Most kaizens, or changes that promote continuous improvement, are small, but together, they can have a significant cumulative effect. Occasionally, though, a low-cost change comes along that generates massive savings. At Toyota Motor Corp.’s assembly plant in Buffalo, WV, the manufacturing team came up with just such an extraordinary innovation.
Toyota Motor Manufacturing West Virginia Inc. (TMMWV) is the carmaker’s only combined engine and transmission plant in North America. Additionally, TMMWV is the only manufacturing plant in North America to produce hybrid transaxles.
Approximately 2,400 people work at the $1.8 billion factory, which spans nearly 2 million square feet. TMMWV, which celebrated its 25th anniversary in 2021, produces some 1 million engines and transmissions annually.
A key component of any engine is the camshaft, which must be machined to very tight tolerances to function properly. If the camshaft’s lobes aren’t spot on, it can result in unacceptable chatter noise when the completed engine is powered up. At that point, the only way to fix the problem is to shut down the production line, deconstruct the affected engines and replace the faulty camshafts.
“Just one failed test can cause a quarter of production—or about 135 engines—to be placed on hold,” says Cheryl Rollins, team leader in quality control at the plant. “That almost always requires scheduling weekend work to fix the problem.”
To prevent that from happening, Rollins and her team set out to come up with a way to identify cam chatter earlier in the production process.
The Kaizen
By applying Toyota Production System principles, the team drilled down to the root cause of the problem and came up with an elegant and affordable camshaft chatter checker tool. It’s comprised of an LED stream light, a small white board, and a bit of nylon to hold it all together at the required angles. The worker conducting the inspection simply aligns the tool with the camshaft, turns on the LED and examines the pattern that appears on the whiteboard when the light reflects off a specific lobe.
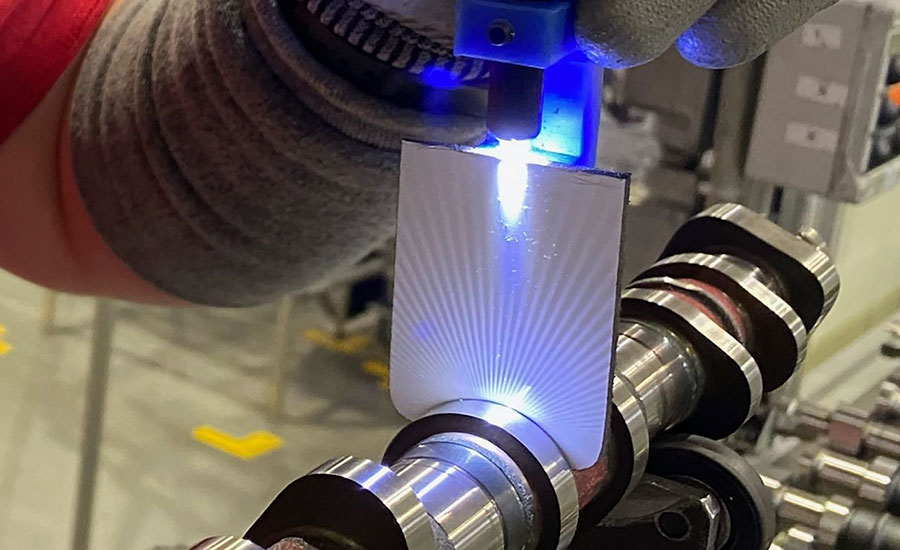
Engineers at Toyota have invented an elegant and affordable tool for inspecting camshafts. It’s comprised of an LED stream light, a small white board, and a bit of nylon to hold it all together at the required angles. Photo courtesy Toyota Motor Corp.
If all is well, the light will bounce off the lobe and onto the white board in one continuous flood of light. But if there are imperfections in the machined surface, a radial pattern of shadows will appear on the board—what the team refers to as “fanning.” The more prominent the shadows, the more significant the flaws. And, in turn, the louder the resulting engine noise if that camshaft were to find its way into production.
Workers don’t check every camshaft, only a representative sample. But since the checker has been put into use, the plant hasn’t had a single shutdown requiring extra work shifts due to this problem. All of the flawed components have been identified and replaced earlier in the production process.
The Savings
In hard costs, Rollins says the impact of an assembly line shutdown due to cam chatter was in the neighborhood of $500,000 per incident. Even if the cam chatter checker has prevented just one such occurrence, it has already paid for itself many times over. And that’s before factoring in the impact such disruptions can have on the lives and morale of the workers directly affected by it or the delayed production of engines that are in such high demand right now.
Meanwhile, Rollins and her team applied for and were granted a patent for their invention. And their colleagues at Toyota’s assembly plant in Huntsville, AL, which churns out 3,000 engines per day, have also incorporated the innovation into its quality control processes.
“The loss of containment used to cause a lot of frustration on the line,” Rollins says. “They came to us and said, ‘Please come up with something.’ It’s incredibly satisfying to respond to the challenge and to receive the validation of the patent, which, as far as we know, is the only one of its kind in the U.S. It really makes you proud to work for a company like Toyota.”
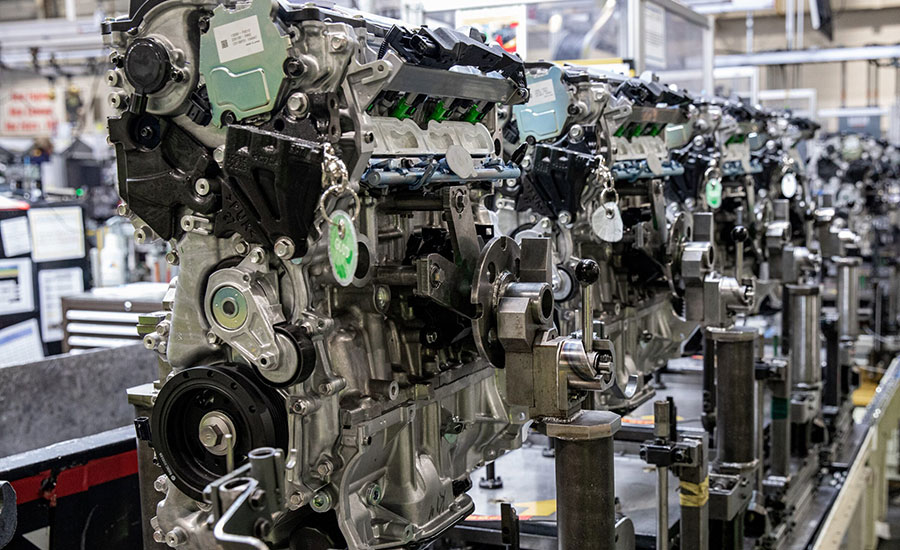
Toyota’s assembly plant in Buffalo, WV, produces some 1 million engines and transmissions annually. Photo courtesy Toyota Motor Corp.
ASSEMBLY ONLINE
For more information on Toyota, read these articles:
Toyota Improves Engine Assembly
The Toyota Production System: A Fresh Look
Toyota Unveils New Generative AI Technique for Vehicle Design