Manufacturers are using artificial intelligence to improve automated inspection, generate more cost-effective product designs, and analyze reams of process data to prevent defects. Now, they can use AI to improve robot guidance.
German startup Micropsi Industries GmbH has introduced MIRAI, a new control system that enables robots to handle variance in shape, position, color and light conditions in the work space. Using AI, MIRAI generates robot movements in real time and can respond automatically to movements of the target object. MIRAI takes control of the first and last centimeters of the robot’s path, eliminating the need for rigid fixturing of parts.
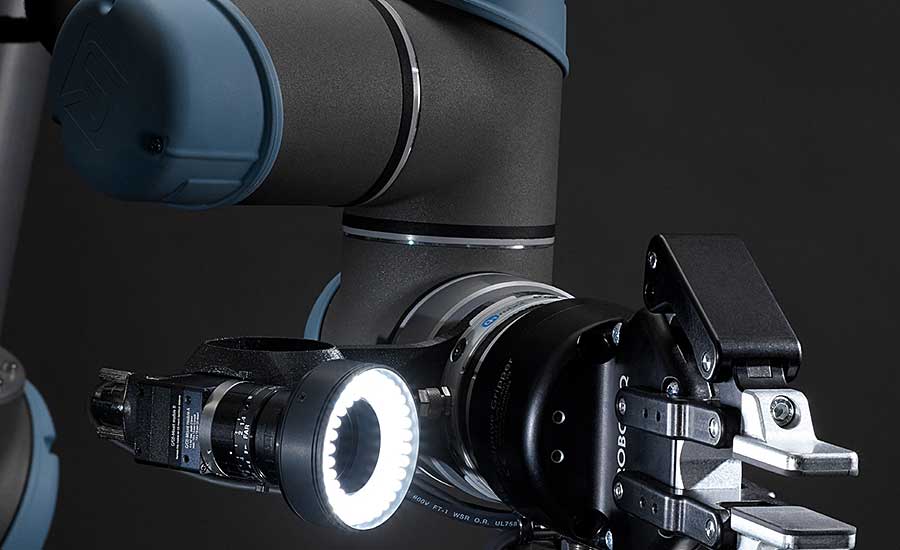
The system consists of a MIRAI controller, a six-axis robot, a force-torque sensor, an end effector, a camera, and a ring-light. Photo courtesy Micropsi Industries
MIRAI also simplifies the task of robot programming. Robots equipped with MIRAI are able to learn many tasks through observation, so they can easily be trained and retrained for various process steps. No knowledge of programming or AI is required.
The system consists of a MIRAI controller; a six-axis robot (supplied by FANUC or Universal Robots); a force-torque sensor; an end effector; a camera (supplied by Micropsi Industries); and a ring-light.
MIRAI augments the robot’s native controller, enabling the machine to perceive its work environment. Through AI, MIRAI-enabled robots observe actions performed by a person and then imitate those actions. Observations are recorded by a camera attached to the robot’s wrist or situated at a fixed position proximate to the workspace. To train the robot, a person performs and records repeated demonstrations of a task by manually guiding the robot by the robot’s wrist. The recordings are then transformed into a vision-based, real-time robot control schema.
AI And Automatic Screwdriving
In May, Micropsi Industries and fastening specialist DEPRAG announced that they are cooperating to provide a robotic screwdriving system that can compensate for variations in part position, fastening angle or manufacturing tolerances. Without guidance, screwdriving with a six-axis robot can be difficult, if not impossible.
“We are pleased to be in cooperation with such a traditional manufacturer as DEPRAG and to be able to profit from their enormous wealth of experience in the field of screwdriving technology,” says Dominik Bösl, chief technology officer of Micropsi Industries. “The cooperation provides our customers with a robust and profitable automation solution, advancing our goal to simplify access to automation.”
The system from DEPRAG and Micropsi can also enable a robot to install screws in assemblies as they pass by on a conveyor.
The system is suitable for the assembly of a wide range of products, including appliances, electronics, automotive parts and agricultural machines.
To see a video of the screwdriving system, click here.
