What do Paul McCartney and Taylor Swift have in common? Aside from being two of the most successful recording artists in history, both superstars use Taylor Guitars.
So do many other popular musicians, such as Zac Brown, Billie Eilish, Finneas, Jason Mraz, Jewel, Sarah McLachlan, Katy Perry and Neil Young.
Taylor’s extensive line of acoustic and electric guitars are also used by thousands of amateur strummers and weekend pickers who appreciate cool sounds generated by well-made instruments.
Taylor produces up to 700 guitars a day at two factories located in El Cajon, CA, and Tecate, Mexico. Many instruments on the company’s assembly lines are unique and built to order.
Learn more about ASSEMBLY'S
Plant of the Year award
The 49-year-old company prides itself on innovation and playing its own tune. Taylor is known for “blending modern, innovative manufacturing techniques with a master craftsman’s attention to detail.” That’s why it uses CNC machines, laser cutters, robots and in-house developed automation to streamline production and improve quality.
In addition, Taylor is a leader in sustainability. It uses a variety of wood that is ethically sourced from around the world. Recent initiatives have focused on responsible stewardship of natural resources by planting trees and upcycling. In fact, the company was recently inducted into the International Green Industry Hall of Fame for its environmental efforts and honored by Fast Company magazine for its manufacturing innovations.
Taylor Guitars is also the recipient of the 2023 Assembly Plant of the Year award sponsored by ASSEMBLY Magazine. The world-class plant was chosen for the 20th annual award because of its innovative use of automation, green manufacturing, process controls and vertical integration.
The company has pioneered new guitar designs and construction techniques. And, it’s been out in front when it comes to developing and adopting production technology. In addition, the employee-owned company is a leader in developing groundbreaking forest stewardship programs.
Taylor Guitars doesn’t just talk about ecology, recycling and sustainability. It lives and breathes it as part of the company’s DNA.
As part of its Ebony Project, Taylor acquired a sawmill in Cameroon where it also funds research about ebony ecology, including a replanting initiative that has planted more than 30,000 ebony trees and 15,000 fruit trees. In Hawaii, in partnership with Pacific Rim Tonewoods, Taylor Guitars has planted about 8,000 trees.
The company has also pioneered an innovative urban wood sourcing program that turns end-of-life city trees into beautiful guitars instead of mulch or firewood. The initiative has already produced thousands of Urban Ash guitars.
Taylor also turns scraps of wood into kitchenware products, such as cutting boards and tongs, which are marketed by sister company Stella Falone.
“Our blend of proprietary, innovative technology with impeccable hand-craftsmanship has led to unparalleled quality and consistency in the production of our guitars.”
– Chris Wellons
But, above all, the company excels at making musical instruments that are known for their quality.
“We do our best to take wood that doesn’t always cooperate and make some of the best guitars money can buy,” says Chris Wellons, vice president of manufacturing at Taylor Guitars. “We’ve set the standard for modern-day precision craftsmanship to create the best possible playing experience.
“Our blend of proprietary, innovative technology with impeccable hand-craftsmanship has led to unparalleled quality and consistency in the production of our guitars,” explains Wellons. “We have gone from a small, unknown company to one of the world’s largest producers of high-end acoustic guitars.”
“We’re proud of the work we do, our factories and especially the people we get to work with,” adds Andy Powers, president, CEO and chief designer at Taylor Guitars. “We’ve developed plenty of cutting-edge equipment, working methods and techniques. But, what I see as the most unique and valuable contribution toward our success is the way so many folks here have applied their energy and expertise toward building the best guitars and factory we can have.
“All across our company, we have great employees contributing toward our development, tooling, engineering and production all the way to marketing, sales and finance,” claims Powers. “A successful factory takes the efforts of a village, and we’re fortunate to have such committed people applying their best efforts here at Taylor.
“Our relationships are the magic ingredient in our recipe for success,” Powers points out. “The relationships between our founders, our employees, our departments, material suppliers and dealers all the way to our customers. The ways we work with each other are key to designing, developing and manufacturing great guitars to put into the hands of musicians year in and year out.”

Taylor Guitars has pioneered many new designs and construction techniques. Photo courtesy Taylor Guitars
Humble Beginnings
Taylor Guitars was started in the 1970s by two kids barely out of high school who shared a passion for fine craftsmanship and aesthetic beauty. Along the way, they modernized the guitar-making process by harnessing technology to develop many innovative manufacturing tools and techniques that brought new levels of accuracy, refinement and consistency to the tradition-bound musical instrument industry.
Bob Taylor grew up in a house in Southern California where his father built the furniture. In his spare time, he picked up some tools and began tinkering with wood and metal. When he couldn’t afford to buy a guitar that he wanted, 18-year-old Taylor decided to build one himself. That eventually led to a job at a small San Diego guitar shop called the American Dream.
Taylor soon became friends with another young employee named Kurt Listug. In October 1974, after learning that the owner was selling the shop, Listug and Taylor partnered to buy the American Dream and struck out on their own. Since Taylor did most of the designing and building, while Listug focused on sales and marketing, they decided to put the former’s name on their new guitar’s headstock.
Taylor and Listug focused their attention on acoustic guitars, which were beginning to make a renaissance after the electric guitar craze of the 1960s. Working out of a small factory in Lemon Grove, CA, the novice luthiers experimented with a variety of designs and materials, such as slim guitar necks and bodies made from exotic Brazilian or Indian rosewood.
The small company specialized in making custom guitars. However, at the time, most steel-string acoustic guitars were still made using traditional designs and production methods that were laborious. Bob Taylor’s lack of knowledge about historic guitar models enabled him to develop his own construction methods and tonal signatures.
