“If you build it, [they] will come” is a famous line from the film Field of Dreams. Although it refers to baseball, the same line applies to EV chargers.
Electric vehicles need conveniently located charging stations. To meet growing demand, many factories have recently opened in Europe and North America to mass-produce chargers and other types of high-voltage equipment.
Despite numerous advantages, EVs are not perfect. Operating a battery-powered car takes a bit of getting used to, especially when it comes to public “refueling.” Motorists are currently tasked with considering destination charging and planning routes around where rapid chargers are located.
To meet the demand, suppliers of public and business chargers have stepped up, albeit with regional variations. According to data compiled by Statista, by the end of 2022, China boasted 1 million slow chargers and 760,000 rapid units. The United States, meanwhile, ranked third with 100,000 slow chargers and 28,000 rapids. In Europe, where 70 percent of EV charging occurs at home or at work, there are half a million charging points, the vast majority being slow chargers.
However, those numbers will be high for 2023, because of continuous growth. The technical capabilities of chargers are also improving steadily as manufacturers ramp up production.
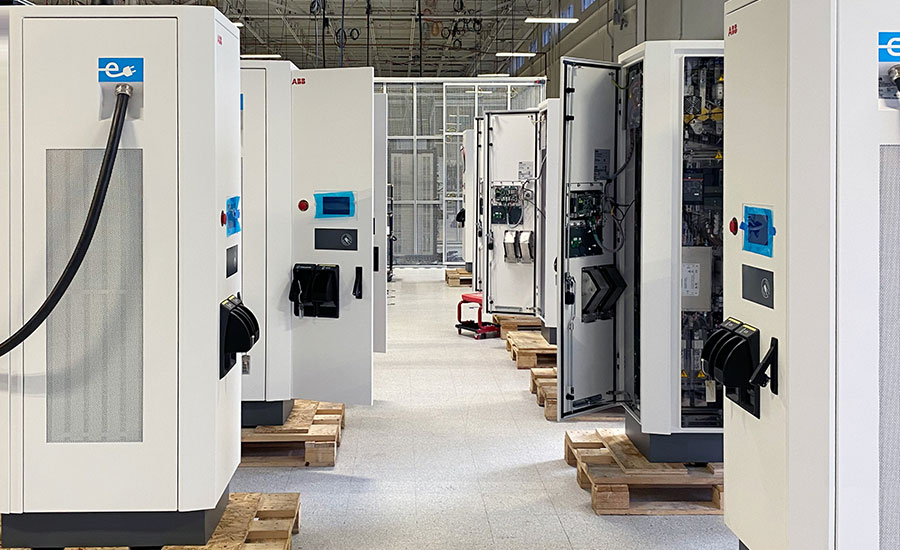
ABB E-Mobility is assembly EV chargers at a new factory in Columbia, SC. Photo courtesy ABB E-Mobility
Charger Manufacturing Ramps Up
There is no shortage of companies getting in on the EV charging act. Last month, LG Electronics opened a new factory in Fort Worth, TX, that is assembling Level 2 and 3 chargers. The devices are designed to be owner-operated, meaning business and municipalities can set their own rates and keep all revenue that’s generated.
ABB E-Mobility is the first charger manufacturer to earn certification from the National Type Evaluation Program (NTEP) and the California Type Evaluation Program (CTEP) for DC fast chargers. These certifications mean that the chargers have been tested in approved laboratory conditions for compliance with the National Institute of Standards and Technology Handbook 44 (HB 44).