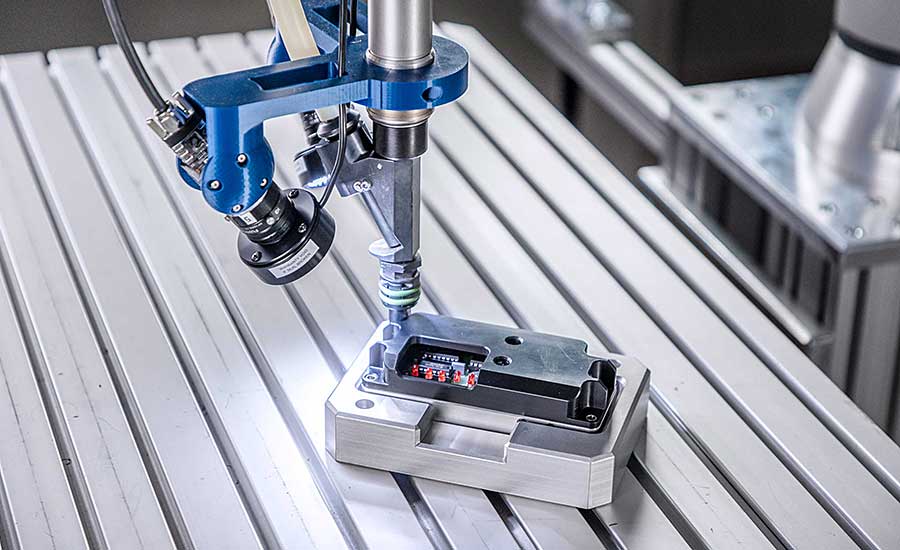
Micropsi and DEPRAG are cooperating to provide a robotic screwdriving system that can compensate for variations in part position, fastening angle or manufacturing tolerances. Photo courtesy DEPRAG
Refurbishing Turbine Vanes
Siemens Energy is using Micropsi’s technology to automate the process of refurbishing gas turbine vanes.
After four years of use, the vanes must be reshaped and resurfaced. Along the surface of the vanes are hundreds of tiny holes, each roughly 2 millimeters wide. These holes were used for air cooling during the vane’s previous use, when temperatures in the turbine get so hot that the vanes would melt without measures like air cooling and protective coatings.
In the refurbishment process, these holes must be filled in before surface treatment. This involves dispensing solder paste into each hole with a thin needle.
The dispensing task poses three challenges. First, the hole positions on the vane vary because of temperature deformation in the vane during use. Second, dispensing the solder paste is time-consuming. With hundreds of holes to fill, it takes hours for a person to fill them all. Finally, the vanes come in different versions and exhibit different levels of wear.
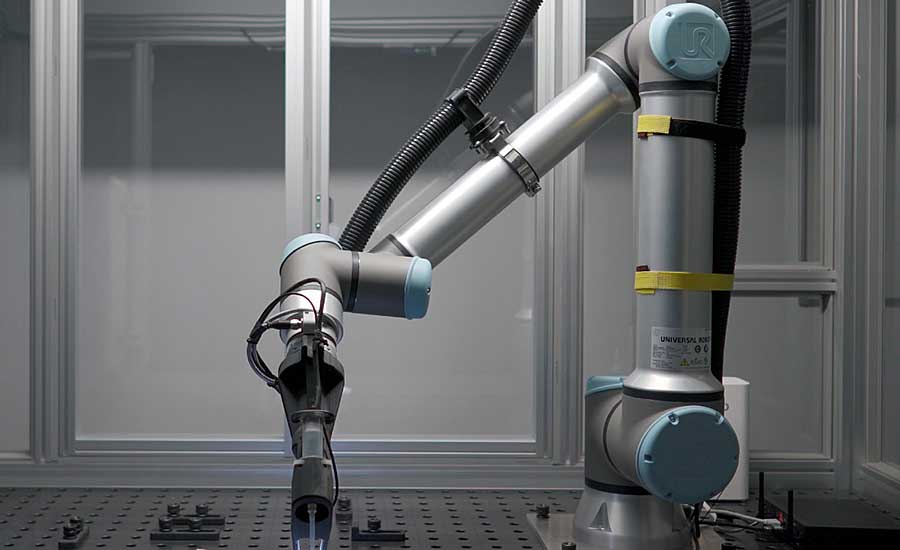
Using the MIRAI control system, a six-axis robot dispenses the solder paste on the vanes in a fraction of the time of a person. Photo courtesy Micropsi Industries
Using the MIRAI control system, a six-axis robot dispenses the solder paste on the vanes in a fraction of the time of a person. Thanks to AI, the robot compensates for variations in hole position, vane shape, and vane condition.
The MIRAI system handles moving the robot from one hole to the another and inserting the needle into each hole. The robot’s native controller handles the dispensing the soldering paste and other parts of task. Training the MIRAI-powered robot took only a few days and was done by Siemens engineers.
Better Machine Tending
Auto parts supplier ZF in Friedrichshafen, Germany, wanted to automate machine tending in a high-volume milling station where gears are manufactured. In this case, metal rings are picked from a crate and placed onto a conveyor. The ring is the raw part of what will become a gear during subsequent manufacturing steps.
This task posed multiple challenges for automation:
- The rings in the crate shift during transportation, making their positions unpredictable.
- The position of the crate, once delivered and facing the robot, can vary 20 to 30 millimeters in all directions.
- The form of the crate can vary. Sometimes its sides are not straight. They can be pressed inward, with a deviation of 20 to 30 millimeters.
- In the spring and autumn, the work space gets direct sunlight. Although a crate’s inside walls are covered with carton paper, one-third of the rings are still directly exposed to sunlight.
- Bubble foil on the inside of the crate covers some parts of the rings.
- The surface of the rings can have oil and rust. This creates variance in their appearance to the vision system.