Taylor slowly built a reputation for making instruments that were easy to play, because his necks were similar to the slim design of electric guitars. In addition, he experimented with a new type of bolt-on neck joint that would eventually revolutionize the industry. The prevailing design at the time was a traditional dovetail joint. Taylor also bucked tradition by fretting guitar necks after they were attached to bodies.
By the mid-1970s, Taylor started to sell guitars to local dealers for the first time and in 1976 managed to build 168 instruments. A few years later, the company purchased some additional woodworking equipment that enabled it to speed up the processing and tooling of raw materials.
Taylor started to build fixtures, jigs and workstations in-house, often rummaging through dumpsters and junk yards for parts. One of its first home-grown designs was a device for shaping guitar bodies.
Around this same time, Taylor started to distinguish its products by allocating designated names or series, using a three-digit numbering system. The first number indicated the series; the second whether it’s a six- or 12-string instrument; and the last digit referred to the body size. Taylor’s first guitar line was dubbed the 800 Series, which was quickly followed by the 700 and 900 Series.
Taylor toyed around with various production techniques, such as reorganizing its small shop into dedicated departments for neck assembly, body assembly and finishing. That strategy enabled the company to maintain a smooth flow of materials and a daily volume that averaged about three guitars.
The young company grew slowly during its first decade in business. By 1978, Taylor built 449 guitars with 11 employees, turning out an average of 16 instruments per week.
However, acoustic guitars fell out of favor during this time, due in part to trends such as disco music and synthesizers. After enduring several lean years, Taylor was making 520 guitars a year by 1984. To further distinguish itself from more established competitors, the upstart company began staining wood on some of its guitars in shades of blue, green and red.
The innovative technique allowed the grain of spruce tops and the flame of maple backs and sides to show through, causing a stir in the industry. Musicians began to notice the unique look, and Taylor received an unanticipated promotional boost when a purple 12-string guitar appeared on Prince’s popular “Raspberry Beret” music video.
The growing company moved to a new 4,700-square-foot factory in Santee, CA, in 1987, which enabled it to implement a new production line and boost production to 10 guitars a day. By the end of the 1980s, Taylor also started to make its own custom-fitted guitar cases.
By then, the company offered a full line of guitars with three body shapes and a variety of woods. A team of 40 employees was turning out 2,000 instruments a year.
To keep up with growing demand, Taylor invested in new production technology, such as CNC milling machines. Instead of relying on drill presses, lathes, shapers and other traditional woodworking tools, Taylor began using a CNC machine to mass-produce bridges, cut fret slots, shape fingerboards and make other guitar parts with greater accuracy, precision and repeatability.
The new production technology enabled Taylor to boost productivity and reduce costs. It also helped the company create a solid wood guitar that sold for less than $1,000, which was hailed as a huge breakthrough at the time.
When it debuted in the early 1990s, the 410 model was almost $200 cheaper than the company’s most affordable model, but it featured the same high-quality neck shape, internal bracing and geometry. The guitar, which took less time to produce than other models, became an instant hit, forcing Taylor to add a second shift to keep up with demand.
In 1992, Taylor moved to a 25,000-square-foot factory in El Cajon. After five years of steady growth, the company expanded into a second building located next door. The 44,000-square-foot facility enabled Taylor to streamline the way that it processes wood and builds guitars. That expansion was followed two years later with a new satellite factory located 40 miles south in Tecate, Mexico. Today, that facility mass-produces lower-priced models and guitar cases.
Taylor currently sells guitars in 65 countries around the world through a network of distributors and dealers. Because one-third of the instruments made at the 2023 Assembly Plant of the Year are exported, Taylor Guitars operates a warehouse in Amsterdam. The company also recently started to sell products directly to consumers via its website.

The 2023 Assembly Plant of the Year manufactures acoustic and electric guitars. Photo courtesy Taylor Guitars
Diverse Product Line
Guitars have a universal appeal. In fact, they are the most popular musical instrument in the world. Part of that popularity is due to the fact that guitars are portable and easy to play. They’re also widely used accompaniment instruments.
“Whether leading a flamenco dancer, a blues singer, a rock band, a jazz quartet or a bluegrass string band, one of the most common and significant roles that a guitar plays is to support other musicians,” says Powers. “It’s capable of driving rhythms like a drummer, establishing harmonies like a piano and filling in melodic lines.”
Taylor’s diverse product line includes many types of acoustic and electric guitars. And, it plans to launch a niche line of acoustic guitar amplifiers in January under its new Circa 74 brand.
While all guitars may look the same to a casual observer, there’s actually a big difference and a wide variety of products. In the music world, the term “acoustic” refers to anything that isn’t electrically amplified. The vibration of the guitar strings is amplified by the guitar body, with natural volume and tone coming from different elements of the body’s construction.
An electric guitar, on the other hand, relies on electronics to amplify its sound. Unlike an acoustic guitar, it does not have a soundhole and lacks natural volume. Pickups make up for this.
A pickup is essentially a set of magnets wound with wire that sits on the body beneath the strings. Each magnet works to convert the vibration of an individual electric guitar string into electricity, and this is output through an amplifier to create sound.
The pickup is the backbone of the electric guitar’s tone. Depending on the materials used and their configuration, pickups can sound vastly different from one another.
The most immediate difference between acoustic and electric guitars is in the way they sound. The former are known for unplugged volume and the length of time notes ring out for. When you strum a chord, the wood sings.
Because an acoustic guitar’s body shapes its sound, different models produce a wide range of tones. The shape, size and type of wood used in construction all play a unique role.
Electric guitars are thinner than their acoustic cousins and sound more or less the same on their own. They only come to life when hooked up to an amplifier. While wood type and construction aren’t arbitrary, the sound of an electric guitar comes mainly from its pickups, as well as different amp settings and effects pedals like distortion, reverb and modulation.