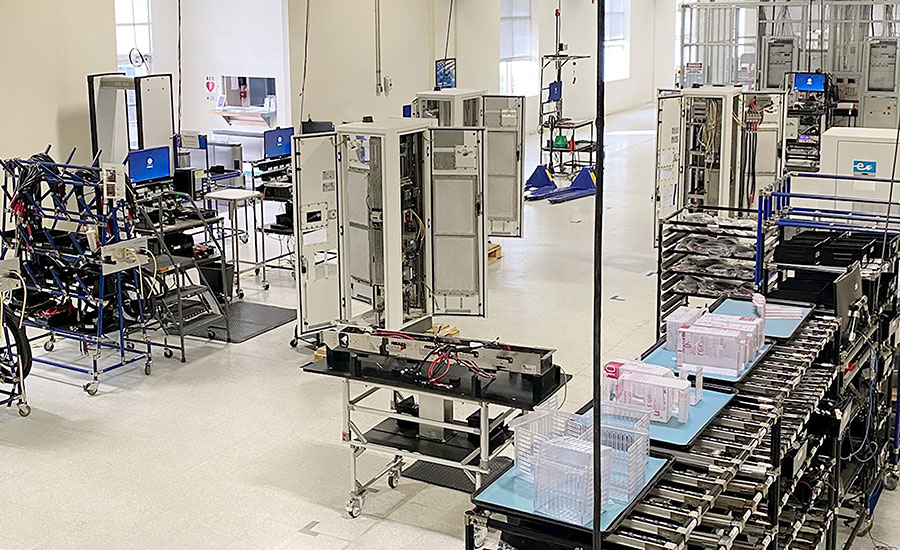
Many companies are building plants to keep up with growing demand for commercial charging equipment. Photo courtesy ABB E-Mobility
The certifications cover the company’s Terra 124 and Terra 184 chargers, which have been manufactured since last year at ABB E-Mobility’s assembly plant in Columbia, SC. At the start of production, the goal was to reduce lead times on charging units to meet the demand from drivers, with chargers ranging from 20 to 180 kilowatts (kW) DC. The latter output refers to the Terra 184, which the company expects to become a familiar site on U.S. highways for standard and heavy-duty vehicle applications.
“This manufacturing milestone demonstrates [our] leadership in the energy transition to electrification and [our] ability to build the e-mobility economy in the United States,” says Bob Stojanovic, vice president for ABB E-mobility in North America. “The need to expand U.S. charging infrastructure is immediate, and we have prioritized our business to support our customers and the industry as a whole.”
Last summer, South Korea-based EV charger manufacturer SK Signet opened the doors to its new production facility in Plano, TX. The factory has a maximum capacity of 10,000 ultra-fast chargers a year and will lead to the creation of more than 180 jobs.
The site will be responsible for the production of SK Signet’s V2 charger, which provides a maximum power output of 400 kW and the ability to charge vehicles up to 80 percent in as little as 15 minutes.
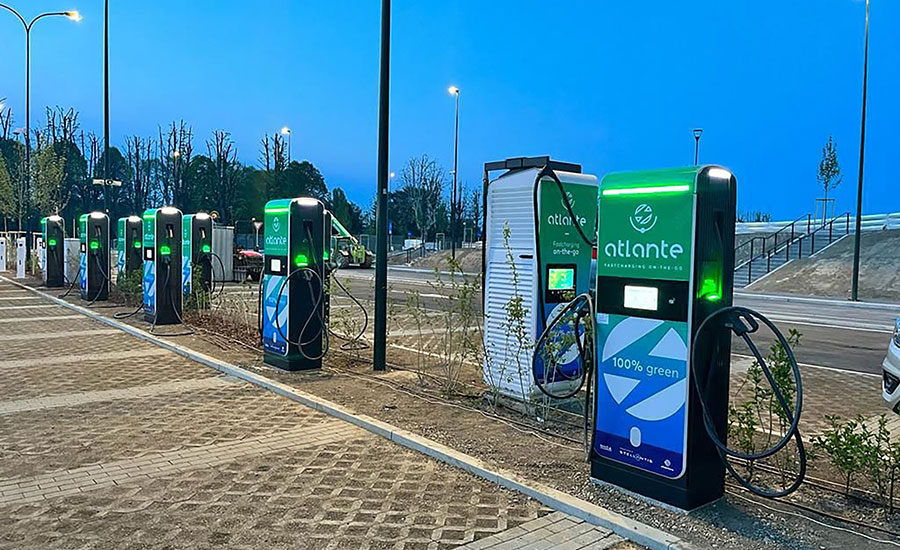
Many companies are building plants to keep up with growing demand for commercial charging equipment. Photo courtesy ABB E-Mobility
Rapid Expansion
Wallbox has been steadily growing since it was established a decade ago in a small warehouse in Barcelona, Spain. Today, the company has commercial chargers in more than 80 countries. It continues to refine its energy management technologies and charging systems to meet clean energy use requirements and customer demands.