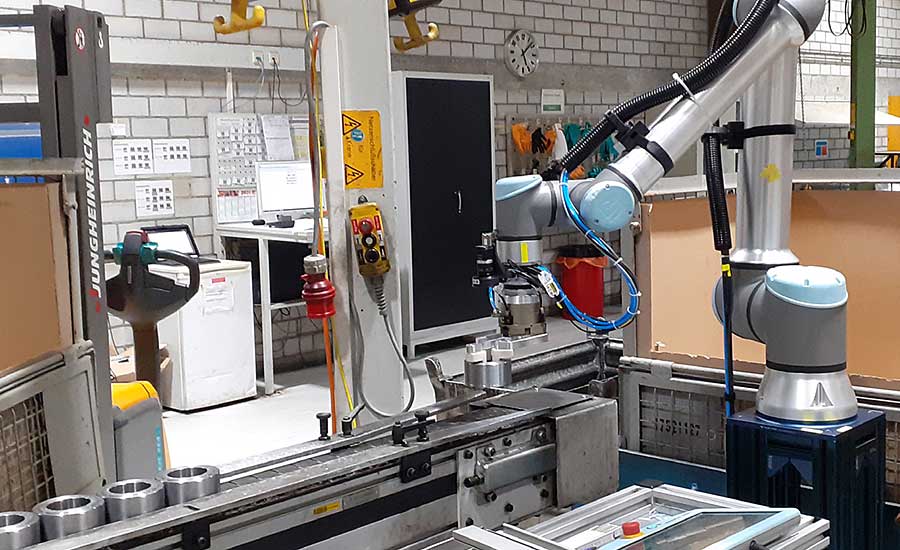
ZF uses a vision-guided robot to transfer metal rings from a box onto a conveyor. Photo courtesy Micropsi Industries
A conventional robot—with or without a vision system—would have difficulty with such variation. And, even then it could, the setup would have to be tailored for that specific task and no others.
Micropsi developed a faster and more reliable system. The system consists of a MIRAI kit, including the control box and the camera; a Universal Robots UR10e cobot; an OnRobot force-torque sensor, and a Schunk gripper.
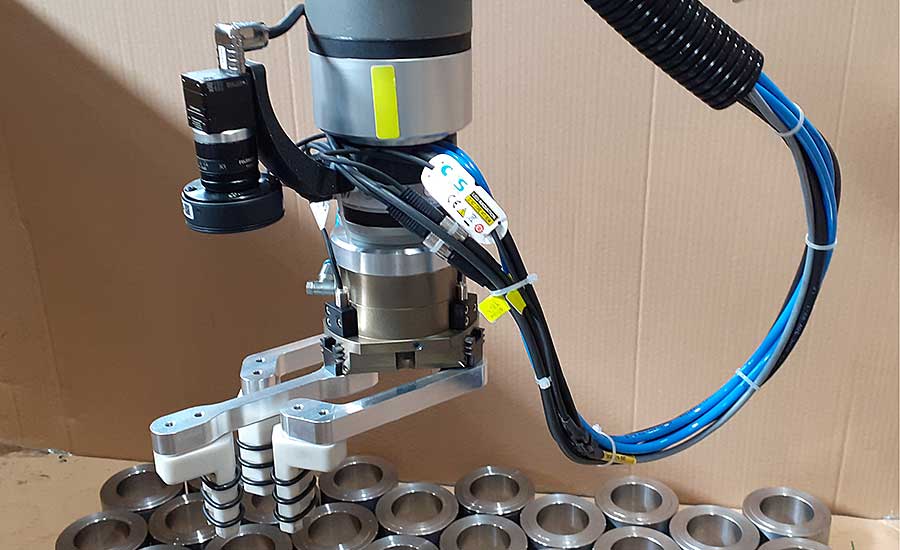
To enable the vision system to view parts from a perpendicular angle, Micropsi designed gripper jaw extensions. The plastic fingers have grooves that provide a better grip on the gummy rings. Photo courtesy Micropsi Industries
The metal rings in the crate arrive in layered beds. The parts are laid closely together on their flat sides. Via its native controller, the UR robot was programmed to move above individual rings in the crate. Once the robot is above a ring, the MIRAI system takes control. It moves the robot to the nearest ring and places the gripper in position. Next, the robot’s native system reassumes control. The robot picks up the ring, moves it to the conveyor, and places it on the belt.
Training the cobot to carry out its part of the process took only four days.
To enable the vision system to view the parts from a perpendicular angle, Micropsi designed three gripper jaw extensions. After the jaw extensions were mounted, 3D-printed plastic fingers were fixed to the end of the extensions. These fingers have grooves that ensure a better grip on the gummy rings.
Founded in in 2014, Micropsi is headquartered in Berlin and has a U.S. office in San Francisco. For more information on AI control systems for robots, visit www.micropsi-industries.com. For more information on automatic screwdriving systems, visit www.depragusa.com.
MORE FROM ASSEMBLY ONLINE
For more information on screwdriving, read these articles:
Screwdriving With Cobots
Automotive Supplier Uses Screwdriving Spindle to Test Fuel Caps
Error-Proof Screwdriving