Taylor makes guitars in multiple body shapes and different types of wood. Products range in size from the Baby, which features a body that is 15.75 inches long, 12.5 inches wide and 3.5 inches deep, to the Grand Orchestra, which has a body that’s 20.5 inches long, 16.75 inches wide and 5 inches deep.
Taylor’s flagship acoustic guitar is the 814ce (the “ce” refers to a cutaway on the body with onboard electronics that allow it to be plugged in and amplified), while the T5z Series anchors the company’s electric line up. However, all of its products feature a signature look, such as a distinctive headstock, bridge and pickguard shape. Other Taylor trademarks include proprietary C-Class and V-Class bracing that’s used inside many bodies to provide structural support and “voice” the instruments in nuanced ways.
Guitars range in price from $399 for a BT1 Baby Taylor to $35,000 for custom models featuring exotic woods and intricate inlays that are prized by collectors. However, most products made at the state-of-the-art El Cajon factory range from $2,000 to $10,000.
“We currently complete around 125 guitars a day here, but we can make upwards of 180 guitars a day if demand spikes, which happened a few years ago during the Covid pandemic,” says Wellons. “Every instrument we make in the U.S. has a solid wood back, top and sides.
“Our sister plant in Mexico produces more guitars, because it specializes in lower price points,” explains Wellons. “The backs and sides of those instruments use three layers of wood—a core piece with veneer layers that are laminated together on either side. But, all of the tops are solid wood.
“Both facilities use similar production processes and equipment,” Wellons points out. “However, our headquarters plant in California produces some parts, such as saddles, that are shipped to Mexico. And, everything made there is sent back to our warehouse in El Cajon for distribution.”
Wood Whisperers
Taylor Guitars uses a variety of “tone woods,” including ash, cedar, koa, mahogany, maple, rosewood, spruce and walnut. The type of species used to make an instrument can have a huge impact on its sound and performance.
Different tone woods have distinctive physical traits, such as varying degrees of density, hardness and weight, that translate into different resonant properties across the frequency spectrum.
For instance, maple has diffuse pores in its grain structure, so as far as stability is concerned, it does not have more flex in one direction over another. Indian rosewood is a classic guitar material that provides a wide frequency range and overtone richness on both the low and high ends of the musical spectrum.

Guitar tops are typically made out of mahogany (top) and spruce. Photo by Austin Weber
Harder, denser woods like koa and mahogany are typically used on the back and sides of a guitar. Sitka spruce is used for a majority of tops and inside bracing. Ebony is widely used for the fingerboard (its high density is useful for holding frets in place and resisting wear) and the bridge of guitars.
The hardwoods used for a guitar’s back and sides (the same species is used for both) contribute rigidity and stability to an acoustic guitar body. This helps generate more sustain (how long the vibrations on guitar strings last) from notes as they ring out. The back and side woods used also emphasize certain resonant frequencies in ways that add unique textures to a guitar’s overall sound.
“Woods are to a guitar maker what ingredients are to a chef,” says Powers. “They have certain inherent properties that translate into sonic flavors, but it’s all about how the guitar maker works with them. Good guitar design is important, because it helps harness the best of a wood’s natural sonic characteristics.”
Wood is what gives Taylor guitars their signature look, feel and sound. However, it presents numerous challenges to the company’s engineers and production team. To ensure consistent quality, raw materials must undergo a rigorous process before any guitar ever gets built.
“Working with wood is unlike aluminum, plastic or other materials commonly used in manufacturing,” says Wellons. “Even though it’s a dead tree, wood is still a living thing. Holding tight production tolerances can be challenging. We mill wood like we’re milling aluminum, using a tolerance within 0.004 inch.
“All the woods we use have unique characteristics,” notes Wellons. “Trees grow differently, so wood grain structures can be inconsistent. The way wood dries and moves can also be different. It’s much different than using metal or plastic, which is very consistent and standardized. Each piece of wood has its own personality, even within its own species. For instance, some wood comes from trees that grew fast vs. others that grew slow or under different stresses during their lifespan.
“We need to coax every single piece of wood along and be patient,” explains Wellons. “Depending on the species involved, the wood preparation process can take weeks or months.
“Wood is a living and breathing material,” adds Wellons. “It’s always a challenge to work with, due to moisture content. We have to go through a number of steps in the drying and acclimation process to get wood stabilized. Even after assembly, wood is constantly moving and adjusting.
“To build a quality guitar, you need to have the correct moisture content,” says Wellons. “So, wood drying is a critical step in our production process.”
Taylor Guitars maintains a large inventory of various types of tone woods. In fact, the El Cajon campus includes an entire building that’s solely dedicated to treating and preparing wood for production. Inside the facility, large fans and kilns are used to carefully dry stacks of koa, mahogany and other imported species.

Prototypes of every Taylor guitar are built in this workshop and design studio. Photo by Austin Weber
Unique Assembly Challenges
The 2023 Assembly Plant of the Year is nestled in a hilly industrial park east of San Diego that looks more like a college campus at first glance. Taylor Guitars operates in 178,000-square-feet of space spread out over seven neighboring buildings. However, only two structures are used for actual production. Other sites include a tooling department, a design studio, offices, a repair facility, a warehouse and a distribution center.
Taylor Guitars prides itself on in-house tooling and milling departments that turn out a variety of metal and wood parts. The facility is vertically integrated, with more than 40 CNC machines, laser cutters and robotic sanders. In fact, the company makes just about everything needed to build a guitar except for frets, tuners and strings.
