Located in Lyons, OR, about 60 miles due south of Portland, Freres Engineered Wood is a family-run business that has been making sustainable wooden building products since 1922.
Following the Oregon Forest Practices Act, the company uses scientifically supported methods to sustainably harvest and replant the Douglas Fir trees on 17,000 acres of timberland. The company is among the most responsible forest stewards in the country, earning certification from the American Tree Farm System, as well as the support of many loyal customers and surrounding communities.
Freres Engineered Wood produces Mass Ply Panel, a wood-based structural panel used as an alternative for concrete and steel in multistory construction projects. This sustainable building material has been used in Europe for decades and is now growing in popularity in the U.S.
“The environmental attributes of wood products are second to none,” says Kyle Freres, vice president of operations at Freres. “Wood is a naturally carbon-sequestering solar product that we can use to make one of the most advanced building products on the planet.”
Mass Ply is Freres’ proprietary version of a mass timber product, similar to cross-laminated timber, a lumber-based panel. Freres’ panel is veneer based and is formed by peeling a log into 0.125-inch thick sheets of veneer. Those sheets of veneer are then assembled into 1-inch-thick pieces that are used to construct a larger panel. Some of these panels can be up to 12 feet wide and 48 feet long, with thicknesses up to 12 inches. These strong panels can be used for floors and roofs in commercial construction.
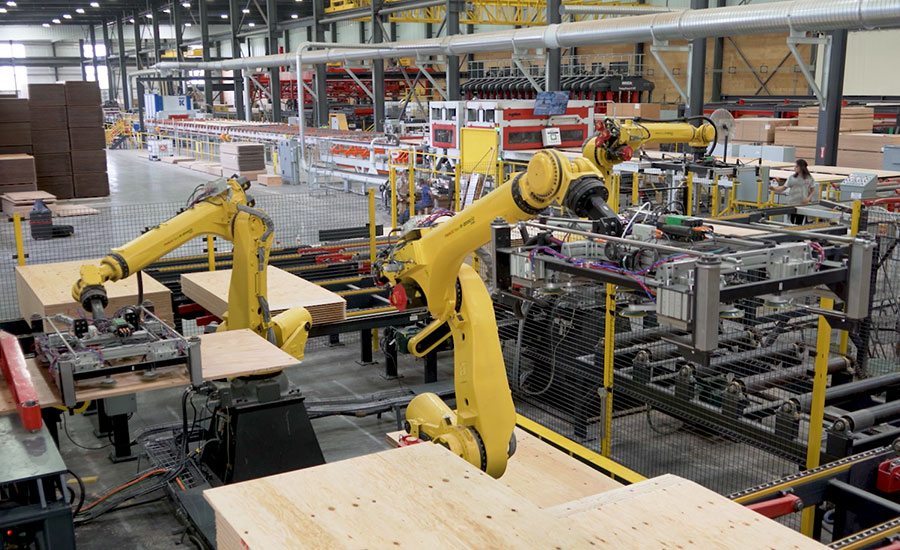
Combining a 3,100-millimeter reach with a 210-kilogram payload capacity, the R-2000iC/210L robot is a great choice for tasks involving high payloads. Photo courtesy FANUC America Corp.
Automation for Large Panels
A few years ago, Freres began designing a new production line in a new facility to create larger panels out of smaller pieces of wood. For this process, a scarf joint must be cut into the panels.
“Unfortunately, the equipment that we were using initially didn’t have the tolerances or the consistency that we were looking for,” says Freres.
Since both ends of the panel were being cut independently by different cutting heads at the same time, matching the cut to both ends of the panel was difficult. Additionally, panels were often bowed or cupped, which adversely affected the profile of the scarf joint. Finally, panel vibration could not be adequately controlled, potentially causing the cutting heads to remove extra wood from the panel edge, which subsequently compromised joint performance.
Freres wanted to boost production efficiency and improve the quality of their panels via better joints, which is key to the panels’ strength. The company turned to FANUC authorized system integrator PRE-TEC, which has been involved in many wood processing automation projects.
Based in Eugene, OR, PRE-TEC designed a robotic cell using two FANUC R-2000iC/210L six-axis robots. Combining a 3,100-millimeter reach with a 210-kilogram payload capacity, the R-2000iC/210L robot is a great choice for tasks involving high payloads. The robot can carry 25 more kilograms than its predecessor, the R-2000iB/185L, and it offers better rigidity, wrist load moment and inertia. Its relatively small footprint means it easily fits into crowded factory environments. It provides a positional repeatability of 0.05 millimeter.
