AGCO Corp’s assembly plant in Jackson, MN, has gone green. The 2017 Assembly Plant of the Year no longer makes red and yellow tractors. Today, the color palette inside the factory has changed to green. That’s because the main vehicles assembled at the 59-year-old facility are Fendt tractors.
In 1997, AGCO acquired Fendt, a leading European agricultural equipment firm based in Germany that’s known for its innovative technology, such as continuously variable transmissions, and its distinctive Nature Green livery. Fendt is now AGCO’s premier tractor line.
“There have been numerous product launches and changes in branding since 2017,” says Travis Van Genderen, director of Jackson operations. “We no longer make yellow Challenger and red Massey Ferguson tractors in Jackson. Today, we only assemble tracked tractors.”
That’s a big difference. Back in 2017, most machine built in the factory used big tires. But, a flexible assembly line enabled operators to switch back and forth between tires and tracks. Because no two machines on the line were ever alike, it was not unusual for assemblers to build a Challenger tractor on four wheels, followed by a Challenger on tracks and then a Massey Ferguson with a dual set of rear tires for extra traction. Most of the variability in the plant today involves factors such as track type, track width and track spacing.
“Five years ago, AGCO began investing heavily in its Fendt brand in North America,” explains Van Genderen. “Starting in 2020, we transitioned our factory in Jackson to be the local face of Fendt. However, we only focus on tracked tractors. Wheeled models are made at Fendt’s flagship plant in Marktoberdorf, Germany.
“Our Jackson-built tractors are now made on Fendt power trains and module platforms, including a small frame machine and a large frame model,” Van Genderen points out. “Within each platform, we make various models that are based on engine power. Those products include the Fendt 900 and the 1100 Vario MT.
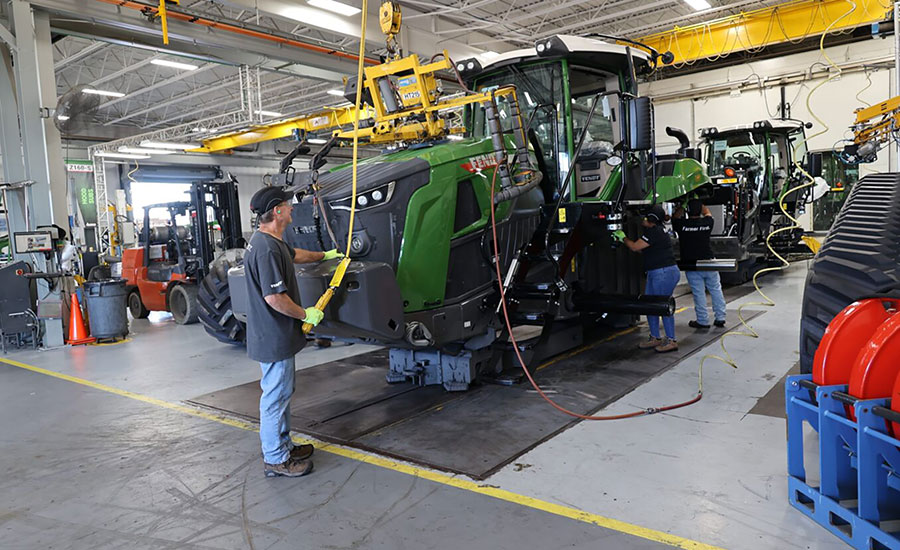
All tractors on the Jackson assembly line are now painted green and equipped with tracks. Photo courtesy AGCO Corp.
“In 2022, we launched the Fendt Rogator 900, the world’s first self-propelled row-crop sprayer that features adjustable height,” says Van Genderen. “The entire suspension system on the four-wheeled machine raises and lowers based on the crop height. Because the product is revolutionary, we had to make a lot of changes in our assembly line to accommodate it.
“We are not doing anything with fuel cell- or battery-powered tractors, because we only build high-horsepower machines in Jackson,” adds Van Genderen. “However, other AGCO facilities in Europe are making some smaller tractors that are equipped with alternative power trains.”
The only legacy product still built in Jackson is the three-wheeled TerraGator applicator. It’s also the only machine in the plant that is not painted green; it still sports a traditional coat of yellow.
“We’ve gone through a lot of changes here, but not as much on the manufacturing side of operations,” explains Van Genderen. “We have not made any major changes to our production line. However, we did upgrade some test equipment and subassembly manufacturing processes.”
The Jackson facility has invested in its tube fabrication department, which produces large steel booms for the Rogator. The extendable booms come in 90-, 100- and 120-foot lengths with 10-, 15- and 20-inch nozzle spacing to suit specific width, volume and broadcast needs of farmers.
“We recently purchased a state-of-the-art laser welding and material handling system, including an advanced robotic cell,” says Van Genderen. “That has enabled us to vertically integrate more tubing production in-house.