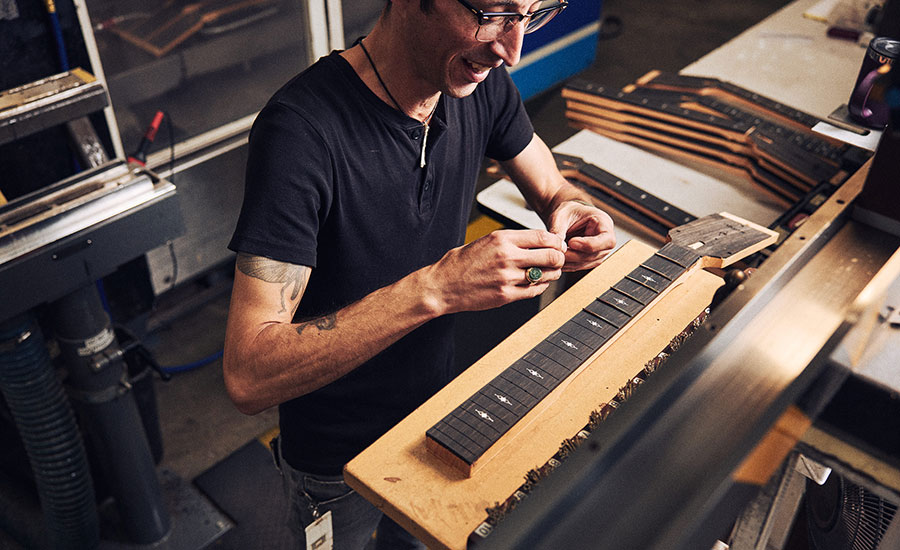
Frets are metal bars on a guitar neck that run perpendicular to strings to shorten the vibrating length of each string. Photo courtesy Taylor Guitars
“We have an entire tooling and engineering division devoted to making our latest guitar designs production-ready,” says Wellons, who’s worked at the company for 31 years. “This includes everything from developing the programs we use with our sophisticated computer-controlled mills and robots to fabricating our own tools and machines to help our skilled artisans produce our guitars.
“That unique integration of technology, tooling and skilled hand-craftsmanship makes our guitar factory operation truly one of a kind,” claims Wellons. “Not only does this allow us to imbue our guitars with impeccable detail work, but the superb build quality gives players an heirloom-quality instrument.
“If we didn’t have our engineering and tooling team, we’d be lost,” Wellons points out. “We can make parts ourselves much faster than relying on suppliers. Vertical integration allows us to get things done quickly and maintain quality. Our in-house team also builds many of our production machines, tools, jigs and fixtures.”
In the milling department, parts such as the tops and backs of guitar bodies are cut to shape and sanded to thickness. Operators also use laser cutters to produce neck angle shims, inlays and other intricately shaped parts.
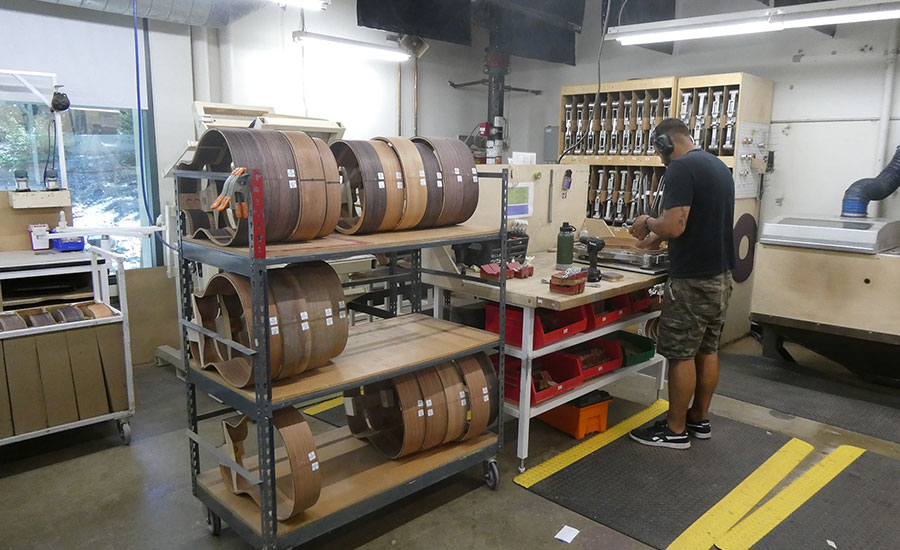
Various sizes and shapes of guitar sides wait to be joined to tops and bottoms. Photo by Austin Weber
Work in process flows back and forth between the two buildings on manual carts every morning and evening. The neck and body are built in one facility, while the final assembly and finish departments are located in the building next door.
Because wood is so finicky, climate control is essential. In several production areas, temperature is consistently maintained around 72 F, with 50 percent relative humidity.
Assemblers in El Cajon produce 10 different series of guitars that amount to around 900 SKUs. However, the two main subassemblies are bodies and necks, which are produced in separate departments.
“Grain structure is very important with the wood that we use to make guitars,” says Wellons. “That’s why we use quarter-sawn wood to build all of our tops, which provides a vertical grain structure.
“Some wood that we work with requires days of rest in between processing before it can even become a part of a guitar,” explains Wellons. “It once took us anywhere from 17 to 20 working days to get a guitar from start to finish. Today, the typical guitar we make in El Cajon takes 10 to 12 days.
“The most complicated process that we do is neck production,” Wellons points out. “It demands precision through the building and assembly process. Because the neck is adjustable, if parts aren’t precise and within the required tolerances, it can create problems downstream.”
Neck and Body Building
Taylor Guitars claims that its instruments are “designed to wear in, not wear out.” To help enable that, the company uses a patented joint design that precisely connects the neck to the body. Unlike competitors, the NT neck is bolted on instead of attached with adhesive.
