Despite the benefits of automation, a wide range of manufacturing processes still demand the flexibility that can only be supplied by skilled production workers. But, just like with automation systems, manual assembly operations must leverage the latest technologies to provide the precise, repeatable performance that is crucial for productivity and quality.
Intelligent cordless fastening tools are one such technology. These products incorporate features—such as integrating the controller directly into the tool—to improve ergonomics and measure the torque and angle applied to every fastener. The result is correct assembly of every component, while providing full traceability.
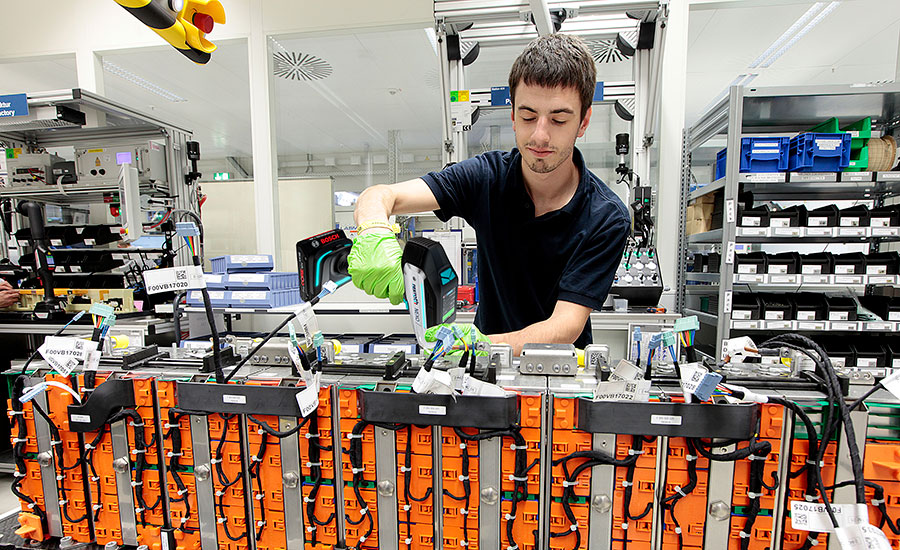
The Nexo cordless nutrunner can safely be used for assembling EV battery packs. Photo courtesy Bosch Rexroth Corp.
Manual Assembly Provides Flexibility
Many companies, including manufacturers of medical devices, electronics, appliances, furniture and electric vehicle batteries, have factories that combine highly automated lines with versatile, manual assembly systems.
Full-scale automation systems can be expensive and time-consuming to design, engineer and install. With manual assembly, skilled assemblers can carry out complex steps, such as installing headlights or seats in a car, that would be difficult for a robot to perform.
In addition, many industries have well-established manual assembly lines that have been honed over many years to eliminate waste. Those measures would be difficult to replace with automation.
Manual assembly is effective for products that have smaller production runs—thousands of units instead of millions—and for products with a high number of variations. Experienced workers, supported by digital assembly guides, are more agile and responsive to variations, whereas an automated system would require extra programming and changeover.
People are also literally more flexible than machines. For example, if a part must be installed on the underside of a vehicle, or electronic components must be connected inside a server cabinet, a person can do the job much more quickly and easily than a robot.
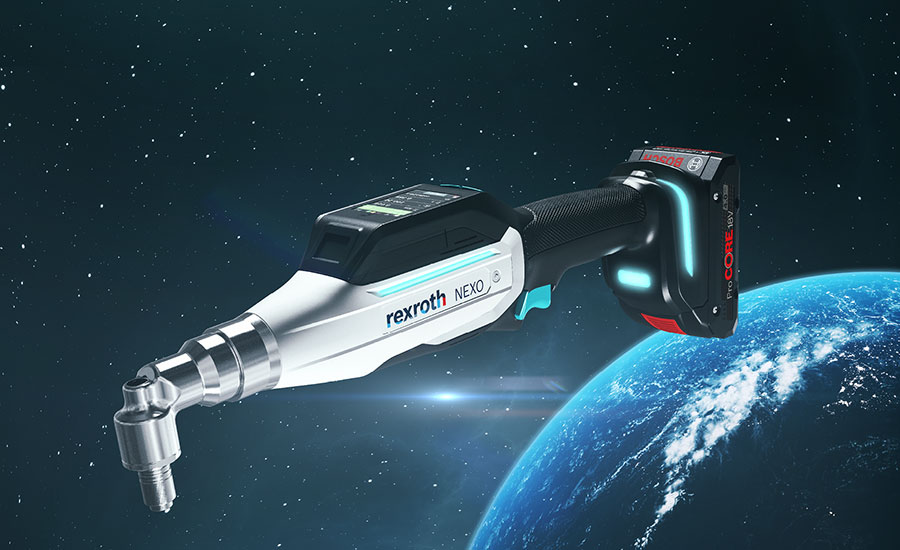
The Nexo nutrunner is lightweight and ergonomic. Photo courtesy Bosch Rexroth Corp.
“Handheld Automation”
Manual assembly can only be effective if it is as tightly controlled as automated manufacturing systems. The newest generation of high-performance, cordless fastening tools combines ease of use, ergonomic design and sophisticated digital intelligence to enable full-featured, “handheld automation” in manual assembly processes.