“We have also started to use collaborative robots in our welding department,” notes Van Genderen. “We use them for machine tending and small part welding applications. We currently have two cobots in use.
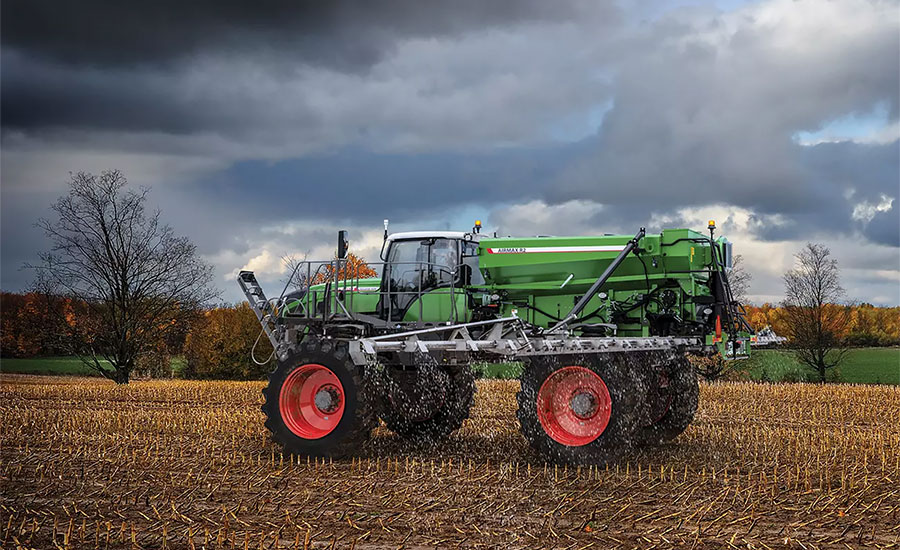
This row crop sprayer features a height-adjustable suspension system. Photo courtesy AGCO Corp.
“In addition, we’re expanding our use of autonomous mobile robots (AMRs),” explains Van Genderen. “In 2017, we were using automated guided vehicles to deliver kit parts to our tractor assembly line. We’ve since upgraded the system to AMRs that use visual guidance technology rather than in-floor magnets. We’ve also expanded the application to our sprayer assembly line.
“We are still transitioning away from using air-powered tools on our assembly lines,” says Van Genderen. “We’ve made some definite progress, but we still have a way to go. For some applications, we just haven’t found a good alternative yet.”
Since 2017, Van Genderen and his management team have focused a lot of their attention on improving shop floor culture to drive operational efficiency, productivity and quality. They’re using the Shingo model and benchmarking with other manufacturers. In fact, earlier this year the Jackson plant hosted a workshop that attracted participants from three other companies.
“To develop our workforce, we have invested a lot in bilingual and non-English speaking employees,” says Van Genderen. “Up until 2021, we had a strict policy that required all job candidates to be fluent in English. However, that limited us in attracting talent. Starting in 2022, we changed that approach and made a concerted effort to recruit a more diverse workforce.
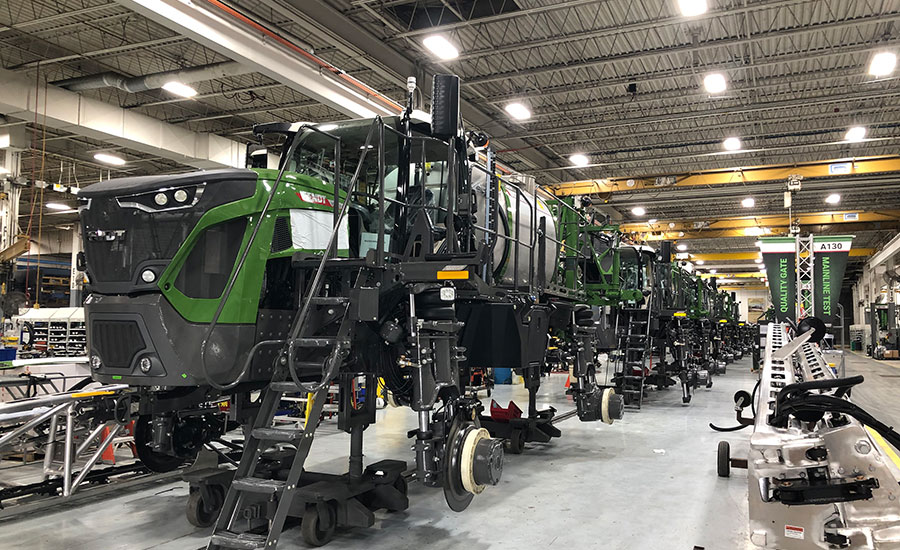
To address ergonomic concerns, such as strains, pains or exertion issues, the Jackson plant employs a part-time chiropractor and a full-time physical therapist. Photo courtesy AGCO Corp.