When it debuted in 1999, the innovation was hailed by some experts as one of the most significant improvements to acoustic guitar design in the 20th century. The design not only allows the neck angle to be set with pitch-perfect accuracy, it also allows for easy micro-adjustability over time, allowing the guitar’s playability to be maintained for a lifetime. It also makes the neck more stable in the face of humidity fluctuation.
“We produce a three-piece neck so that we can perform all fly cutting and machining operations before we attach it to a body,” says Wellons. “This enables us to make a more precise and more playable neck than we made in the past.”
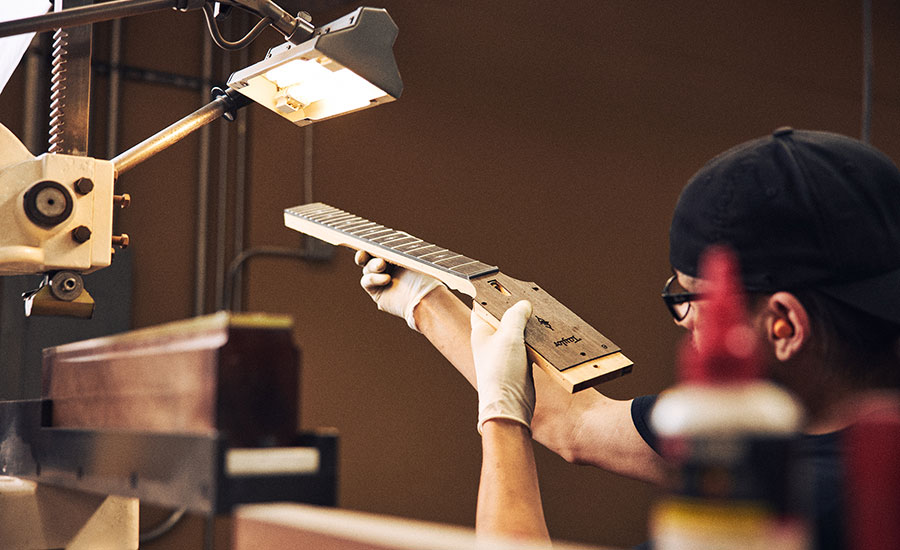
Taylor Guitars uses a unique three-piece neck design. Photo courtesy Taylor Guitars
The three-piece design consists of a main neck shaft, a peg head and a heel that are joined together with yellow aliphatic resin. The pieces are all cut from the same wood blank to maintain consistent density, wood grain and coloration.
It combines structural improvements with greater CNC milling capability, which enables Taylor luthiers to make a straighter, more stable neck. The three-piece design also reduces wood waste.
“Adopting our three-piece design approach allowed us to change the cutting specifications for our neck wood (typically mahogany) to increase the yield from each tree harvested,” says Wellons. “Rather than cutting traditional rectangular 3-by-4-inch neck blank dimensions, we changed our specification to cutting 4-by-4s.
“This ensures the proper grain orientation every time,” explains Wellons. “These improved operations in the milling department increased our yield by 33 percent. It also improved yield on the forest floor by 50 percent, because it allows us to be less selective about the 4-by-4s that come out of a log. It’s a good example of our ability to re-engineer a process not only to improve the guitar’s performance, but to reduce material waste.”
Two pockets are precision-routed into a neck block built into the guitar body using a CNC mill. The pockets are cut perpendicular to each other. A pair of neck angle shims are inserted into the pockets to set the precise neck angle, and then the neck is inset into the pockets and bolted securely in place.
One of the benefits of this approach is that the fretboard extension does not need to be glued to the guitar top to secure it, which helps make the neck more stable in the face of humidity fluctuation.
Laser-cut and milled in varying increments of 0.002-inch, precision shims help set the perfect neck angle to optimize the feel and sound of the guitar. The shims are inset (without glue) into the two pockets where the neck will meet the body. They can easily be changed to micro-calibrate the neck angle during the final assembly process and throughout the guitar’s life.
The glueless, three-bolt assembly ensures a secure wood-to-wood surface connection between the neck and body, which enables a strong transfer of sound.
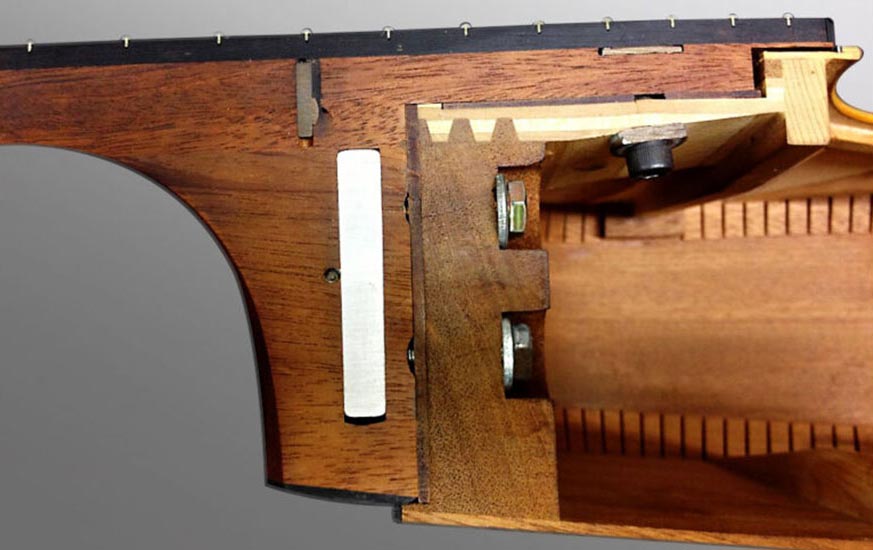
Each Taylor Guitar neck is attached to a body with three bolts. Photo courtesy Taylor Guitars
The design also makes it easy to remove the neck for service at any time, because there’s no glue joint that needs to be steam-treated to loosen for removal. In addition, the patented neck joint allows the string height above the frets to be set low, which makes it easier for guitar players to form chords.