“One of the main trends in EV charging is a focus on improving the user experience, which can be broken down into three parts: reliability, accessibility and usability,” says Erik Fogelberg, general manager at Wallbox USA Inc. "Reliability is about maximizing the uptime of EV chargers, and diagnosing and resolving any issues as quickly as possible.
“Accessibility and usability are the parts that are more interesting to end users,” claims Fogelberg. “Recently, we have seen more EV chargers equipped with point-of-sale terminals and credit card readers, which will continue to improve accessibility and usability.”
The next evolution will be a “plug and charge” approach. “With [that system], drivers simply plug into the charger and the rest of the transaction process will occur automatically, without any further interaction with the charger, for an almost seamless experience,” explains Fogelberg.
The next public charger produced by Wallbox will be the Supernova, a DC unit specifically designed for public spaces in North America. The product has already been successful in Europe, where more than 2,000 units have been sold. Later this year, Wallbox will also be launching its Pulsar Pro charger in North America. The device is specifically designed for shared spaces, such as shopping mall or office parking lots.
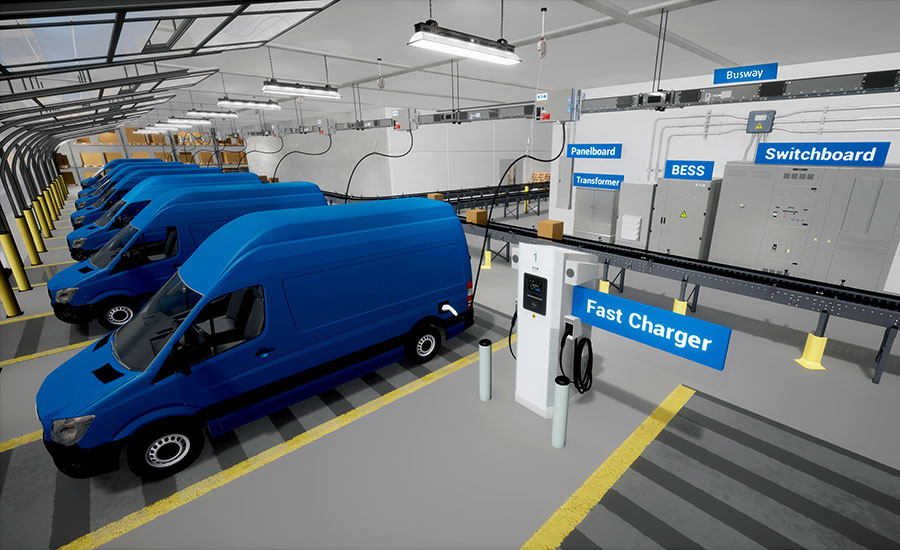
Charging busways will help accelerate fleet electrification. Illustration courtesy Eaton Corp.
“We are committed to providing the best possible charging experience for our customers,” says Fogelberg. “One way we achieve this is by offering EV charging cables that provide an optimal balance between performance and weight. Our DC fast chargers are made with materials that provide IK10 impact protection while remaining lightweight, making it easier to transport and install our chargers.
“We are constantly working on new initiatives in both hardware and software to improve our products and services,” adds Fogelberg. “However, three of the major commonalities that we never lose focus on are design, performance and user experience.”
To meet growing demand for new chargers, Wallbox operates several factories to serve different markets.
“All the [facilities] are specifically designed to be able to easily increase capacity by introducing new assembly lines, on a needs basis,” explains Fogelberg. “In the past two years we have invested in two new factories: one in Barcelona, and another Arlington, TX, that produces products specifically for North America." Wallbox also recently acquired ABL, which has added two new factories in Germany and Morocco.
“We utilize human-machine interface (HMI) technology for our assembly processes,” says Fogelberg. “This guides operators to ensure the accurate assembly of the chargers. We also incorporate quality checks during the assembly process to monitor things such as torque control and wiring harness installation. In the unlikely event of an issue, it ensures early detection and resolution.
“It’s more efficient for us to run [manual] assembly lines [rather than] fully automated lines,” adds Fogelberg. “However], we run automatic end-of-line tests, which allows the functionality and visual aspects for every charger that leaves the factory to be checked and verified.