“So far, the initiative has been very successful,” claims Van Genderen. “We have hired a large number of Spanish-speaking employees. But, we had to develop and build systems to support that shift in direction. Our bilingual efforts have included translation, training and mentorship programs.”
To address ergonomic concerns, such as strains, pains or exertion issues, the plant still employs a part-time chiropractor and a full-time physical therapist. Within the last two years, it has also added two part-time behavioral health specialists to address mental well-being.
In 2017, AGCO’s Jackson facility was in the midst of an innovative project that equipped assemblers with wearable devices. It referred to the Google Glass-based program as “informed reality.” While the initial results were encouraging, the initiative has since been shelved for a variety of reasons.
“Starting in 2021, we transitioned our entire business system over to SAP,” says Van Genderen. “With that, we launched an in-house developed manufacturing execution system. Deploying a new ERP and MES at the same time was a big shift for us. When we launched those systems, we lost some connectivity with the wearable devices.
“We also discovered that wearable technology wasn’t the best option for us in all applications,” explains Van Genderen. “In addition, Google no longer supports the glasses.
“After we got into full-scale deployment, we ran into a lot of technical challenges,” recalls Van Genderen. “The return on investment wasn’t quite as much as we had hoped for.
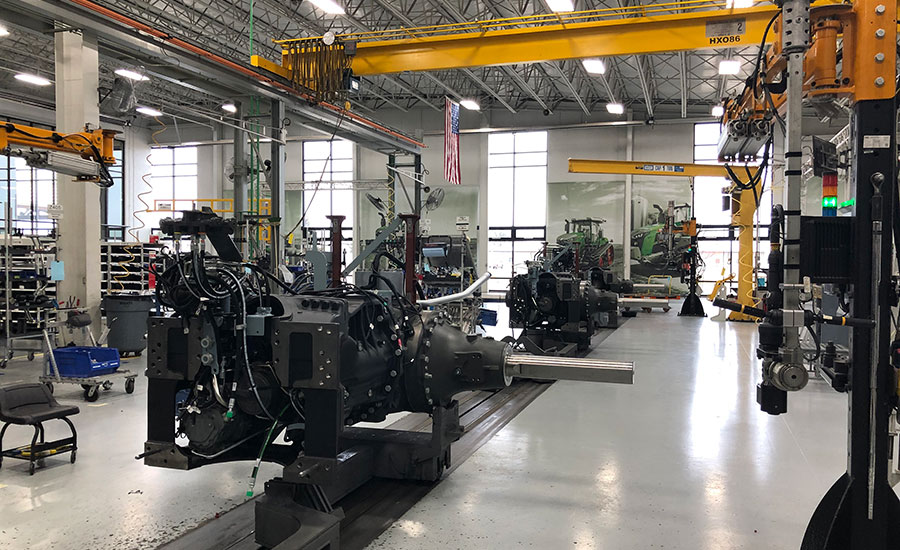
All Jackson-built tractors are now made on Fendt power trains and module platforms. Photo courtesy AGCO Corp.
“We had some great use cases for the wearable technology and there were pockets where it really was effective,” says Van Genderen. “But, wide-scale adoption of the technology just wasn’t feasible. There were areas where the glasses worked OK, but some work instructions were granular and difficult to view. So, it wasn’t as effective at training new employees as we thought it would be.
“We needed to transition to a technology that was more robust and could provide a better viewing experience for users, so we opted to move toward tablets,” notes Van Genderen. “The tablets are a more effective way for operators to view instructions, zoom in and see a more complete assembly picture.
"They tend to provide a better viewing experience for operators, especially when it comes to communicating complex work instructions,” claims Van Genderen.
AGCO Jackson has, however, had success with additive manufacturing technology. The plant launched an initiative in 2022 that now uses a dedicated cell equipped with a multi-jet fusion (MJF) printer by HP, fused deposition modeling printers by Stratasys and Raise3D, and stereolithography resin printers by Formlabs. Its sister factory in Beauvais, France, is also very advanced in using the technology.
“We are printing production-ready parts, in addition to fixtures and assembly aids used in our factory,” says Van Genderen. “It’s been very effective for us and the parts look phenomenal. Our design engineers are also using additive manufacturing to create new parts. For instance, they’re looking at ways to combine three or four parts and consolidate them into one complex part that normal manufacturing processes can’t support.”
Engineers can produce a variety of plastic parts that fit within a 16-inch cube. Production parts currently being printed include an adaptor for air filters and hoses, brackets for lights and reflectors, a handle for air valves, a plug for floor mats, and support brackets for hoses and dipstick tubes.
“Currently, 13 production part numbers are being produced on the MJF printer,” says Van Genderen. “We plan to grow this to 50 part numbers.”Click here to learn more about the Assembly Plant of the Year award or to nominate a facility for 2024 (the deadline is May 1).