To eliminate bottlenecks, Wellons and his engineering team recently produced spaghetti diagrams of the entire neck-building process. “We decided to make work centers and reconfigure our machines on the shop floor,” he points out. “The beauty of our machines is that they’re mobile.
“We used to have a workcell that required operators to go from machine to machine,” notes Wellons. “To eliminate wasted motion, we now have machines facing each other that perform similar operations so that one person can operate up to three machines.
“The new neck-building operation has streamlined production and made it less complex than in the past,” says Wellons. “The actual takt time is less, because there’s less hands-on work required.”
While the body of an acoustic guitar has its own quirks, it’s much more straightforward than the neck assembly process. Assemblers take bent sides that are lined to improve structural integrity and rigidity, and join them to a back and a top that is internally braced. After they glue those three subassemblies together, luthiers add decorative edges called binding.
However, the entire production process is much more complex than it sounds. That’s because bodies play a unique role in guitar performance. In addition to the type of tone wood and internal bracing that are used, body shape is critical.
“A small body will produce a smaller sound than a big-bodied instrument,” explains Wellons. “A small body guitar with a tight waist area will produce a much different sound than a small body guitar with a wider waist on it. Parlor guitars are smaller and sound different than a jumbo-sized guitar. Comfort is also a factor.
“Body assembly takes longer than neck assembly,” Wellons points out. “That’s because all of the parts must sit for two days after they’re delivered to the body department so they can acclimate to their surroundings in a climate-controlled facility.
“Some parts will gain moisture based on the relative humidity, while others will lose moisture,” says Wellons. “We need to stabilize the parts before we bend, block, brace or line them so that they’re not moving during the process.”
Bending and shaping wood sides are critical to a guitar’s performance and aesthetics. By bending a piece of wood, it becomes more rigid.
Side bending starts with two rectangular panels of wood that are shaped by laser cutters and then sanded to a smooth finish. Once the two halves are shaped, they’re joined together with a heel block and a tail block using yellow aliphatic resin to form a complete guitar side.
Taylor engineers developed and built jigs, molds, shims and machines in-house that use heat and pressure to semiautomatically bend parts. They’ve also created some automated cutaway benders. However, it’s one of many precise guitar building processes that has proven impossible to automate with robots.
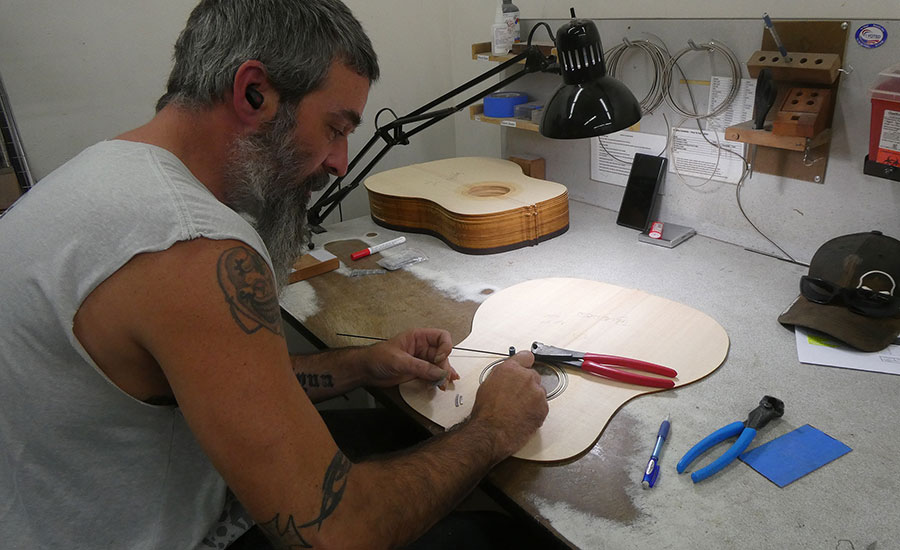
Decorative rosettes are manually applied to guitar tops. Photo by Austin Weber
Rosette assembly is a good example of why human touch is required. Rosettes are decorative elements that surround a guitar’s open, circular sound hole. The thin strips are made from a variety of wood and other materials, including ABS plastic, acrylics and sea shells, such as abalone and mother-of-pearl.
The different substrates are attached using cyanoacrylate adhesive. The intricate process must be done by hand, because it’s impossible to do with a robot or other type of machine.
Another critical assembly step that’s done manually by skilled luthiers occurs on the reverse side of guitar tops, which are also referred to as soundboards. That’s where assemblers install bracing. Taylor’s bracing department is located next to the side bending department in a climate-controlled room.
Bracing plays an important role in the way that a guitar sounds. It provides internal structural support to withstand string tension and distributes string energy in controlled ways that are converted into acoustic sound.
“Bracing provides different constructions, strengths, tones and sounds,” explains Wellons. “A very short and wide brace, for instance, will produce a different quality than a tall and narrow brace. That’s why we’ve made quite a few changes and modifications to bracing over the years.”
The type of wood species that bracing is made out of can make a huge difference. Taylor mills thin, precise strips of bracing out of Adirondack spruce and Sitka spruce. Strips of kerfing (lining inside a guitar that provides a surface to connect sides to tops and bottoms) are milled out of mahogany.

Kerfing is used to help connect guitar bodies with tops and sides. Photo courtesy Taylor Guitars
Five years ago, Taylor revolutionized the acoustic guitar industry with a new design called V-Class bracing. It replaced the traditional X-brace design, which has been around since the mid-1800s.