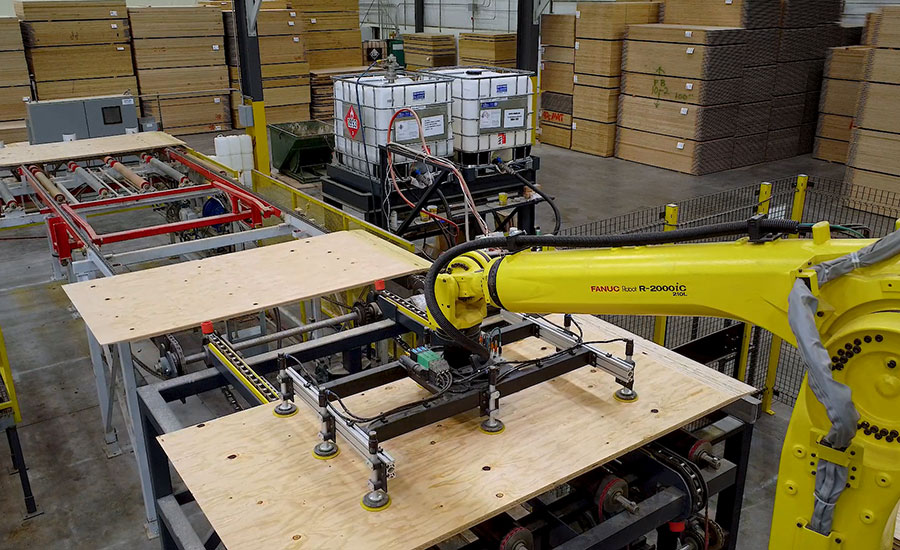
Before presenting the panel to the cutting head, the EOAT squares and clamps the panel. An on-board thickness measurement system ensures the panel is within a target thickness range. Photo courtesy FANUC America Corp.
At Frere, panel units are fed into the system in two locations—one for each robot presenting panels to the cutting system. Each robot picks and lifts an engineered wood panel with a specially designed end-of-arm tool (EOAT).
“The end-of-arm tool will vacuum pick the plywood panel that’s going to be scarfed,” says Mark Matteson, sales and marketing operations analyst at PRE-TEC.
Before presenting the panel to the cutting head, the EOAT squares and clamps the panel. An on-board thickness measurement system ensures the panel is within a target thickness range. If it is not, the robot places the panel on a reject conveyor to be double-checked by plant personnel.
If it meets thickness requirements, one end of the panel is inserted between a hold-down mechanism and an anvil. Once the panel is in the desired position, the clamping mechanism activates, holding the panel down against a machined surface to reduce vibration and effects of cupping in the wood on joint quality. When the cutting cycle is complete, the robot flips the panel over to present the other end.
“The benefit there is that we’re having the same cutting head cut both sides of the panel, so we know we have a balanced scarf joint on both ends of our panel,” says Freres. “We could not do that without having a robotic application.”

With a relatively small footprint, the R-2000iC/210L easily fits into crowded factory environments. Photo courtesy FANUC America Corp.
Meanwhile, as the first panel is being cut, the second robot goes through the same picking, squaring and thickness checks before staging a second panel below the one being cut.
This system has significantly improved the quality of the panels’ joints, which benefits their strength and performance. Moreover, the automated cutting system has doubled production capacity, because two robots now continually feed the same cutting head. This helps optimize the manpower and floor equipment to support growth in future demand.
“We’re using two robots in a very tight space to work together, without collisions, to fully utilize a cutting head system,” he says. “With the FANUC robots, you can really control the scarf-cutting process to make sure that we are within tolerances.”
Not only is the robotic system increasing quality and throughput, but it’s also freeing up hard-to-find employees to do other higher-level jobs and tasks.
“It’s a lot less manual labor for our employees,” Freres says. “It’s an easier process for them to manage.”
With sustainable construction products becoming more attractive due to increasing concerns over climate change, products like Mass Ply Panels are poised to surge in popularity. The automation at Freres has helped ramp up production capacity and improved the panels’ quality for future demand.
“We’re looking at technology and robotics as a way to support the innovation that our industry and our company, in particular, need to survive for another hundred years,” says Freres.
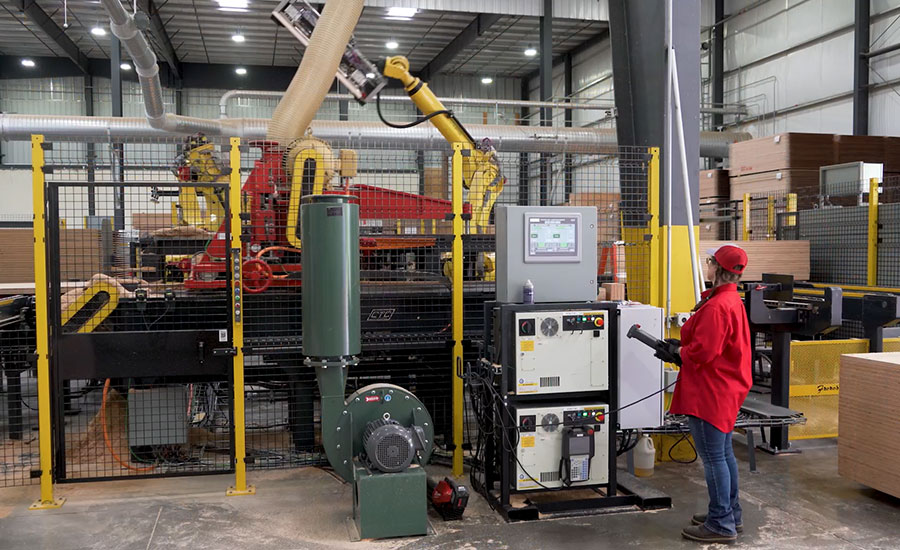
The robotic system has reduced the amount of manual labor for Frere’s employees. Photo courtesy FANUC America Corp.
ASSEMBLY ONLINE
For more information on robotic assembly, read these articles:
Robots Assemble Drivetrain Components
What’s New With Robotic Soldering?
Six-Axis Robots Provide Ultimate Flexibility