foot automated stockroom, saving 42 percent floor space and eliminating a $4,000 monthly off-site storage charge. Of the 2,000 square feet that was recovered on site, a portion was used to expand manufacturing and a portion was used to expand the shipping department.
In manufacturing environments, hot picks are inevitable and occur when parts are needed in manufacturing immediately due to scrapped or lost pieces. When a manufacturing operator needs a hot pick, he fills out a materials request form and heads to the stockroom. With the push of a button, the carousel operator can interrupt the batch orders being picked, retrieve the hot pick for the waiting operator, and then return to picking the batch of orders.
For information about automated storage and retrieval systems, visit www.KardexRemstar.com. or call 800-639-5805.