“As the EV industry is rapidly evolving, regulations and needs will continue to change,” Fogelberg points out. “The market will benefit from further government investment, to the benefit for the EV-driving public.
“Charge point operators will not only be looking for DC fast chargers, but also long-term solutions,” claims Fogelberg. “That means they want reliable chargers with a proven track record that are cost effective to install and maintain. They also want to offer their customers a seamless payment experience in products that are upgradable so that as next-generation EVs hit the market, they can increase the power capability of their chargers.”
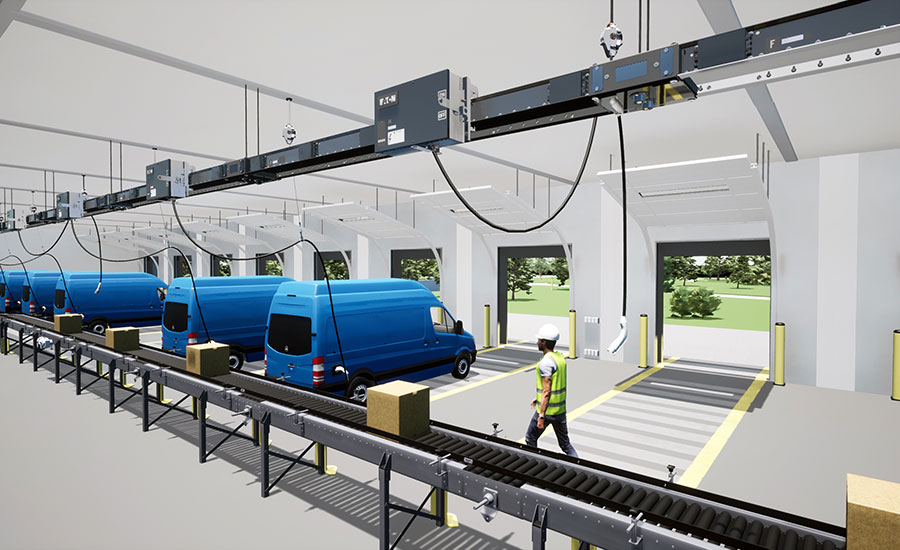
Modular, overhead charging technology eliminates costly cable runs and major modifications to existing parking structures. Illustration courtesy Eaton Corp.
Old Company, New Focus
For legacy automotive suppliers, the emergence of battery technology has meant a shift in focus on products, production and planning. A good example is Eaton Corp., which has used its electrical engineering expertise to grow into the EV space.
“We’re delivering breakout capabilities in EV hardware and software that adhere to open standards and enable infrastructure that’s scalable and built to last,” says Joe Cappeta, director of technical applications and energy transition at Eaton.
One of the most recent innovations at the 113-year-old company is its EV charging busway, which claims to accelerate fleet electrification and reduce installation time by 40 percent. The product is assembled at a three-year-old factory in Hodges, SC.
“The modular, overhead charging technology eliminates costly cable runs and major modifications to existing parking and conveyor structures,” explains Cappeta. “The busway enables [companies] to expand and reconfigure infrastructure with no concrete work required, which is often the biggest cost when deploying EV charging for fleets. We’re providing a plug-and-play solution to add, move and expand charging infrastructure without rewiring.”
Eaton’s Fleet Pro charge was developed with in-line fusing “above and beyond UL standards,” enabling it to be applied anywhere within the power system safely.
“Our Charging Network Manager software makes it easy to deploy, manage and monetize charging infrastructure for fleet, commercial and multi-family applications,” claims Cappeta. “The dashboard has been designed for enabling customers to oversee charging locations; supporting driver access and control; monetizing charging infrastructure; and reducing costs with load management.”
According to Cappeta, the next 18 months is going to see continued change and development of the charging infrastructure and network. “Vehicle electrification is no longer a pilot program or experiment,” he points out.
“Critical power is what we deliver on for our customers, so reliability is extremely important,” notes Cappeta. “While hardware can experience problems, it’s essential to have the personnel and the expertise required to troubleshoot a system and get it back up and running in an emergency.
“We’re also adding intelligence into our chargers and battery energy storage systems with Predict Pulse remote monitoring and management service,” says Cappeta. “This technology actively monitors over 200 data points within hardware to predict and mitigate a potential failure before it happens.”