Instead of arranging the main support braces as a crisscrossed X, two longitudinal braces are attached with yellow aliphatic resin in a V formation, with the top of the V splayed along either side of the sound hole. The unique design helps create a guitar that is louder and produces longer sustaining musical notes.
In the body assembly department, guitar sides, tops and bottoms are attached and inserted into an in-house built fixture for curing. When bonding wood to wood, assemblers use a yellow aliphatic resin glue dispensed from handheld squeeze bottles.
Finishing is the next step in the guitar-building process. Assemblers in El Cajon use three six-axis robots for this delicate task. In the mid-1990s, Taylor pioneered a new UV-cured finish for its guitars, which enabled the company to use 60 percent less finish and speed up processing time from seven days to one day. At the time, the finish was half as thick as the existing industry standard.
“We use a matte finish that’s 2 mils thick and a fit finish that ranges from 3.5 to 6 mils, depending on color and gloss,” notes Wellons.
Taylor also was the first guitar manufacturer to use RFID tags, which are attached to the neck and body. It enables Wellons and his colleagues to track every step of the production process and monitor key performance indicators. Assemblers can also pull up specs and work instructions with the system, which is based on an in-house developed factory automation control system.
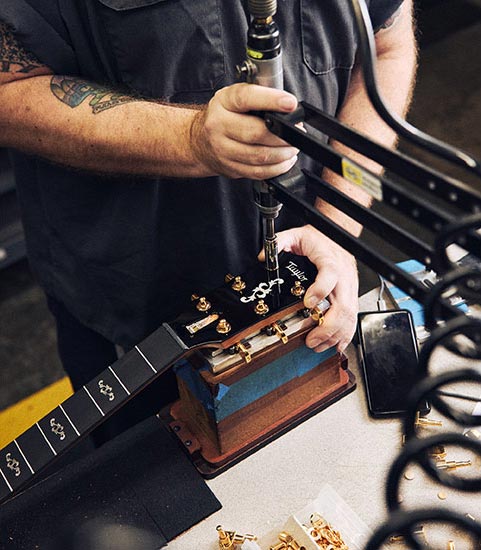
Pneumatic fastening tools are used to securely tighten tuners. Photo courtesy Taylor Guitars
Final assembly is usually a two-day process. On the first day, piezoelectric pickups that are assembled in-house by four SCARA robots are inserted into the body of select guitars behind the saddle (a component that lifts the strings and is attached to a bridge). The neck gets frets and tuners installed, while bridges and pick guards are attached to the top with adhesive.
On the second day, the neck gets attached to the body with three bolts using pneumatic tools that measure torque. Finally, strings are attached and stretched using battery-powered tools. Then, each guitar is tuned to pitch at the same workstation. Finished products are sent to the shipping department where they’re inserted into guitar cases and boxed.
Automation vs. Tradition
The 2023 Assembly Plant of the Year employs some of the best luthiers in the world who are skilled at crafting fine wood instruments. But, that doesn’t mean that Taylor Guitars shies away from using automation. It has actually embraced robotics, machine vision and other state-of-the-art production technology to improve productivity, address ergonomic issues and boost quality.
“Unlike in many other industries, guitar customers like to know that their products are made by hand,” says Tyler Robertson, robotics engineer. “It’s a product that they hold in their hands. Hand craftsmanship makes the product more desirable. We apply automation intelligently and responsibly to make our guitars even better.”
Since he arrived at the company nine years ago, Robertson has attempted to blend traditional manual production methods with automation. But, he’s discovered that automation can’t be applied to everything. Some parts of the guitar-building process simply can’t be accomplished with robotics.
“When I joined Taylor Guitars, I thought we’d have about 100 robots in operation by now,” notes Robertson, who previously worked for a systems integrator that specialized in automotive and aerospace applications. “My initial goal was to automate a lot of the production processes. But, once I became more educated on guitar building and high-end woodworking, I discovered that wood presents numerous variances and tolerances that often don’t make automation a viable option. There are also many variances involved with our guitar models.”

Buffing applications use six-axis robots to reduce the risk of repetitive motion injuries. Photo courtesy Taylor Guitars
Taylor currently uses 12 robots, including SCARA and six-axis machines, for adhesive dispensing, buffing, finishing and electronics assembly applications.
“Buffing was our initial robotic application, back in 2001,” explains Robertson. “Since then, we’ve gone through three generations of robots. Our newest robotic application is for dispensing a two-part epoxy for assembling part of guitar necks.
“We have to carefully balance automated and manual assembly, because hand work can lead to some types of repetitive motion injuries,” says Robertson. “Ergonomics was the No. 1 reason why we implemented buffing robots. It’s also why we plan to soon start using some robots for sanding. We also hope to deploy some collaborative robots in the future.
“Automation helps take care of most of the laborious and physically challenging work,” explains Robertson. “However, because of unique variations in wood and aesthetics, there are some diminishing returns on investment that make it impossible to fully automate the entire process of making high-end acoustic guitars.
“Robots can handle up to 80 percent or 90 percent of some tasks,” Robertson points out. “Human artisans take care of the remaining 10 percent to 20 percent of the work that we can’t accomplish with machines. But, robots have enabled the work that we do by hand to become more refined and specialized.
“Some things just don’t make financial or engineering sense to do with automation,” warns Robertson. “That’s why we will never adopt 100 percent automation and there will always be detail work that humans perform much better.
“Automation has helped us grow by leaps and bounds,” claims Robertson. “For instance, our automatic buffing cells have improved throughput dramatically. It takes a human about 30 minutes to buff a guitar. A robot can accomplish the same task in 15 minutes. Automation enables consistent quality and takes the human element out of potential problems, enabling us get to the root cause of problems quicker.”