Such tools offer advanced capabilities, including:
- Tightening a threaded fastener to defined parameters.
- Automatically inspecting each operation via built-in sensors calibrated to national standards.
- Digitally documenting every fastening operation.
- Alerting the assembler if an error or deviation has occurred, enabling prompt remediation.
Intelligent tools provide the real-time data collection, quality monitoring, and precise, reliable, repeatable performance of Industry 4.0 technology, along with the flexibility of manual production.
This is important if the assembly process involves significant variability, such as connecting power management controls to an EV battery pack. Having a skilled assembler handle the task offers the optimum combination of precision tightening and tracking with a person’s ability to respond to individual complications as work progresses.
Intelligent cordless tools can also be configured to provide increased safety protection for assemblers and the products they work on. EV battery packs are a major example. These packs must be assembled while the batteries are live. Because assembly errors can pose a risk to workers’ health and the proper functioning of the vehicle and its safety system, there are strict requirements for monitoring and documenting every connection. In accordance with VDI/VDE standard 2862, suppliers and OEMs must monitor every safety-critical tightening connection and archive the documented data for 10 years.
And, because they’re cordless, intelligent tools provide ergonomic and safety benefits. Power cords are a tripping hazard and pose a risk of electrical shock. Cords can also mar painted surfaces. Intelligent cordless tools can be configured to record and transmit fastening data wirelessly.
Key Characteristics
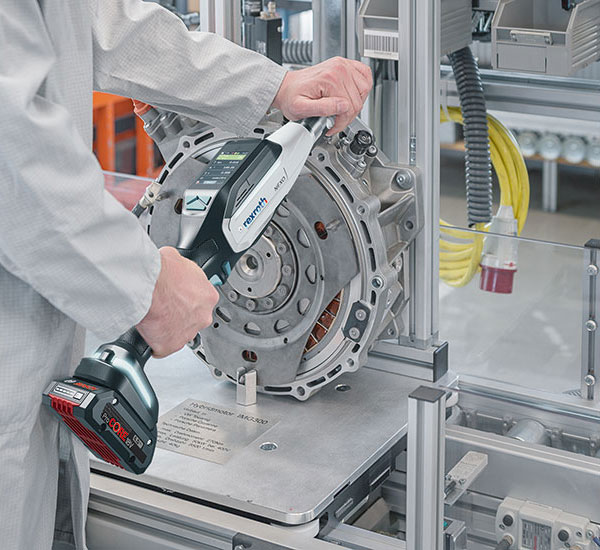
Bosch offers four battery sizes, giving manufacturers the ability to use a heavier battery with a longer runtime or a lighter one to make it easier on workers. Photo courtesy Bosch Rexroth Corp.
To realize the potential for handheld automation, engineers should look for tools with the following features:
Powerful integrated controller. Rather than have the tool’s controller as a separate unit fixed at a workstation, new tools, such as the Nexo handheld nutrunner from Bosch Rexroth, have a built-in controller with standard Wi-Fi 6 connectivity.
Integrated controllers let the tool be used virtually anywhere on the factory floor with full functionality—even in Wi-Fi dead zones. Performance is critical. The controller on Bosch’s new nutrunner has a 4-core processor for reliable and future-proof computing power even for complex assembly applications. It also features memory that can support up to 20,000 results.
Completely programmable tightening sequences and real-time quality control are built into the control; the system also features a full-color screen and lights that prompt operators as they work—including alerts if an error occurs.
Enhanced durability. Tools that are down for repair can cost assembly lines time and lost productivity. Manufacturers should consider tools engineered to deliver thousands of hours of virtually maintenance-free operation.
Key features for durability include brushless servomotors, digital transducers and other components proven to deliver high levels of uptime and to lower total cost of ownership.
Size is also critical: Look for tools with motors that are smaller and faster than previous-generation tools yet are also more efficient and lighter for high-speed assembly.
Cutting-edge ergonomics. Efficient and accurate manual assembly requires a tool with exceptional ergonomic attributes to enable assemblers to work with peak efficiency and quality. The new generation of cordless tools have lightweight and compact designs to provide a better-balanced tool that enhances ergonomics. Many also feature colored LEDs on the base and tool body to provide visual feedback on tightening tasks, even if the tools are in an unusual position.
A critical element in cordless tools is the battery. If it weighs too much or has limited charging capacity, its value is limited. Lightweight batteries are now available in a range of options. Bosch offers four battery sizes, giving manufacturers the ability to use a heavier battery with a longer runtime or a lighter one to make it easier on workers.
Digital technologies. To support Industry 4.0 initiatives, tools should incorporate multiple digital technologies, such as:
- Camera-based scanners that can capture 3D Data Matrix codes and visually document completed assemblies. They are more accurate than bar code readers.
- Browser-based operating systems for ease of programming on any connected device.
- Full-color display and external illumination, providing assembly guidance and tightening results.
- Onboard diagnostics and data collection.
ASSEMBLY ONLINE
For more information on fastening tools, read these articles:
New Fastening Tools Improve Ergonomics, Throughput
New & Noteworthy: Four New Fastening Tools
Cordless Direct-Drive Tool Behaves Like Pulse Tool