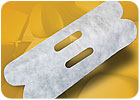
Four die-cut felt pieces are wrapped around and between the bladders, then sewed into a bag that glides over the seat cushion foam instead of rubbing against it. Photo courtesy Fabrico
The subsystem is a valve-driven unit that lets the driver determine lumbar softness and back support by controlling the inflation level of the lumbar-bladder assembly. This assembly consists of three rubber bladders welded into a 414 by 54-millimeter frame. To pass final testing, the assembly must perform for 10,000 inflation-deflation cycles with an operating pressure of 4.4 psi and hold 12 psi without bursting.
Engineers discovered that the bladders were rubbing against the foam of the seat cushion, resulting in noise, problems adjusting the back support and premature wear of the foam and bladder. To solve the problem, Alfmeier engineers needed to isolate the bladder from the foam without affecting the inflating and deflating process, and still meet customer flammability standards.
For help, the engineers turned to Fabrico, which offers custom fabrication services. Fabrico proposed wrapping four die-cut felt pieces around and between the bladders, then sewing the pieces into a bag that glides over the cushion foam instead of rubbing against it. The felt is a durable, silky material commonly used as a filter in pharmaceutical, beverage and fuel applications.
The gliding effect of the felt increases the bag life of the sewn part and enhances the overall effectiveness of the lumbar support bladder. The felt also withstands the constant inflation and deflation of the bladder and, in the process, protects surrounding foam padding of the driver’s seat cushion from the effects of continual impact.
Equally important, the felt meets U.S. and international supply specifications for flame retardancy of interior trim materials in passenger cars, multipurpose passenger cars, commercial vehicles and buses.
Under the arrangement, Fabrico procures, die cuts and orients the felt pieces in Ontario, CA, then ships kits to its plant in Monterey, Mexico. This is near the Alfmeier assembly facility in Apodaca, Mexico, where final integration into the luxury seat is performed. The arrangement gives Alfmeier a local and uninterrupted supply of material at substantial cost savings.
For more information on custom fabrication for assembly, call 800-351-8273 or visit www.fabrico.com.