Implementing automation in a factory that relies heavily on manual assembly processes and traditional building methods can be challenging. However, Taylor Guitars has always been an innovation-driven company that’s not afraid to push the envelope or adopt new technology.
“Before we introduce any type of automation, we carefully map out the process on the plant floor,” says Robertson. “We also use prototype machines that enable operators to practice running actual production parts. We watch what they’re doing and get feedback, then make any necessary adjustments.”
Robertson also strongly believes in naming robots. For instance, “Buffy” works in the buffing workcell, while “Epoxo” specializes in adhesive dispensing. Taylor assemblers also dubbed a controller “Robocop” and named a server “Panopticon.”
“Our goal is to be more definitive about what each machine does and where it’s located in the factory,” explains Robertson. “Ambiguous nomenclature can be confusing. By using snappy names, everyone knows exactly what you’re talking about. You also get a sense of ownership with it.”
One of Taylor Guitars’ biggest automation success story involves electronics assembly and inspection. The company uses four SCARA robots and three smart cameras to produce its ES2 piezoelectric pickup. The process requires copper to be folded around the part of the pickup assembly that holds piezo crystals.
The assembly process starts with the piezoelectric material fed onto a conveyor from a vibratory feeder. A color-sensing camera determines the polarity of each two-sided piezo block. Any piezo blocks presenting bronze side up are rerouted through the feeder to present with the silver side facing up.

SCARA robots assemble and inspect piezoelectric pickups. Photo courtesy Epson Robots
While the camera determines piezo block polarity, a worker inspects and places pieces of the assembly in the pickup molds, which are arranged on a rotary indexing table. The paper backing is removed from the adhesive by automated tooling custom-made by Taylor’s engineers.
Then, a robot places insulation and installs a printed circuit board (PCB). Another robot is equipped with custom end-of-arm tooling to pick three piezo blocks at a time from the conveyor and place them in the appropriate slots of the pickup assembly. Once the piezo blocks and PCB are installed, the pickup assembly is folded and a robot transports the completed assembly to a wrapping station.
Throughout the assembly process, a combination of machine vision cameras and a laser sensors are used to verify correct placement of the piezo blocks, assess final assembly and confirm the presence of components in the pickup assembly.
The application uses an aluminum carousel fixture that can hold 10 components. The device was designed and fabricated in-house. It’s one of many examples of Taylor’s do-it-yourself mentality that includes making everything from adhesive dispensing systems to vacuum grippers.

Many machines, fixtures and jigs, such as these carousels used to cure mahogany guitar tops before cutting, were designed and made in-house. Photo by Austin Weber
“Due to unique guitar geometries, standard tools and machines just don’t exist,” explains Robertson. “We have some vendors that we rely on, but we still do a lot of things in-house. We typically believe that we’ll have the best solution to address a production challenge or problem, because we’re the closest to the product. When we do have to go find a supplier, we have to start by teaching them how to build a guitar first.”
Robertson and his colleagues continue to subscribe to the philosophy that has fueled Taylor Guitars for the last 50 years. For instance, they’re currently working on two quality control and inspection projects that involve machine vision.
“We’re also keeping an eye on new vision tools equipped with artificial intelligence that will really move the needle,” says Robertson. “We also hope to apply advanced technology to wood grain analysis, which has proven to be quite challenging so far.”
About the Award
The Assembly Plant of the Year award was initiated in 2004 to showcase world-class production facilities in America, and the people, products and processes that make them successful. There is no entry fee. All manufacturers that assemble products in the United States are invited to nominate their plants. The winning plant receives a crystal award and a commemorative banner.
The Assembly Plant of the Year award is sponsored by ASSEMBLY Magazine. The goal of the award is to identify a state-of-the-art facility that has applied world-class processes to reduce production costs, increase productivity, shorten time to market or improve product quality.
All nominees were evaluated by ASSEMBLY’s editorial staff, based on criteria such as:
- Have assembly processes been improved through the use of new technology?
- Has the plant improved its performance by making more effective use of existing technology?
- Has the plant taken steps to reduce production costs?
- Have new or improved assembly processes resulted in increased productivity?
- Has the plant used assembly improvements to reduce time to market?
- Has the plant boosted bottom-line profits and competitive advantage?
- Did operators play a role in the successful implementation of new assembly strategies?
- Has a product been effectively designed for efficient assembly?
- Has the plant attempted to protect the environment and conserve natural resources?
As winner of the 20th annual Assembly Plant of the Year competition, Taylor Guitars received an engraved crystal award and a commemorative banner.
Previous recipients of the Assembly Plant of the Year award were Brose Tuscaloosa Inc. (Vance, AL); GKN Automotive (Newton, NC; Murakami Manufacturing USA Inc. (Campbellsville, KY); GE Appliances (Decatur, AL); Ford Motor Co. (Sterling Heights, MI); AGCO Corp., Jackson, MN; Bosch Rexroth Corp. (Fountain Inn, SC); Polaris Industries Inc. (Spirit Lake, IA); STIHL Inc. (Virginia Beach, VA); Northrop Grumman Corp. (Palmdale, CA); Ford Motor Co. (Wayne, MI); Philips Respironics (New Kensington, PA); Eaton Corp. (Lincoln, IL); Batesville Casket Co. (Manchester, TN); IBM Corp. (Poughkeepsie, NY); Schneider Electric/Square D (Lexington, KY); Lear Corp. (Montgomery, AL); Xerox Corp. (Webster, NY); and Kenworth Truck Co. (Renton, WA).
A nomination form for the 2024 Assembly Plant of the Year award will be available on ASSEMBLY's web site in early January.